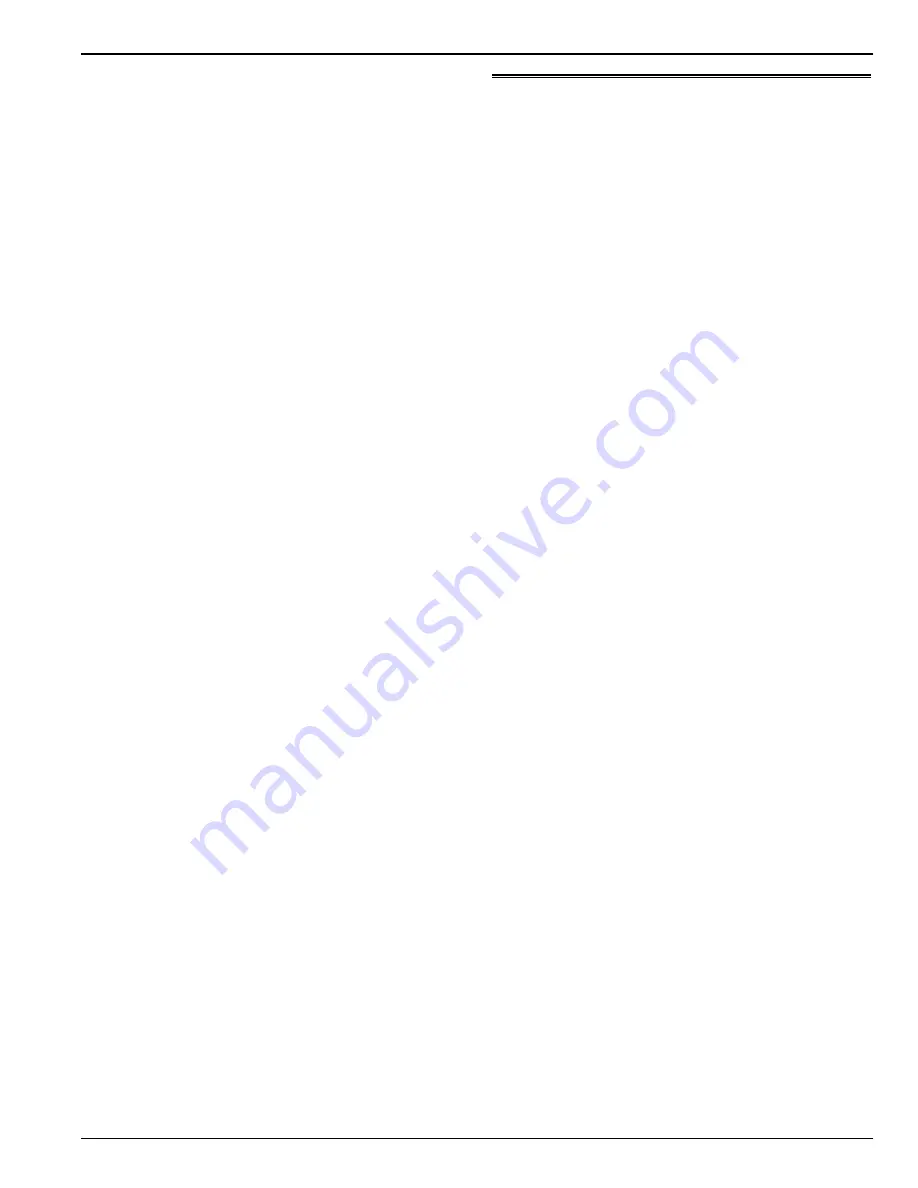
CRR-20 & CRR-40, September 1999
Refrigeration Maintenance and Service Operations
Refrigerant Recovery
6-15
10. Connect the heater and thermistor lead wire harnesses.
11. Evacuate the low side.
12. Open the discharge valve. Then open the receiver tank
outlet valve.
13. Verify that all personnel are clear and connect main power
plug to power supply. Place the unit back in service.
KVQ Valve Replacement
If the valve body is damaged, replace the entire valve.
1.
Connect the unit’s main power cable to the main power
source and switch the refrigeration unit’s On/Off switch to
ON.
2.
Close receiver tank outlet valve and pump down the low
side to 21 kPa, 0.21 bar, 3 psig.
3.
Turn the unit On/Off switch to OFF. Then disconnect the
main power cable from the main power source. Close
(front seat) the discharge service valve.
CAUTION: Any time the discharge valve is front
seated, disconnect the unit power source to pre-
vent accidental compressor start-up.
4.
Unplug the heater and thermistor lead wire harnesses.
5.
Unsolder the valve outlet (compressor side) joint from the
suction line. Unsolder the inlet joint and remove valve.
6.
Clean the tubes for soldering. Position the new valve in
position in the suction line.
7.
Solder both modulation valve connections.
CAUTION: Use a heat sink or wrap the valve with
wet rags to prevent damage to the new valve.
8.
Pressurize the low side and test for refrigerant leaks (see
“Refrigerant Leak Test Procedure” in the Refrigeration
Maintenance chapter of this manual).
NOTE: If pressurizing with nitrogen, front seat
the discharge valve to prevent nitrogen from
entering the refrigerant charge.
9.
If no leaks are found, evacuate the low side and recover
the leak test gas (see “Refrigerant Recovery” in the
Refrigeration Maintenance chapter of this manual).
10. Plug the heater and thermistor wire harnesses into the unit
wire harness.
11. Open the discharge valve. Then open the receiver tank
outlet valve.
12. Verify that all personnel are clear and connect main power
plug to power supply. Start the unit and check the refrig-
erant charge. Add refrigerant as required.
Refrigerant Recovery
Caution: Use only refrigerant recovery equipment
approved for and dedicated to R-134a recovery.
When removing any refrigerant from a Thermo King refrigera-
tion system, use a recovery process that prevents or absolutely
minimizes the refrigerant that can escape to the atmosphere.
Typical service procedures that require removal of refrigerant
from the unit include:
•
To reduce the refrigerant pressure to a safe working level
when maintenance must be performed on high-pressure
side components.
•
To empty the unit of refrigerant when an unknown
amount of charge is in the system and a proper charge is
required.
•
To empty the unit of contaminated refrigerant when the
system has become contaminated.
NOTE: Always refer to specific recovery equipment
Operator and Service Manuals.
Vapor Recovery
1.
Install a gauge manifold set on the unit. Attach the ser-
vice line to the recovery machine and properly purge the
lines. Set the recovery machine for vapor recovery.
2.
Keep unit OFF and mid-seat the discharge service valve.
3.
Turn ON the recovery machine and open (back seat) both
gauge manifold and hand valves.
4.
Continue to operate the recovery machine until unit pres-
sures drop to 0 kPa, 0 bar, 0 psig pressure.
Liquid Recovery
1.
Install a gauge manifold’s low-pressure line to the
Schrader suction service valve in the suction line (near
modulation valve). Attach the manifold’s high-pressure
line to receiver tank outlet valve service port. Attach the
service line to the recovery machine and purge the lines.
2.
Operate the unit and build discharge pressures to approxi-
mately 1380 kPa, 13.80 bar, 200 psig.
3.
Close the receiver tank outlet valve and pump down the
low-pressure side of the system.
4.
Stop the unit.
5.
Set recovery machine for liquid recovery and turn it ON.
6.
Open (back seat) high-pressure valve on gauge manifold.
7.
Operate the recovery machine until the unit system pres-
sures reach approximately 0 kPa, 0 bar, 0 psig.
Содержание CRR-20
Страница 4: ......