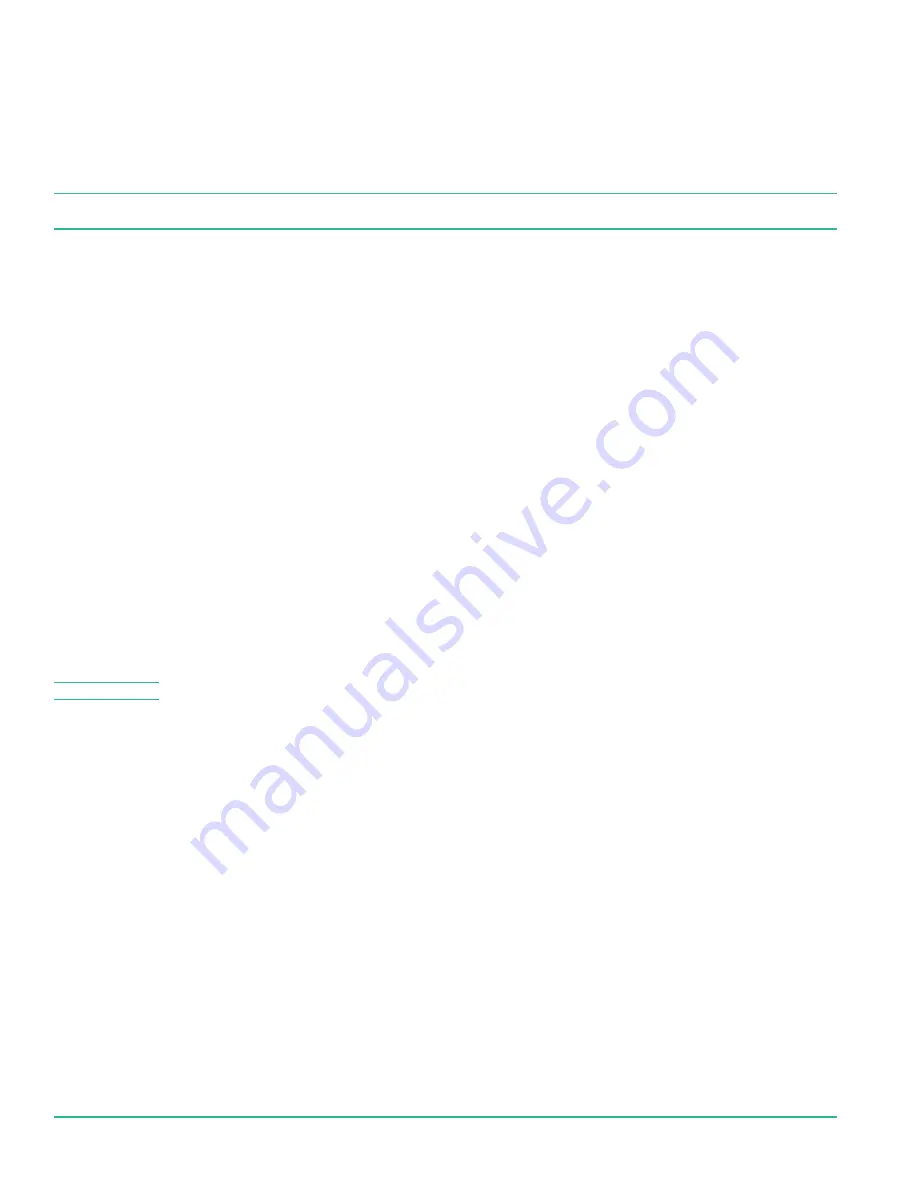
40
INSTALLATION
4.9
COMPRESSED AIR SYSTEM
Connect to plant air system with a flexible connector with a minimum rating of 200 psi (13.8 bar) and 245°F
(118°C). Piping should be large enough in diameter to minimize pressure drop. Support piping so that stress
is not transmitted to the compressor. Mount the pipe supports independent of the compressor to limit
vibration and prevent expansion strain. A loop system is recommended, with all piping sloped to accessible
drop legs and drain points. Install an appropriate flow-limiting valve for each additional 75 feet of hose in
runs exceeding ½-inch inside diameter to reduce pressure in case of hose failure. Flow-limiting valves are
listed by pipe size and CFM. Select appropriate valves accordingly.
