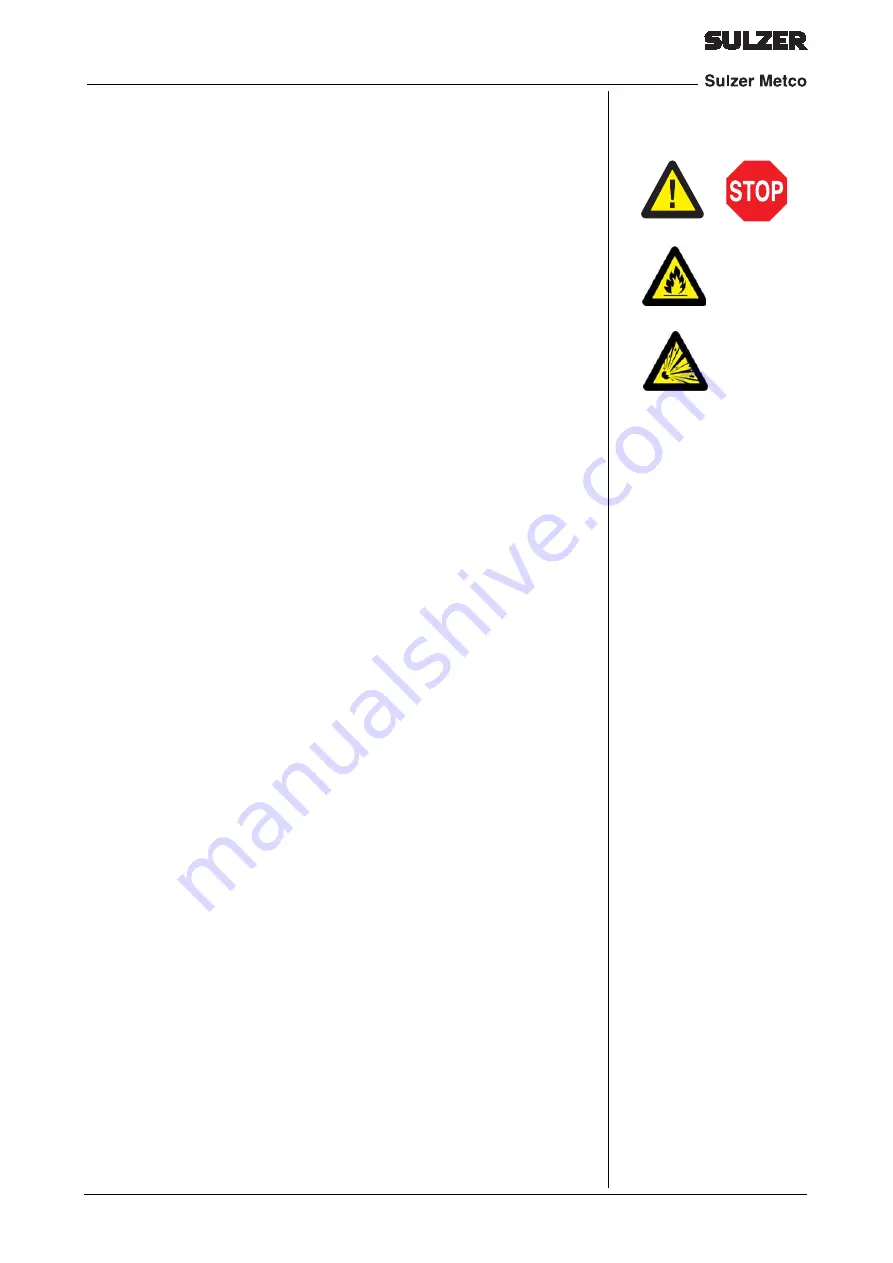
General Safety Instructions
1-13
Revision 1/10/08
1.7.7 Dust combustion and dust explosion hazard
Caution!
Proper protection from dust combustion and dust explosions is only
possible with sufficient knowledge of the hazards and the measures to
be taken to prevent these.
•
The safest method of protection is to prevent any accumulation of
dust at the workplace and within the extraction system and also in
the pipe system of the filter.
(Primary Explosion Protection)
•
For cleaning purposes it is best to use an industrial vacuum
cleaner according to category C.
•
Dust must not be swirled up. In the right concentration with air
oxygen, an explosive dust/air mixture can form which through
initial combustion can lead to an explosion.
•
Avoid additional ignition supplies.
•
The electric arc and the spray jet with the molten metal particles is
an unavoidable ignition supply. You can mitigate this by never
directing the spray jet at an accumulation of dust.
•
Do not extinguish burning dust with water.
•
Use a powder extinguisher with metal fire extinguishing powder
according to fire class D. Take advance precautions by seeking the
advice of the fire service.
•
Moist or wet dust from zinc, aluminum, magnesium and alloys of
these tend towards spontaneous combustion. A chemical reaction
with water leads to a build-up of hydrogen, especially with
aluminum. Suitable safety measures must be taken when filtering
and storing the dust.
•
Aluminum and aluminum alloy dust and other rapidly reacting
metallic dusts should only be extracted using filter systems
designed for the purpose. These dust/air mixtures are easily
combustible and explosive.
•
The relevant national regulations must be observed.
Содержание ECO ARC 600
Страница 6: ......
Страница 47: ...ECO ARC 600 5 1 Revision 1 10 08...
Страница 74: ...ECO ARC 600 7 6 Revision 1 10 08...
Страница 75: ...ECO ARC 600 8 1 Revision 1 10 08...
Страница 88: ...ECO ARC 600 8 14 Revision 1 10 08 T2 K1 A10 F4 D10 F2 1 F2 2 F3 K3 F21 F22 F23...
Страница 94: ...ECO ARC 600 9 2 Revision 1 10 08 9 2 Circuit diagram...