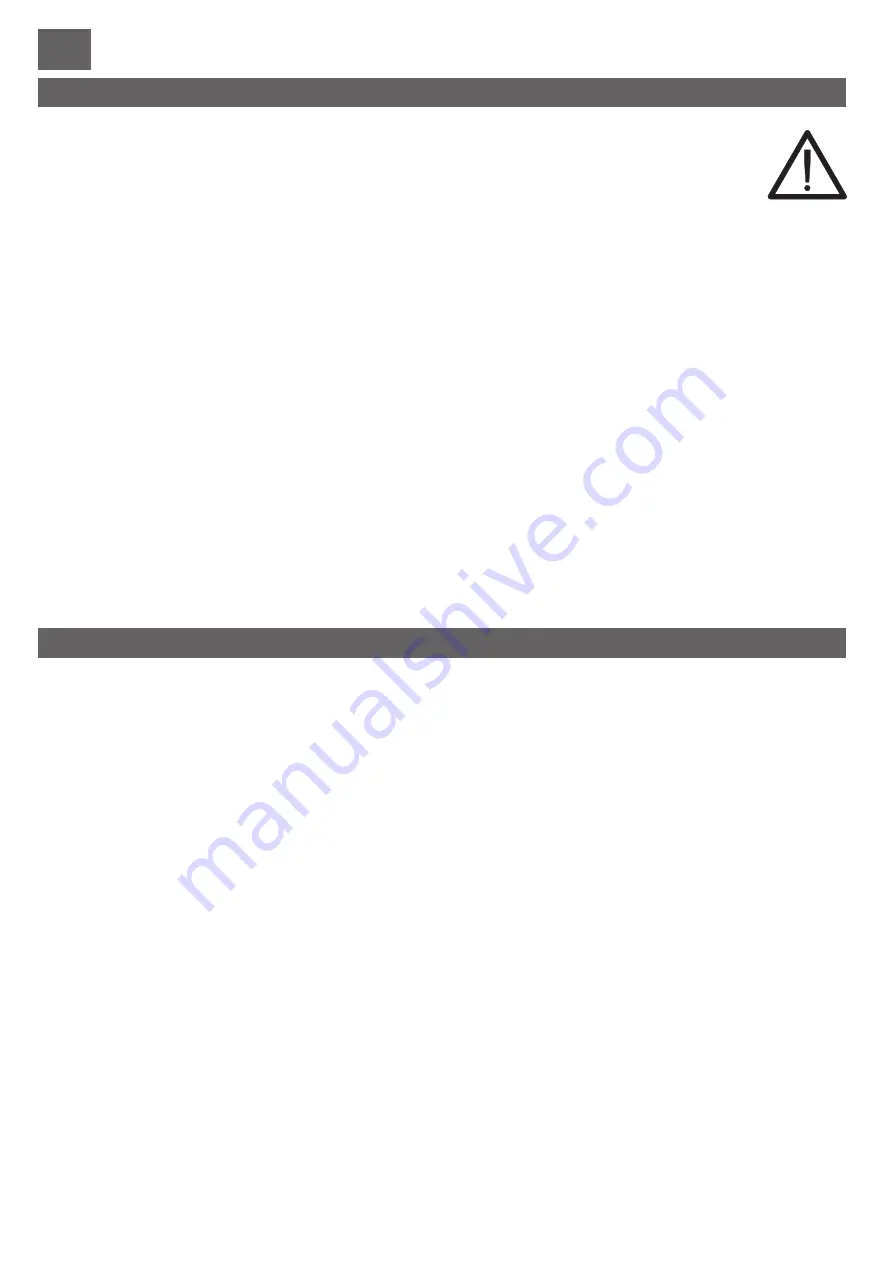
GB
MECHANICAL STOPS ADJUSTMENT
Models ASY feature an internal system for mechanical stroke limitation composed of adjustable and independent stops (parts
11 and 14 in fig. A), one for the opening stroke and one for the closing stroke (optional).
Using these internal stops can be convenient when there are no stroke end stops or when there is no other way to limit the
stroke of the gate leaf. Where permitted by the installation it is anyway advisable to use or install gate leaf limit stops.
The adjustment is extremely simple:
- remove the screws (part 6 in fig. A) and remove the cover (part 4 in fig. A).
- fit the mechanical stop to the lead screw (fig. C) while keeping the fixing screws backed off.
- move the leaf towards the actuator maximum stroke limit and fully tighten the screws of the mechanical stops
- perform opening and closing cycles to check the stops are correctly positioned and then refit the actuator cover.
- bring the gate leaf to its fully closed position
- bring the actuator to its closed position (a few millimetres before the maximum extension)
- place the front bracket on the gate leaf and mark the holes
Before final fixing (screws or welding) perform a manual opening and closing movement and check the actuator is level (fig.
G).
2
8
9
1
3
7
4
6
5
GB
PRELIMINARY CHECKS AND IMPORTANT SAFETY NOTES FOR INSTALLATION
BRACKETS FIXING
Before reading the installation instructions, take note of the following basic concepts:
- the joint brackets (front and rear) must be mounted correctly at two different heights.
