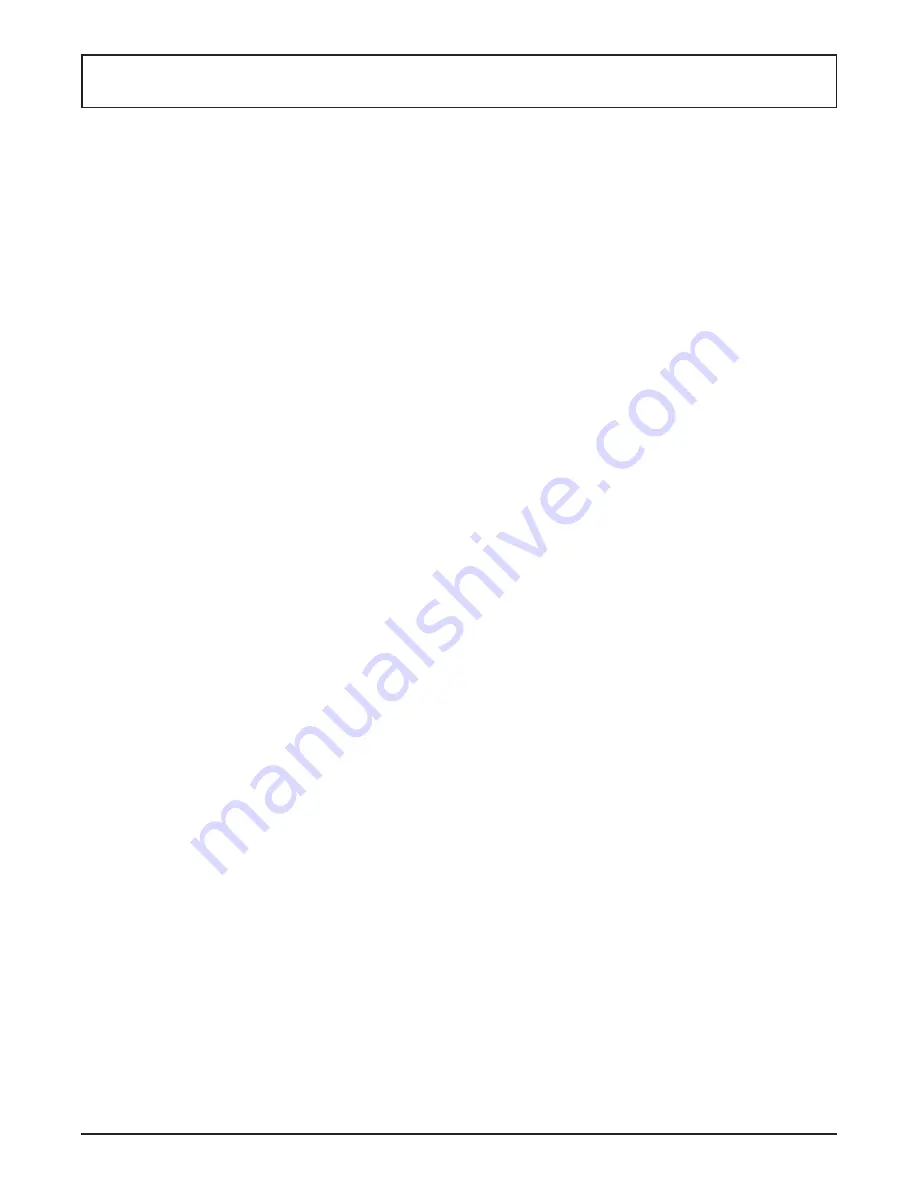
Owner’s Manual #513698 Rev.1
13
AUTOVEND Model Machines
SECTION 4
TROUBLESHOOTING
4.1
OUT OF ORDER
If the vending interface shows an out of order screen,
complete the following checks before contacting a service
technician.
CUP LEVELS
Make sure there is a minimum of three tubes full of cups.
Insert a maximum of 30 cups into each tube. When insert-
ing, pull them apart slightly so they are not stuck together.
Discard any damaged cups.
MIX LEVELS
Make sure the hoppers are at least 3/4 full of liquid mix.
Add mix if necessary.
CAROUSEL DOOR
Make sure there are no objects in the carousel door and
remove them if necessary.
CUP HOLDER ASSEMBLIES
Make sure the thumb screws on the cup holder assemblies
are tight. Tighten as necessary.
INTELLITEC2™ ERROR
Refer to Section 4.2 for troubleshooting error codes on
the IntelliTec2™ control.
4.2
INTELLITEC2™ ERROR CODES
When the machine experiences a problem, one of the
following error codes will be displayed on the control
panel. Each error code directs you to the system location
of the malfunction.
ERROR CODE MALFUNCTION
2
High
Torque
3
Run
Time
4
Clean
5
Freezing Cylinder Sensor
6
Hopper Sensor (single hopper machines)
7
Drive Motor
8
Cab Sensor
9
High Pressure Cutout
10
Auxiliary
Sensor
11
Prime (cab units only)
12
Left Hopper Sensor
13
Right Hopper Sensor
21
Spigot
Open
Time
To return the machine to normal operation, any error
causing condition must be corrected and the power to
the affected freezing cylinder must be cycled. Turn the
power to the freezing cylinder off then back on using the
On/Off button of the affected freezing cylinder.
4.3
INTELLITEC2™ ERROR CODE
TROUBLESHOOTING
Error Code 2 - High Torque
If the control panel displays a High Torque Error
(E2), the controller has sensed that the drive motor
is running at a high load for 10 or more seconds.
This may be due to the product consistency
adjustment being set too high. Press the On/Off
button for the cylinder to turn it off, wait until the
product in the freezing cylinder thaws and then
turn the cylinder back on. If the error persists,
contact your Authorized Stoelting Distributor for
further assistance.
Error Code 3 - Run Time
The Run Time Error (E3) occurs when the
compressor runs continuously for an extended
period. This error is generally caused by very
low mix levels in the hopper or from product
breakdown. Another common cause results from
a restriction preventing mix from entering the
freezing cylinder. Check the mix in the hopper.
If the level mix is low, add mix. If there is a
possibility that the mix has broken down, clean
and sanitize the machine and replace the mix
with fresh product.
Ice crystals in the hopper can clog the mix inlet
system and prevent mix from entering the freezing
cylinder. Thoroughly thaw mix per manufacturer’s
recommendations. To check for ice crystals, pour
a small amount of product from the mix container
through a clean and sanitized sieve or strainer.
If ice crystals are in the mix, check temperature
of the walk-in cooler where the mix is stored.
In air cooled machines, the Run Time Error
may indicate that airfl ow within the machine
has reduced or stopped. Check the sides of the
machine for anything that would restrict airfl ow.
If the error persists after attempting to clear it,
contact your Authorized Stoelting Distributor for
further assistance.
Error Code 4 - Clean
If the machine is left in the Clean Mode for more
than 20 minutes, the control panel will display a
Clean Error (E4). This condition does not refl ect a
problem with the machine itself. The Clean Error
has been programmed into the controller as a
safeguard to protect the machine from potential
damage caused by the machine being accidentally
left in "Clean Mode". To clear the Clean Error,
press the On/Off button for the cylinder to turn if
off then back on.
Содержание AUTOVEND
Страница 1: ...Model AUTOVEND OPERATORS MANUAL Manual No 513698 Rev 1...
Страница 2: ......
Страница 6: ......
Страница 22: ...Owner s Manual 513698 Rev 1 16 AUTOVEND Model Machines...