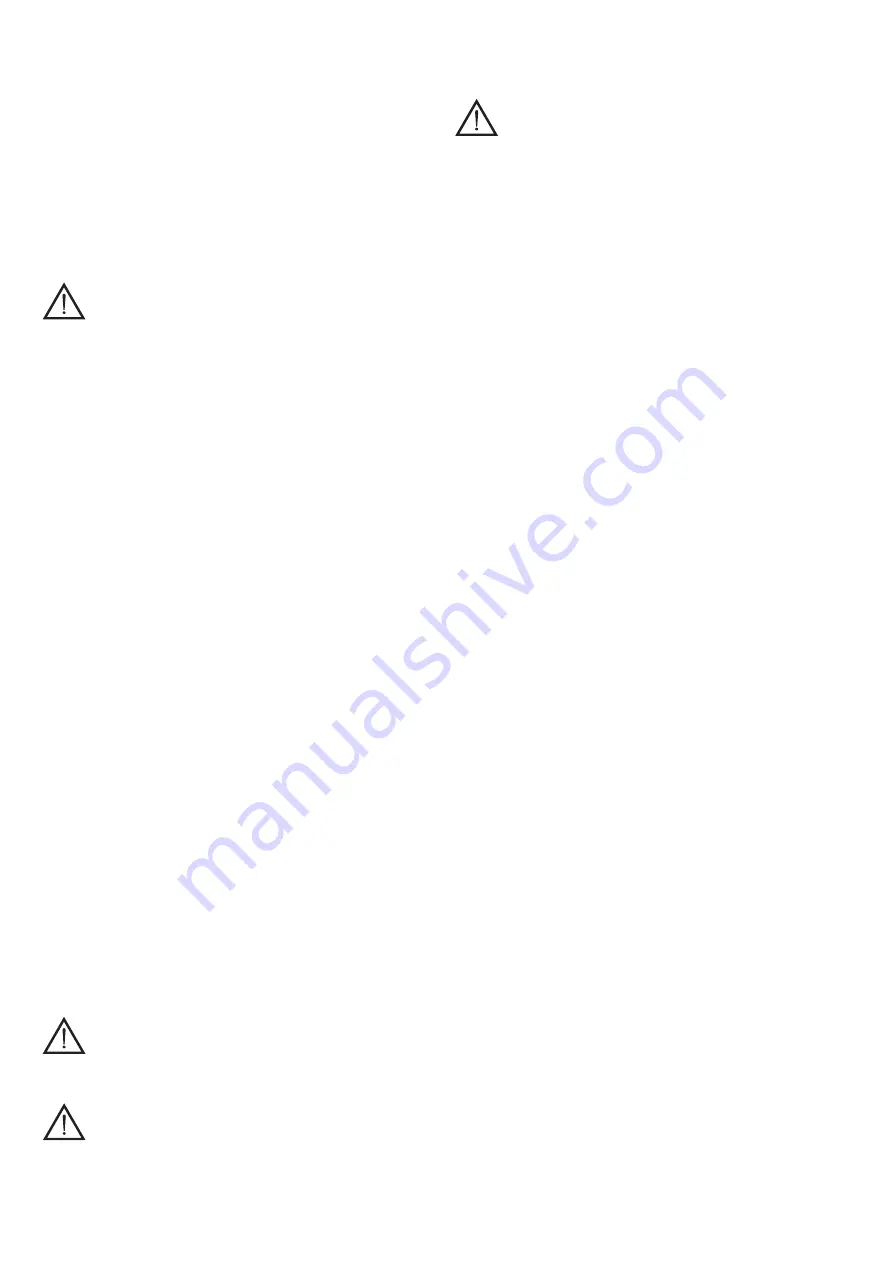
- 7 -
6.3 PROCEDURE
6.3.1. FASTENING THE EARTH CABLE TO THE SHEET METAL
a) Connect the power cable to the electrical mains to power the machine: the
GREEN LED (Fig. C-3) switches on.
b) Use the potentiometer (Fig. C-1) to select the symbol of the earth to spot weld
(Fig. D-26).
c) Bare the sheet metal as near as possible to the point where you intend to work,
for a surface corresponding to the contact surface of the earth nut.
d) Connect the head of the earth electrode to the eyelet of the earth cable (Fig. I).
e) Rest the tip of the earth electrode (Fig. D-25) on the bare sheet metal previously
prepared and close the circuit resting the tip of the studder gun on the bare sheet
metal, then press the trigger.
f)
Check the welding seal of the earth electrode by exerting light traction of the
electrode in an orthogonal direction compared to the surface on which it is welded
and then fasten the earth nut against the sheet metal (Fig. L).
Note: if the earth electrode should easily detach during traction, try to increase the
welding time by rotating the potentiometer clockwise.
6.3.2 SPOT WELDING WITH GUN
Spot welding takes place simply by resting the tool connected to the gun on the part
to weld and pressing the trigger.
ATTENTION!
- To fasten or dismantle the accessories from the chuck of the gun, use two
fixed hex keys to prevent rotation of the chuck.
- If working on doors or bonnets, it is compulsory to connect the earth bar on
these parts to prevent passage of current through the hinges, and however
near the zone to spot weld (long current paths reduce the efficiency of the
spot).
- DO NOT PLACE THE STUDDER ON THE PIECE IF YOU DON'T INTEND TO
START WELDING!
Washer spot welding for earth terminal fastening
(fastening the alternative earth to that of the earth nut)
Select the icon of the washer using the potentiometer.
On the chuck of the gun, assemble the specific electrode (POS. 9, Fig. D) and insert
the washer (POS. 13, Fig. D).
Rest the washer in the chosen zone. Place in contact, in the same zone, the earth
terminal; press the gun button implementing welding of the washer on which fastening
should be carried out using the specific stand (see accessories catalogue, on request).
