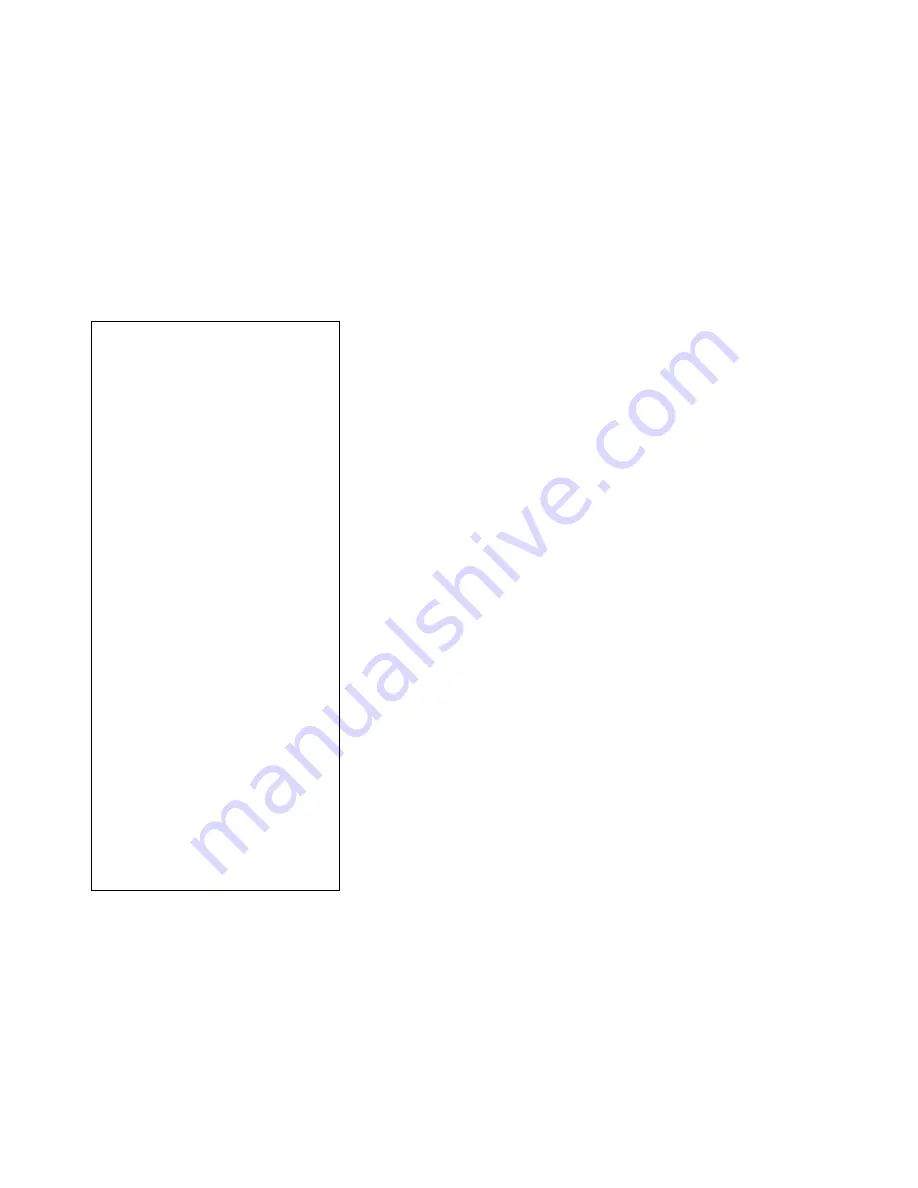
PID control
80
Event control “overwrites” the results of speed control from other control processes. Hence, a
set event can block the absolute value control or differential control.
Example
: Keeping the
collector temperature at 60°C with the absolute value control is blocked when the cylinder has
already reached 50°C at the top = the fast provision of DHW is complete and is now to be con-
tinued with full volume flow (and hence a lower temperature but slightly better efficiency). To
do so, a value that automatically requires full speed has to be entered as the new set tempera-
ture in the event control (e.g. coll = 10°C).
If absolute value as well as differential control are switched off (output: maximum correcting
variable), then there will be a switch from maximum correcting variable to the value that com-
plies with the event control when the event control is activated.
Entire menu view:
DES: PID CTRL
FUNCTION STATUS:
INPUT VARIABLE:
OUTPUT VARIABLE:
ABSOL.VAL. CTRL:
MODE: std
Speed increases as temperature increases
T.abs.ACT: 50.3 °C
The sensor is currently measuring 50.3°C
T.abs.SET: 50 °C
The sensor is kept at 50°C
DIFFERENTIAL CONTROL:
MODE: std
The speed increases with the difference T.diff+ to T.diff-
T.diff+.ACT: 50.3 °C
The sensor at the source is currently measuring 50.3°C
T.diff-.ACT: 42.7 °C
The reference sensor is currently measuring 42.7°C
SET DIFF 8.0 K
The desired difference (T.diff+ to T.diff-) should be 8 K
EVENT CONTROL:
MODE: off
No event control is allowed. If
std,
then:
COND.: ACT < THRES
Condition
T.activACT: 48.1 °C
The sensor that activates the function is measuring 48.1°C
T.activTHR: 60 °C
Event control should launch at 60°C on (act-) sensor
(fixed activation threshold, no hysteresis)
T.ctrl ACT 50.3 °C
The sensor control starting with the event is displaying 50.3°C
T.ctrl SET 90 °C
Starting with this event, the sensor is controlled to 90°C
CORRECTVAR.:
maximum: 30
Highest admissible speed stage is the stage 30 (full run)
minimum: 8
Lowest admissible speed stage is stage 8 (0 also admissible)
current: 14
Stage 14 is currently output
CONTROL PARAMETER:
P: 10 I: 0 D: 0
PID shares for stable operation
The control parameters P=8, I=5, and D=2 generally ensure stable operation. If the speed periodically
changes (generally for 20-30 seconds), I and D should be set to zero for simple systems. Drawback:
A low, constant temperature is incorrectly controlled for, and the system is a bit slower.
If a speed control is used in service water systems, the PID settings must be determined in a test (see
"stability problems") to ensure optimal performance.