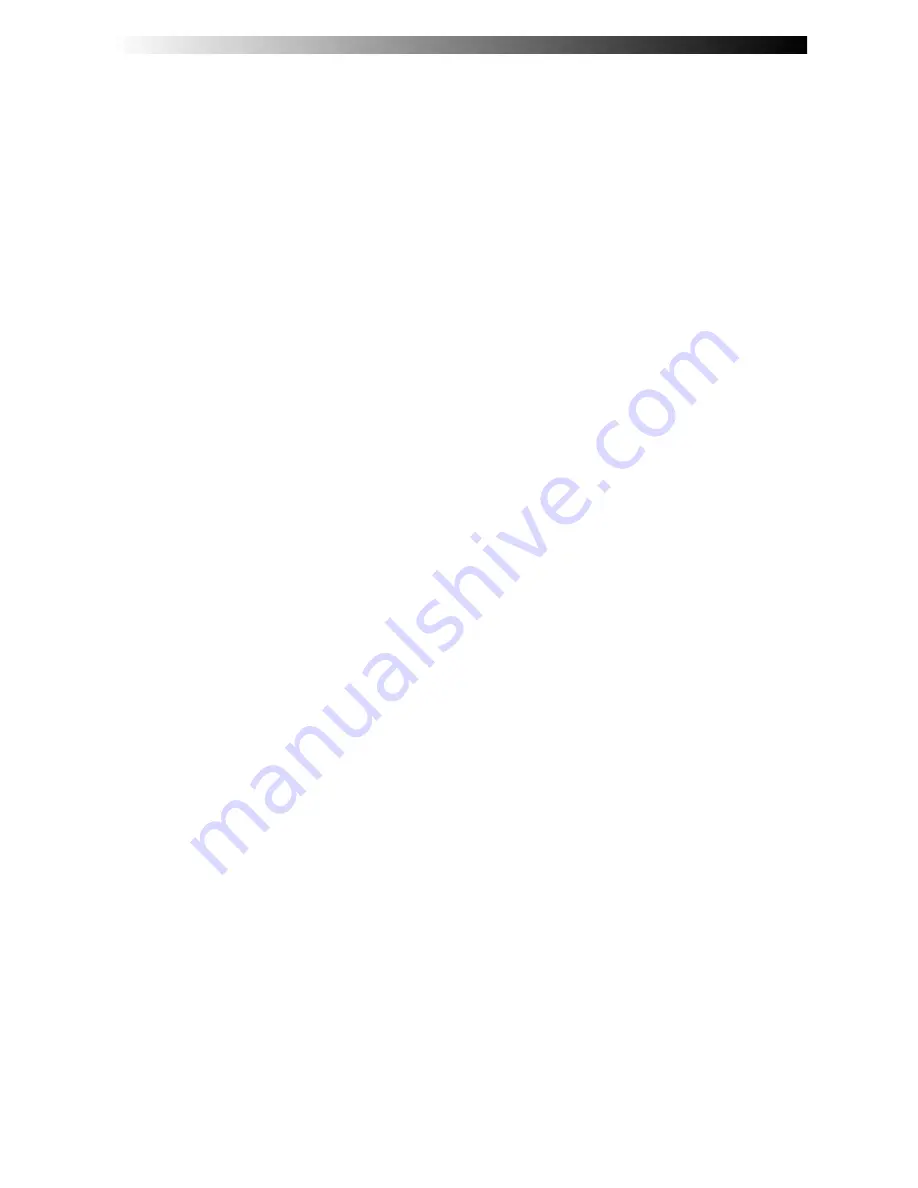
Doc653/30CV02A
11
- Ensure that there is suffi cient room around the device for maintenance and the replacement of
components if necessary
The recommended minimum clearance is as follows:
- 1000 mm to the front (free space for movement);
- 400 mm above;
- 250 mm below;
Since all the components can be accessed from the front, no minimum distance is required on
the left and right side. We however recommend a minimum distance of 100 mm in order to enable
easy opening of the casing.
5.2.3 Ventilation
The ventilation of the installation room should conform to the applicable national and local stand-
ards and regulations.
In connection with ventilation, keep in mind the following points:
a. Follow the applicable national and local standards and regulations concerning the dimensions
of the opening and the protection of the mechanical ventilation system if any
b. The air inlet openings should be in two walls facing each other
c. Use broad, low inlet grills
d. The ventilation outlet should be at high level as high as possible
e. In the case of insuffi cient air supply, it may be necessary to mechanically supply ventilation air.
5.3 Connections
5.3.1 Gas
connection
The gas connection should be installed by a recognised installer in accordance with applicable
national and local standards and specifi cations.
The gas connection is located on the bottom of the appliance.
The pressure on the inlet side of the appliance should be reduced to 20 mbar for natural gas and
up to 50 mbar for propane, using a gas governor.
The pressure loss in the supply pipe should be such that the pressure never falls below 17 mbar
for natural gas and 30mbar for propane, when the appliance is at maximum load.
In order to guarantee that the gas valve works at all times, it is recommended that a gas fi lter is
installed in the gas pipeline. The gas fi lter can be ordered as an option to be supplied with the
boiler.
Install a gas isolating valve directly under the appliance.
5.3.2 Electrical
connections
The electrical connections should be installed by a recognised installer in accordance with appli-
cable national and local standards and specifi cations.
The appliance is fully wired in accordance with the electrical diagrams delivered with the appli-
ance.
All the electrical connections are located behind the control panel. The control panel can be eas-
ily opened after removing the locking screw. The cables to be connected (supply, control) enter
through the bottom of the appliance via cable glands.
Содержание ECONOFLAME R30
Страница 35: ...Doc653 30CV02A 31...
Страница 36: ...32 Doc653 30CV02A...