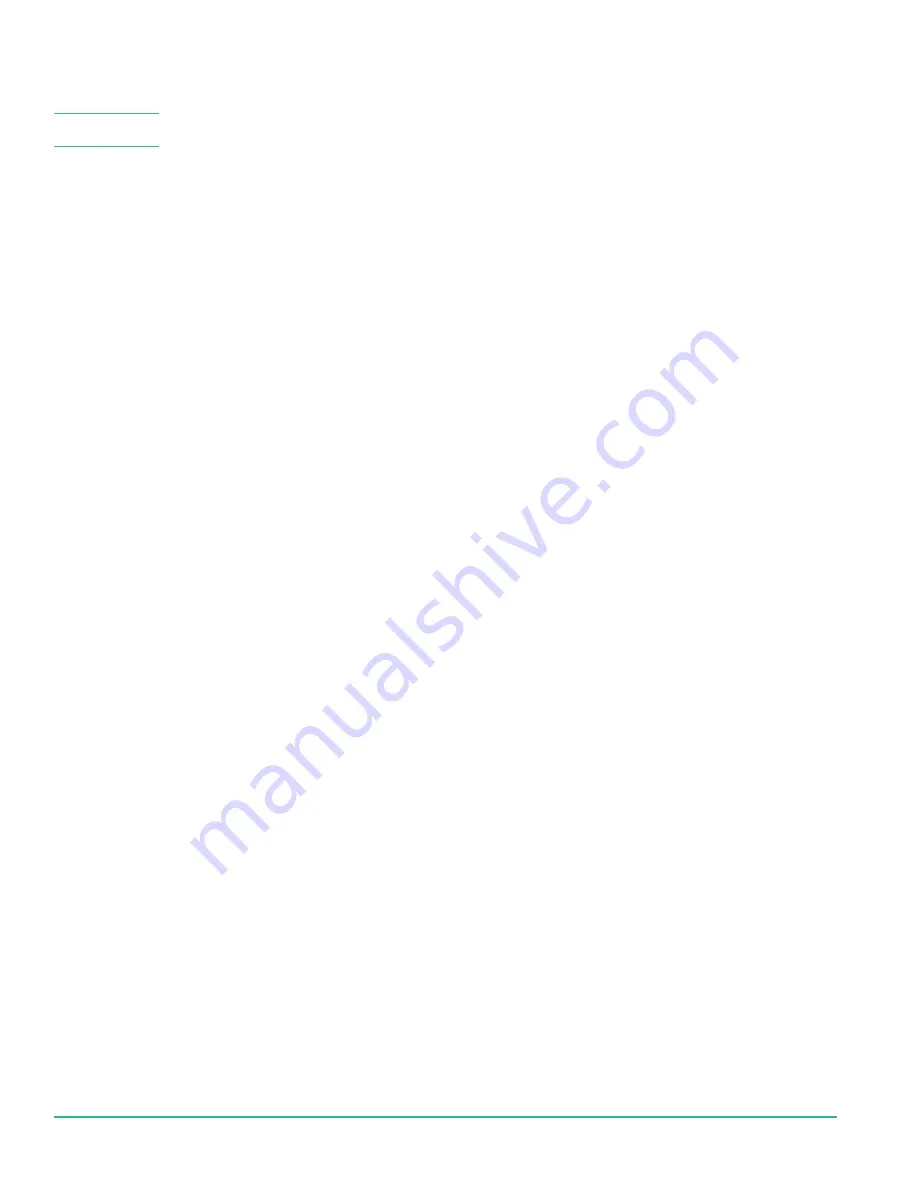
48
MAINTENANCE
6.5
COMPRESSOR LUbRICANT
Refer to
Chapter 8.4 Compressor Lubricants on page 62
for additional information about lubricants offered
by Sullivan-Palatek.
CAUTION!
Never mix synthetic lubricants with hydrocarbon lubricants. Never mix synthetic lubricants
manufactured from different base products. Severe damage to the compressor system may result.
Lubricant manufacturers include a variety of additives in the blending process to enhance lubrication,
product life and performance. Mixing different types or brands of lubricants is not recommended due to the
possibility of a dilution of the additives or a reaction between additives of different types.