Slotted washers spot welding
Select the icon of the slotted washer using the potentiometer.
This function is executed by assembling and tightening the electrode holder (POS. 28,
Fig. D) of the gun. Insert the slotted washer (POS. 27, Fig. D) in the electrode holder
and spot weld as previously described.
Spot welding and simultaneous traction of the special washers
Select the icon of the washer using the potentiometer.
This function should be carried out assembling and fully tightening the chuck (POS.
4, Fig. D) on the body of the extractor (POS. 1, Fig. D), couple and tighten the other
terminal of the extractor on the gun. Insert the special washer (POS. 14, Fig. D) on
the chuck (POS. 4, Fig. I), fastening it with the specific screw (Fig. D). Spot weld the
relevant zone, adjusting the spot welding machine as for spot welding the washers
and start traction.
When complete, turn the extractor 90° to detach the washer, which can be spot welded
again in a new position.
Sheet metal heating
Select the icon of the electrode in carbon using the potentiometer.
In this operating mode, the spot welding time is continuous.
Operation duration is therefore manual, being determined by the time for which the
gun trigger is kept pressed.
The intensity of the current is automatically adjusted based on the position of the
potentiometer chosen (current increasing clockwise).
Assemble the carbon electrode (POS. 12, Fig. D) on the gun chuck and block in place
with the ring nut. Touch the area, that was previously bared, with the carbon tip. Work
from the outside to the inside, using a circular movement to heat the sheet which
undergoes work hardening and returns to its original position.
To prevent the sheet from drawing too much, treat small areas and immediately after
wipe using a damp cloth to cool the treated part.
Sheet metal recalculation
Select the icon of the electrode for recalculation (POS. 7, Fig. D) using the
potentiometer.
This function is executed by assembling and tightening the specific electrode (POS.28,
Fig. D) of the gun.
In this position, working with the specific electrode, you can flatten the sheet metal that
underwent localised deformation.
Use the extractor supplied (POS. 1, Fig. D)
Washer coupling and traction
Select the icon of the washer using the potentiometer.
This function is carried out by assembling and tightening the chuck (POS. 3, Fig. D)
on the body of the electrode (POS. 1, Fig. D). Couple the washer (POS. 13, Fig. D),
spot welded as previously described, and start traction. In the end, rotate the extractor
90° to detach the washer.
ATTENTION!
When the work has been completed, place the tools on an insulating surface
and switch off the machine!
7. MAINTENANCE
WARNING! BEFORE CARRYING OUT MAINTENANCE, MAKE SURE
THE MACHINE IS OFF AND DISCONNECTED FROM THE MAINS.
7.1 ROUTINE MAINTENANCE
ROUTINE MAINTENANCE CAN BE CARRIED OUT BY THE OPERATOR.
- adaptation/restoration of the diameter and profile of the electrode tip;
- replacement of the electrodes;
- check the integrity of the power cable;
- check the integrity of the gun and output cables.
7.2 SPECIAL MAINTENANCE
SPECIAL MAINTENANCE MUST ONLY BE CARRIED OUT BY TECHNICIANS WHO
ARE EXPERT OR QUALIFIED IN AN ELECTRIC-MECHANICAL AMBIT.
WARNING! BEFORE REMOVING THE SPOT WELDING MACHINE OR
GUN PANELS AND ACCESSING THE UNIT, MAKE SURE THE SPOT WELDING
MACHINE IS SWITCHED OFF AND DISCONNECTED FROM THE MAIN POWER
AND PNEUMATIC SUPPLIES (if present).
Carrying out checks while the inside of the spot welder is live can cause serious
electric shock due to direct contact with live parts and/or injury due to direct contact
with moving parts.
Periodically and as frequently as required by the use and environmental conditions,
inspect inside the spot welder and clamp and remove the dust and metal particles that
have deposited on the transformer, diode module, power terminal board, etc. using a
blast of dry compressed air (max. 5 bar).
Do not direct the jet of compressed air onto the electronic circuit board; if necessary
clean with a very soft brush or suitable solvents.
At the same time:
- Make sure the wiring does not show signs of insulation damage or loose-oxidised
connections.
- Make sure the screws that connect the transformer secondary with the output bars
/ wires are tight and that there are no signs of oxidation or overheating.
8. TROUBLESHOOTING
SHOULD MACHINE OPERATION NOT BE SATISFACTORY, AND BEFORE
CARRYING OUT MORE SYSTEMATIC CHECKS OR CONTACTING YOUR
TECHNICAL ASSISTANCE CENTRE, MAKE SURE THAT:
- With the power cable connected to the mains, the GREEN LED is on; if this is
not the case, the problem is in the power line (cables, plug and socket, fuses,
excessive voltage drop etc.).
- The YELLOW LED is off: on the contrary, wait a few minutes for cooling and to
reset functionality of the machine;
- The elements that are part of the secondary circuit (gun - cables) are not inefficient
because of loose screws or oxidation.
- The welding parameters are suitable for the work to be carried out
- After having carried out maintenance or repairs, restore the connections and wiring
as they were before, making sure they do not come into contact with moving parts
or parts that can reach high temperatures. Band all the wires as they were before,
being careful to keep the primary high voltage connections separate from the
secondary low voltage ones.
Use all the original washers and screws when re-closing the structural work.
Содержание 828129
Страница 82: ... 82 1 2 1 2 3 7 1 2 4 3 5 6 8 U1 Hz kVA kVA Sp S50 U1 n V kA kA U20 I cc 2 I p 2 V 3 4 FIG A FIG C FIG B ...
Страница 83: ... 83 FIG D ...
Страница 84: ... 84 FIG E FIG F FIG G FIG H ...
Страница 85: ... 85 FIG I FIG L ...