WARNING!
Never use plastic, PVC, ABS pipe or rubber hose in a compressed air system.
Install a moisture separator as close to the compressor as possible on plane with the discharge of the cooler.
If a receiver tank is going to be utilized, a rule of thumb for sizing would be four gallons per horsepower. By
adding an air receiver tank in the system, the compressor will offer smoother operation through air demands.
It is also recommended that air enters the receiver tank at a lower port than that of the tank’s outlet port.
Additional equipment such as dryers and conditioning filters should be installed after the receiver tank, prior
to customer’s process.
It is always recommended to locate additional compressed air equipment as close to the compressor package
as possible. Keep in mind that pipe length and elbows, especially 90°, produce pressure drops which directly
impact the output performance to the customer’s process.
4.10
MULTIPLE MACHINE INSTALLATION
If the compressor is going to be installed in a sequence system with other compressors, special controls are
required to reduce the power cost. A multi-machine Base Load Transfer (BLT) component or a Sequencer
control unit will be necessary. For more information on a BLT/Sequencer, consult Factory.
4.11
STORAGE
If it is necessary to store the compressor for a long period of time, the following procedures are
recommended to avoid damaging the compressor:
»
Store the compressor package on a dry, solid surface.
»
Make sure all air and electrical connections are disconnected or locked out.
»
Top off all fluid levels and cover the compressor package with a waterproof tarpaulin that can be easily
removed for in-storage maintenance.
»
While in storage, rotate the compressor shaft every six months to make sure the bearings stay
lubricated.
CAUTION!
Before putting the compressor package back into service follow all INSTALLATION procedures.
Содержание 15D
Страница 6: ...vi About This Manual ...
Страница 12: ...4 Introduction ...
Страница 20: ...12 Specifications 2 2 DIMENSIONS OPEN BASE MOUNT AIR COOLED Figure 2 1 GA 15 40D AC BM OPEN ...
Страница 21: ...13 Specifications 2 3 DIMENSIONS ENCLOSED BASE MOUNT AIR COOLED Figure 2 2 GA 15 40D AC BM VERT ENCL ...
Страница 22: ...14 Specifications 2 4 DIMENSIONS OPEN BASE MOUNT WATER COOLED Figure 2 3 GA 15D 30D WC BM HORZ OPEN GAUGES ...
Страница 23: ...15 Specifications 2 5 DIMENSIONS ENCLOSED BASE MOUNT WATER COOLED Figure 2 4 GA 15 40D WC BM ENCL GAUGES ...
Страница 24: ...16 Specifications 2 6 DIMENSIONS OPEN PLATFORM MOUNT AIR COOLED Figure 2 5 GA 15 40D AC PLAT OPEN GAUGES ...
Страница 25: ...17 Specifications 2 7 DIMENSIONS ENCLOSED PLATFORM MOUNT AIR COOLED Figure 2 6 GA 15 40D AC PM VERT ENCL ...
Страница 30: ...22 Specifications 2 12 PIPING AND INSTRUMENTATION AIR COOLED Figure 2 11 GA P I S R02 ...
Страница 31: ...23 Specifications 2 13 PIPING AND INSTRUMENTATION WATER COOLED Figure 2 12 P I 15 40 WC GAUGES R00 ...
Страница 34: ...26 Specifications ...
Страница 66: ...58 Troubleshooting ...
Страница 84: ...76 Parts Catalog 8 10 AIR INLET ASSEMBLY 15 30HP 13 12 11 13 12 4 5 2 3 14 1 Figure 8 6 AS805 030D7H TE R00 ...
Страница 88: ...80 Parts Catalog 8 12 AIR INLET ASSEMBLY 40HP 14 15 5 15 4 3 2 13 1 Figure 8 8 AS805 040DS TE REV 00 ...
Страница 112: ...NOTES ...
Страница 113: ...NOTES ...