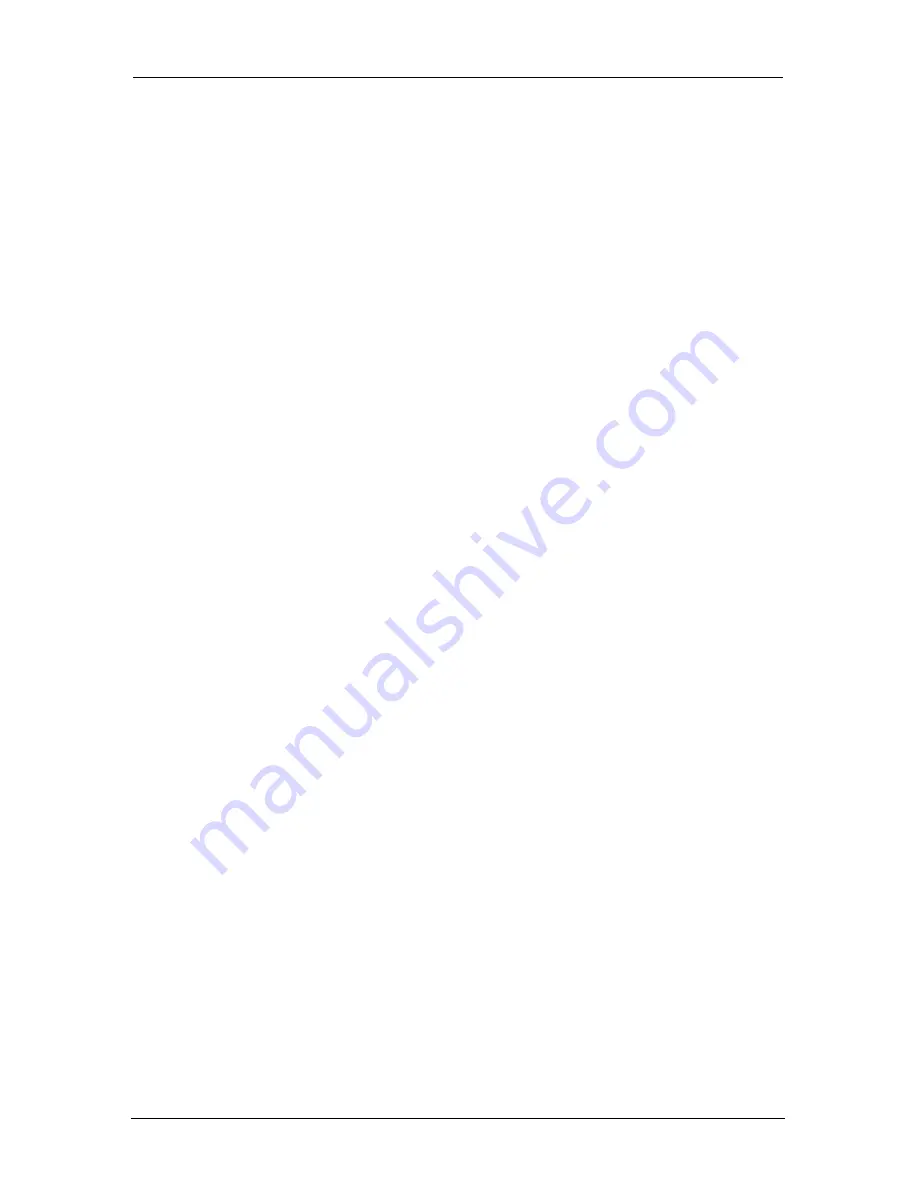
FC-3800 Facility and Installation Guide Section 3: Unpacking and Installation
0101-8604-0, Rev. F
3-3
FC-3800 F & I Guide
2. Remove any skids or pallets.
3. If the cubicle has leveling legs, unlock the locking nuts for the legs and extend them
so that the distance from the bottom of the footpad to the top of the skirt panel is 1.5
inches (38 mm).
Now the vacuum cubicle can be placed. To do so:
1. Using a forklift, lower the vacuum cubicle to the floor near the spot where it is to be
permanently located. Using Figure 3-2, verify that there are adequate clearances for
the other equipment that will be installed nearby. Take care to allow enough space so
that all doors or maintenance panels can be opened fully. If you are installing the
vacuum cubicle through a clean-room wall, make sure that that wall does not obstruct
the opening of the vacuum cubicle’s doors and maintenance panels or prevent them
from opening all the way.
2. Roll the vacuum cubicle on its casters to its permanent position.
3. Level the cubicle as necessary. Some systems have leveling legs that can be
screwed down to accomplish this task.
3.2.3 Positioning the Operator Station
The operator station will normally be placed immediately to the right of the vacuum
cubicle, as shown in the installation drawings (see section 3.4). The operator must have
ready access to the system controls while being able to open and close the vacuum
cubicle door in an unobstructed fashion.
3.2.4 Installing the Power Distribution Box
The power distribution box is normally mounted on a nearby wall. To ensure
unobstructed access as cables are being fed through the bottom of the box, It should be
mounted at least 12 inches (305 mm) above any obstructions. The recommended
distance from the floor to the bottom of the box is 32 inches (815 mm).
On systems supplied with 208 V ac power, the power distribution box will weigh
approximately 176 lbs. (80 kg). On systems supplied with 400 V ac power, a transformer
will be included in the power distribution box, increasing its weight to approximately 300
lbs. (136 kg). Such systems also include a step-down transformer external to the power
distribution box. Perform the following procedure when installing this transformer:
1. Remove the step-down transformer from its packaging.
2. Place the transformer on the floor in its mounting location, which must be within 6 feet
of the power distribution box. If required to do so by local codes, secure the
transformer to the floor, using customer-supplied hardware.
3. Connect power Drop #1 to the input of the transformer.
4. Using the Temescal-supplied cables, connect the transformer’s output to the input for
Drop #1 in the power distribution box.
In nominal 400 V ac installations, connect power Drop #2 directly to the power distribution
box. In nominal 208 V ac installations, connection both Drop #1 and Drop #2 to the power
distribution box.
Before the facility power is actually connected to the power distribution box, make sure
the main power switch on the box is locked in the OFF position. That switch must remain