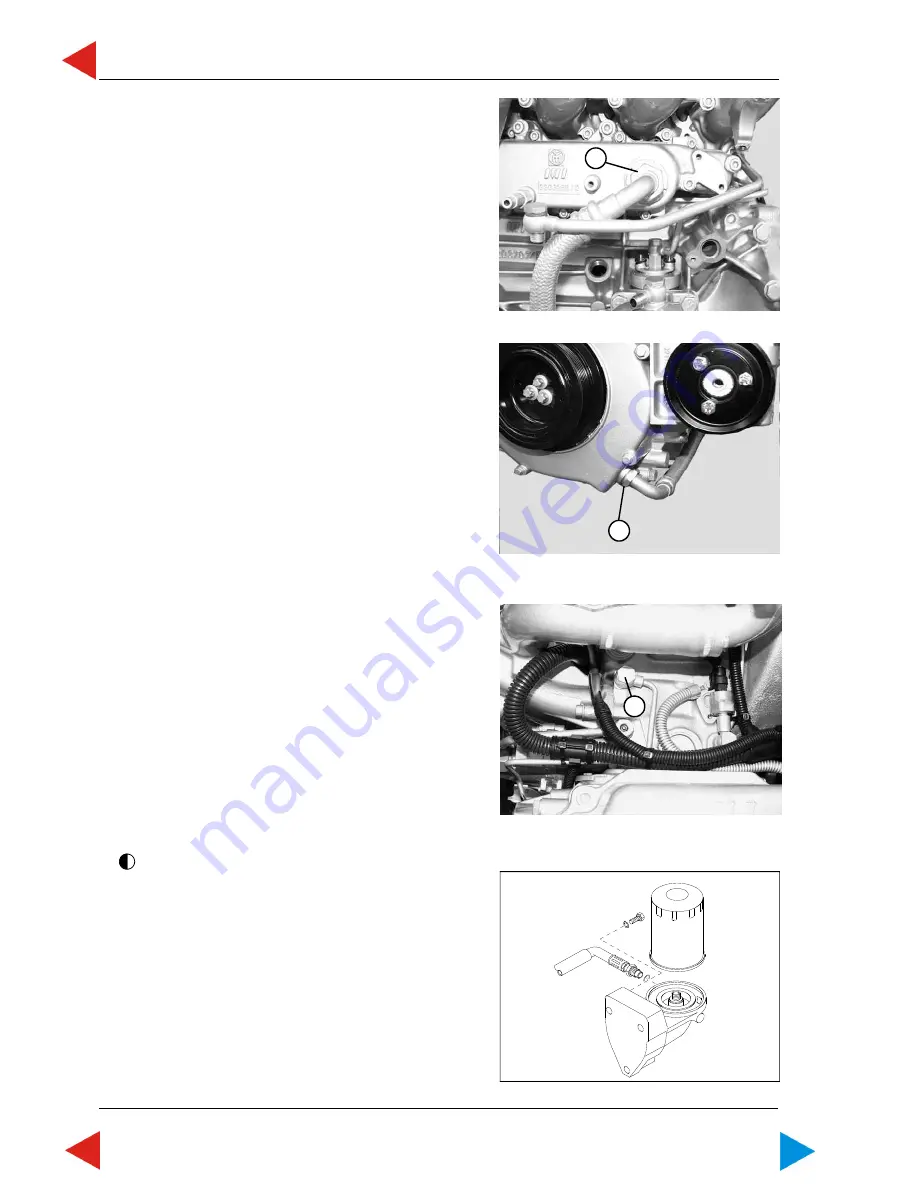
01 ENGINE
Page ENGINE - 64
Z001019/0_6_July 2008
SERVICE MANUAL MARINE ENGINES
5
Dismantle oil hose on engine cooler (ill.5/pos.1).
6
Disconnect oil hose on oil pump (ill.6/pos.1).
7
Unscrew hollow screw (SW19) (ill.7/pos.1) to fuel
feed pipe.
For 4 cyl. engines
8
Remove oil filter bracket.
06.01 ill.5
06.01 ill.6
06.01 ill.7
06.01 ill.8
1
1
1
ToC
Содержание M0114K33
Страница 2: ...THIS PAGE IS INTENTIONALLY BLANK ...
Страница 140: ...01 ENGINE PageENGINE 80 Z001019 0_6_July 2008 SERVICE MANUAL MARINE ENGINES THIS PAGE IS INTENTIONALLY BLANK ToC ...
Страница 148: ...01 ENGINE PageENGINE 88 Z001019 0_6_July 2008 SERVICE MANUAL MARINE ENGINES THIS PAGE IS INTENTIONALLY BLANK ToC ...