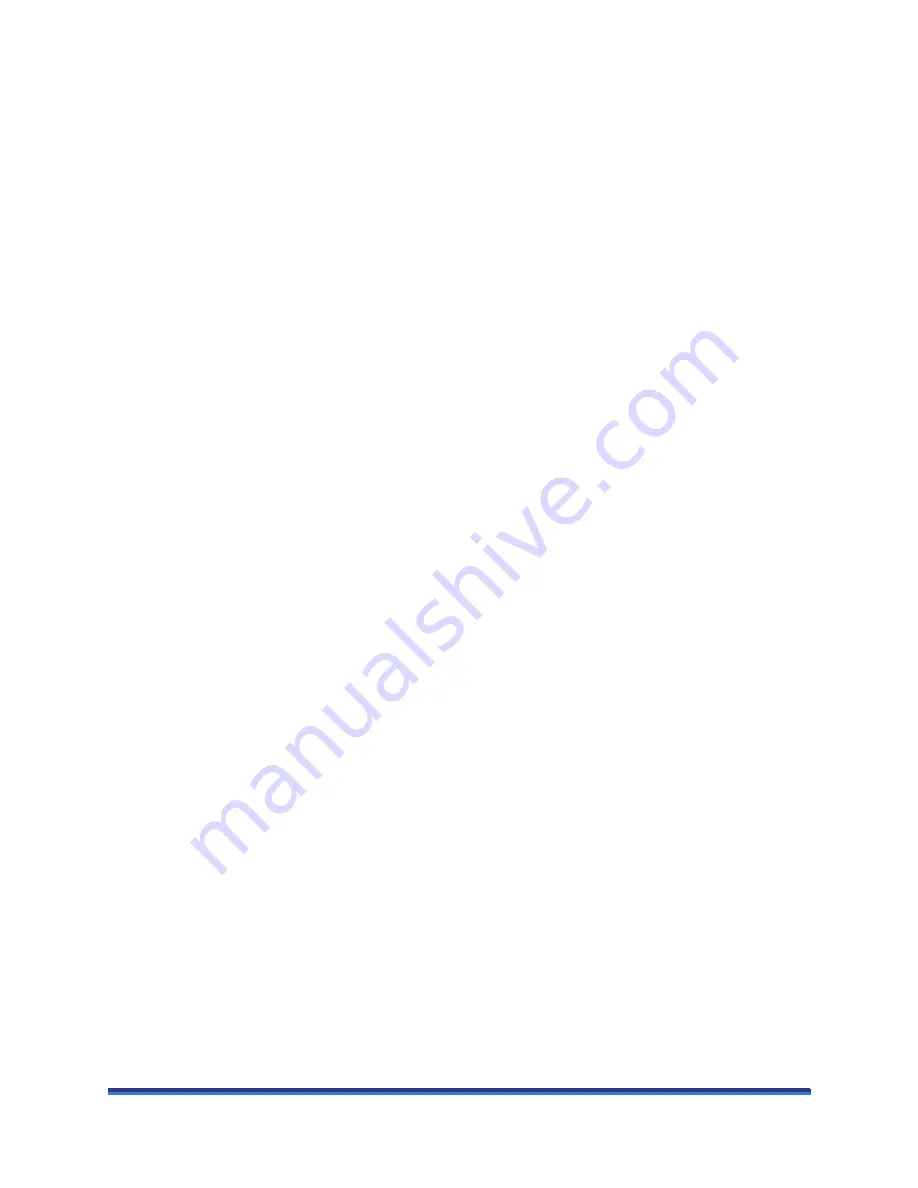
ARES-G2 Getting Started Guide
Page 67
Selecting and Installing a Geometry
General Recommendations
Although the physical properties of the sample generally dictate appropriate sample geometry, it is some-
times possible to test a given sample using more than one geometry.
Ideally, the test results should be identical in the different geometries. However, there exist experimental
limitations that may make testing in one geometry preferable to testing in another. Additionally, factors
such as anisotropy and differences in strain dependence may yield inconsistent results for different geome-
tries.
Recommendations for selection of a geometry based upon sample type are as follows:
•
Fluids, Suspensions and Emulsions: Low viscosity fluids, or suspensions of limited stability can be
tested using either the
Concentric Cylinder
or
Double Wall Concentric Cylinder geometry
. Higher
viscosity fluids, and thicker suspensions and emulsions can be tested using
Parallel Plates
, or
Cone
and Plate geometries
.
•
Solid Samples, including Thermosets, Thermoplastics, and Elastomers:
These materials can be tested
using the
Torsion Rectangular geometry
. Several inserts are available to accommodate a variety of
sample thicknesses.
•
Polymer Melts and Soft Solids: Melts can be tested using the
Parallel Plate
or
Cone and Plate geom-
etries
. The
Extensional Viscosity Fixture
or EVF is an option for testing elongation viscosity of poly-
mer melts and high viscosity viscoelastic fluids.
•
Thermosetting Resins and other Curing Studies: These materials are best tested in a
Parallel Plate
geometry
. Disposable plates are available for curing studies, or other geometry reactive materials.
Testing Limits and Compliance
Instrument compliance is defined as displacement, in radians, per unit of applied torque. Stiffness is the
reciprocal of compliance. Transducer compliance is the transducer shaft angular displacement divided by
the torque applied to the transducer. Shaft displacement is measured by a position sensor on the transducer
shaft. Sample compliance is sample displacement divided by the force applied to the sample.
Because the transducer is not an infinitely stiff device, both the transducer and sample exhibit compliance.
Since the transducer can be deformed along with the sample, some of the strain that is commanded
deforms the sample, and some of the strain may deform the transducer. If the transducer deformation is
large, relative to the sample deformation, this may lead to errors in moduli stiffness.
The ARES-G2 utilizes an online hardware correction scheme to adjust for transducer compliance. The sys-
tem determines sample deformation (strain) by taking the difference between the (measured) motor and
transducer displacement signals.
Under “ideal” conditions, the sample deformation is relatively large, and as such, the transducer displace-
ment is much smaller than the motor displacement applying the torque. The difference between the two
deformations (which is used to obtain sample displacement) is therefore a large number, and the relative
error associated with the measurement is small. However, this error becomes significant when very stiff
samples are tested, and the transducer displacement becomes close to the motor displacement. In most
cases, the automatic online hardware correction scheme mentioned above eliminates the error. However, if
the measured strain value is significantly smaller than the commanded strain value; the data are likely
affected by transducer compliance.