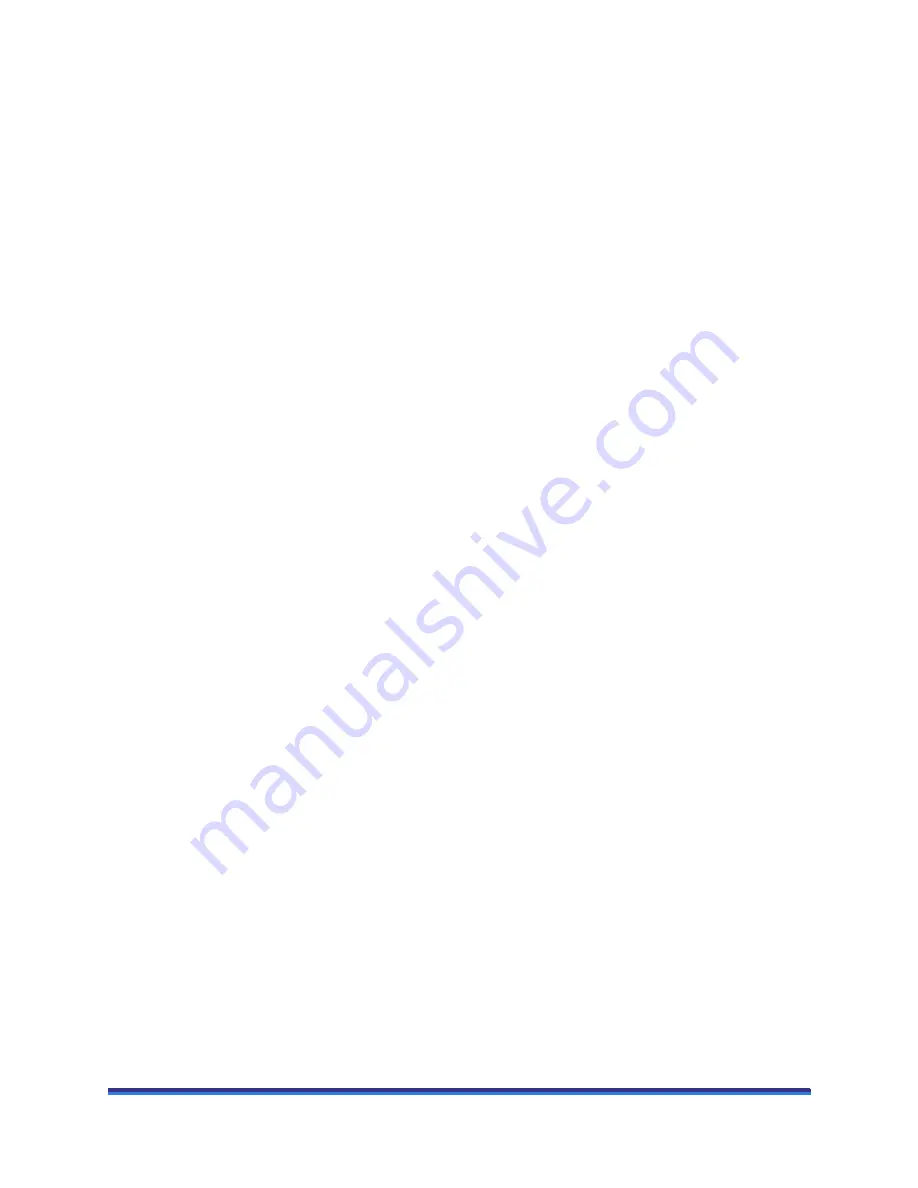
ARES-G2 Getting Started Guide
Page 66
Torque Calibration
Torque Calibration ensures that the transducer is accurately measuring torque. The calibration involves
hanging a precision weight from the calibration geometry, a 2.5-centimeter moment arm that is mounted on
the transducer, over a pulley during calibration. The applied torque is therefore the product of the weight
and the 2.5-cm moment. For example, hanging a 200 g weight applies a torque of (200 g)(2.5 cm) = 500
g·cm (0.049 N-m).
Normal Force Calibration
Normal Force Calibration ensures that the transducer is properly measuring normal force. The calibration
involves hanging a precision weight from a hook on the calibration geometry, which is mounted on the
transducer during calibration. The applied normal force is the amount of weight applied to the calibration
geometry. For example, hanging a 1000-g weight applies a normal force of 1000 (9.8 N).
Phase Angle Check
The phase angle correction compensates for possible phase shifts that may be added to torque and strain
due to instrument electronics. Once the correction is determined, it should remain constant for the life of
the system. The phase angle correction is computed and entered at the factory before the instrument is
shipped, and should not have to be adjusted under normal operating conditions.
Phase angle is checked at the time of installation and is recommended to be rechecked once a year during a
scheduled preventative maintenance visit. A Torsion Rectangular Clamp Set (p/n 403220.901) is required
if you wish to periodically check the phase angle, or perform a phase angle calibration outside of a sched-
uled preventative maintenance visit.
To check the phase angle using the ARES-G2, a Dynamic Frequency Sweep is run on a steel sample that is
loaded into a torsion rectangular geometry. Recall that a purely elastic sample has a phase angle of zero
degrees. The phase angle of steel is near zero. If the values obtained from this test are abnormal, please
contact Technical Services for further assistance.
System Check Using PDMS
Included in the calibration kit (supplied with the instrument) is a jar of PDMS. PDMS (polydimethyl silox-
ane) is a rheological reference material that is used to verify the correct operation of the test station in addi-
tion to the various types of calibration. A PDMS test should be run periodically to ensure proper operation
of the instrument. It should also be run as a preliminary diagnostic any time there is a question regarding
instrument performance.