- the brackets supplied can be welded directly to the structure or secured with screws and screw anchors, provided
the system is able to withstand the forces imparted: by the actuator, by manual movement of the gate and (in certain
conditions) by the wind.
- the position of the brackets establishes the maximum opening angle and the length of the actuator's linear stroke;
consider that the longer the stroke of the lead screw, the greater the torque and the smoother the movements of the
gate leaf; on the contrary, with a short stroke, movements may be more abrupt and there will be less torque available.
Table TAB1 shows several examples of bracket positions; the measurements are guideline and should be used solely to
prepare for installation. Check which of the possible solutions is applicable to your automation project and perform a few
manual trials before fixing the brackets.
Start by defining the position of the rear bracket by plotting the values in the table (TAB1) horizontally and observing fig. D. For
example: measuring dimension "C" (e.g. 90 mm) makes it possible to calculate dimensions "A" (e.g. 155 mm) and "B" (e.g.
155 mm); for other factors, consider that dimension "B" can vary by +/- 20mm and dimension "A" can be modified by choosing
a different hole in the bracket. Assess these tolerances because the more dimensions "A" and "B" are similar, the smoother the
movements of the gate leaves.
The rear brackets are supplied in two parts (with non-welded plate) offering the freedom to: shorten or tilt the bracket or fix the
drilled bracket directly to the gate post (figs. E1, E2). For fixing with screw anchors and/or screws the bracket must be welded
to the plate as shown in fig. E (standard installation).
Even if the structure of ASY is designed to adapt to imperfections or structural deterioration of the fixing, the importance of
using maximum precision when levelling the brackets (fig. E3) cannot be underestimated.
The table (TAB1) contains a reference to different dimension "D" for the two models ASY 3 and ASY 5, and columns with fixed
dimensions "E" (maximum centre distance) and maximum stroke "F".
The height of the brackets is established easily using a spirit level; the front bracket must be 55 mm lower (fig. F); in addition,
calculate the final height of the actuator such as to allow correct outlet of the electrical cables or choose a higher position to
reduce the accumulation of dirt, grit and moisture (fig. G).
After having secured the rear bracket and marked the height of the front bracket, you can calculate distance "D" with the aid of
the table (TAB1) or proceed as follows:
- secure the actuator as shown in fig. H
- fix the front bracket to the actuator
Before proceeding with installation, checks should be made on:
1. the solidity of the existing structure (posts, hinges and leafs) in relation to the force generated by the motor.
2. the provision of mechanical stops of suitable strength at the ends of the gate opening and closing strokes.
3. the bottom wheel/rail system and upper roller/guide system to ensure there is no rubbing or excessive
clearance.
4. the disabling of any manual locks.
5. the condition of any wiring already installed in the system.
Important safety notes:
1. The automation system must be installed to good workmanship standards by qualified staff meeting the legal
prerequisites and in accordance with machinery directive 2006/42/EC and the EN13241-1, EN12453 and EN12445
standards.
2. Analyse the risks of the automation system and adopt any appropriate safety and warning measures.
3. Install controls, such as the key-operated selector switch, in such a way that the user is not in a hazard zone.
4. Affix the CE nameplate or label containing the hazard information and ID data of the automation.
5. Consign the instructions for use, safety information and EC declaration of conformity to the final user.
6. Ensure that the user has understood how to operate the automation correctly in automatic, manual and emergency
modes.
7. After installation, try out the automation safety, signalling and release devices several times.
8. Inform the user in writing (for example, in the operating instructions):
a. of any residual risks for which no protection is provided, and foreseeable misuse.
b. That the power supply must be disconnected before the gate is released, when performing routine maintenance or
during cleaning of the automation area.
c. That the automation must be inspected frequently for visible damage, notifying the installer at once if any is found
d. That children must not be allowed to play in the immediate vicinity of the automation
e. That the radio remote controls and other control devices must be kept out of the reach of children.
9. A maintenance plan must be provided for the system (at least every 6 months) and the work done recorded in a log.
19
20
RELEASE AND LOCK PROCEDURE (irreversible models only)
These two operations are only required in the event of a fault or electrical power failure; the user or person responsible must be
instructed by the installer, who will provide them with a copy of these instructions, which must be kept in a safe place together
with the release key.
Before performing either of these procedures, make sure you disconnect the entire automation from the electrical
supply, even if it is currently unpowered due to an outage.
Any electric locks must be specified and released for manual operations.
RELEASE
:
1)
disconnect the electrical supply;
2)
open the rubber cap, insert the key and turn it clockwise;
3)
raise cover;
4)
grasp the lever and turn it towards the front of the actuator; the gate leaf can now be moved manually.
5)
The leaf can remain unlocked and the cover can be refitted by simply removing the lever.
LOCK
:
6)
grasp the lever and rotate towards the rear of the actuator; at this point the leaf is locked and can only be moved
electrically.
7)
After this operation always close the cover;
8)
and turn the key to lock it in place;
9)
take care to reclose the rubber cap
protecting the lock.
For REVERSIBLE models the gate can be operated manually after having released exclusively any electric locks
fitted.
Содержание ASY Series
Страница 2: ...1 Fig A I F E GB D NL 5 6 7 1 2 3 4 8 9 10 11 12 13 14 15 16...
Страница 31: ...NOTE...