Environmental conditions in the area of compressor operation such as the presence of reactive gases or
vapors in the air may lead to chemical changes and premature degradation of the lubricant. The useful life of
synthetic lubricants may extend the normally recommended drain and replace period; however, the user is
encouraged to closely monitor the lubricant condition and to participate in an oil analysis program with the
fluid supplier.
6.5.1 CHECK
The oil level should be checked daily, when the compressor is off.
1.
Shut down the compressor (or check before the compressor is turned on).
2.
Wait two minutes after the compressor stops to allow the pressure to be relieved and the oil to settle.
3.
Observe the oil level in the fluid sight glass. It should be ½ to ¾ full.
4.
While the compressor is running, the oil should be visible in the sight glass and the compressor not
running hot.
6.5.2 FILL
Oil must be added to the compressor if the oil level is below the sight glass when the compressor is running.
1.
2.
Verify that compressor has no air pressure prior to removal of component parts.
3.
Clean any dirt from around the oil fill cap.
4.
Loosen the cap to make sure any remaining pressure is relieved through the vent hole, then remove.
5.
Add oil so that the sight glass reads ½ to ¾ full.
6.
Replace cap and tighten securely.
6.5.3 CHANGE
Change the compressor oil as indicated by
.
REMOVE OLD LUbRICANT
1.
2.
Remove the drain plug from the end of the drain line at the bottom of the sump tank.
3.
Open the drain valve and allow all oil to drain. Discard old oil per local codes.
4.
Remove any remaining oil by turning the compressor unit by hand.
ADD NEW LUbRICANT
1.
Clean any dirt from around the oil fill cap.
2.
Loosen the cap to make sure any remaining pressure is relieved through the vent hole, then remove.
3.
Add oil so that the sight glass reads ½ to ¾ full.
4.
Replace cap and tighten securely.
6.5.4 CONVERT
When converting to a different type of oil in the compressor, use the following procedures to ensure the
different oil types do not mix.
REMOVE OLD LUbRICANT
1.
2.
Remove the drain plug from the end of the drain line at the bottom of the sump tank.
3.
Open the drain valve and allow all oil to drain. Discard old oil per local codes.
Содержание 15D
Страница 6: ...vi About This Manual ...
Страница 12: ...4 Introduction ...
Страница 20: ...12 Specifications 2 2 DIMENSIONS OPEN BASE MOUNT AIR COOLED Figure 2 1 GA 15 40D AC BM OPEN ...
Страница 21: ...13 Specifications 2 3 DIMENSIONS ENCLOSED BASE MOUNT AIR COOLED Figure 2 2 GA 15 40D AC BM VERT ENCL ...
Страница 22: ...14 Specifications 2 4 DIMENSIONS OPEN BASE MOUNT WATER COOLED Figure 2 3 GA 15D 30D WC BM HORZ OPEN GAUGES ...
Страница 23: ...15 Specifications 2 5 DIMENSIONS ENCLOSED BASE MOUNT WATER COOLED Figure 2 4 GA 15 40D WC BM ENCL GAUGES ...
Страница 24: ...16 Specifications 2 6 DIMENSIONS OPEN PLATFORM MOUNT AIR COOLED Figure 2 5 GA 15 40D AC PLAT OPEN GAUGES ...
Страница 25: ...17 Specifications 2 7 DIMENSIONS ENCLOSED PLATFORM MOUNT AIR COOLED Figure 2 6 GA 15 40D AC PM VERT ENCL ...
Страница 30: ...22 Specifications 2 12 PIPING AND INSTRUMENTATION AIR COOLED Figure 2 11 GA P I S R02 ...
Страница 31: ...23 Specifications 2 13 PIPING AND INSTRUMENTATION WATER COOLED Figure 2 12 P I 15 40 WC GAUGES R00 ...
Страница 34: ...26 Specifications ...
Страница 66: ...58 Troubleshooting ...
Страница 84: ...76 Parts Catalog 8 10 AIR INLET ASSEMBLY 15 30HP 13 12 11 13 12 4 5 2 3 14 1 Figure 8 6 AS805 030D7H TE R00 ...
Страница 88: ...80 Parts Catalog 8 12 AIR INLET ASSEMBLY 40HP 14 15 5 15 4 3 2 13 1 Figure 8 8 AS805 040DS TE REV 00 ...
Страница 112: ...NOTES ...
Страница 113: ...NOTES ...