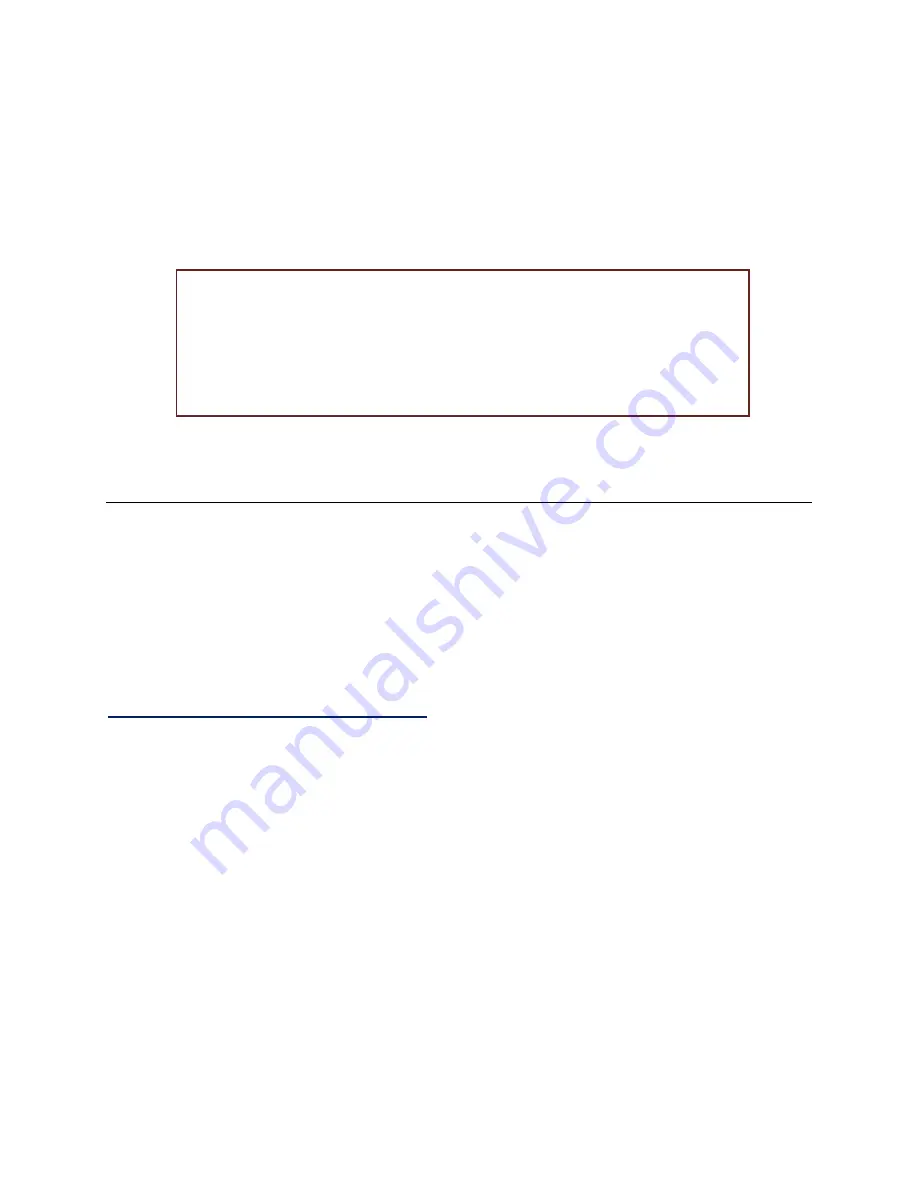
A quick tap on the
MENU
button (≡) will take you to the
Model Setup
menu. If you hold it too
long you go to the
Radio Setup
menu -- just a tap. Now tap the
PAGE
button repeatedly to flip
down thru the screens. A long press on the
PAGE
button will move you up a screen. Almost all
of our robot setup will be done on three screens:
INPUTS
,
MIXER
, and
OUTPUTS
.
In this guide we will use these three screens to set-up the following common combat robot
functions:
As a bonus I’ll toss in a feature from a fourth model setup screen that will allow you to command
servo motion up to 150% of normal range. Let’s get to work.
The Mixer Screen -- Linking Inputs to Outputs
The mixer screen accepts input signals -- from the transmitter sticks, switches, and knobs -- and
assigns them to output channels that will be sent to the receiver. Multiple inputs may be
assigned to individual outputs to create channel ‘mixes’, and the signals may come direct from
the inputs or after they have been modified by the
INPUTS
screen.
Constructing a Single Stick Drive Mix
With conventional transmitter firmware it’s a simple matter to establish single-stick control of
throttle and steering -- just go to the mix menu and turn on ‘Elevon’. With OpenTX firmware
there are no pre-defined mixes you can just turn on – you must define your own mixes.
To properly control motion in a skid-steer robot we require the left and right motors to respond to
the Elevator stick axis (right stick up/down) by spinning in opposite directions (one clockwise,
one counterclockwise) to move the robot forward and back, and we need the left and right
motors to respond to the Aileron stick axis (right stick left/right) input by spinning in the same
direction (both clockwise or both counterclockwise) to rotate the robot right or left. We’ll set up
CH1
to control the left side motor controller and
CH2
to control the right side.
Page down thru the
Model Setup
menu to the
MIXER
screen. With default settings (Mode 2,
AETR) your mixer screen should look like this:
1. A single-stick throttle and steering mix.
2. Assign an output channel to a toggle switch.
3. Create a steering sensitivity dual-rate switch.
4. Program a switch to correct stick response on an inverted robot.
5. Limit servo motion range to prevent lifter stall.
6. Reverse the response of individual receiver outputs.