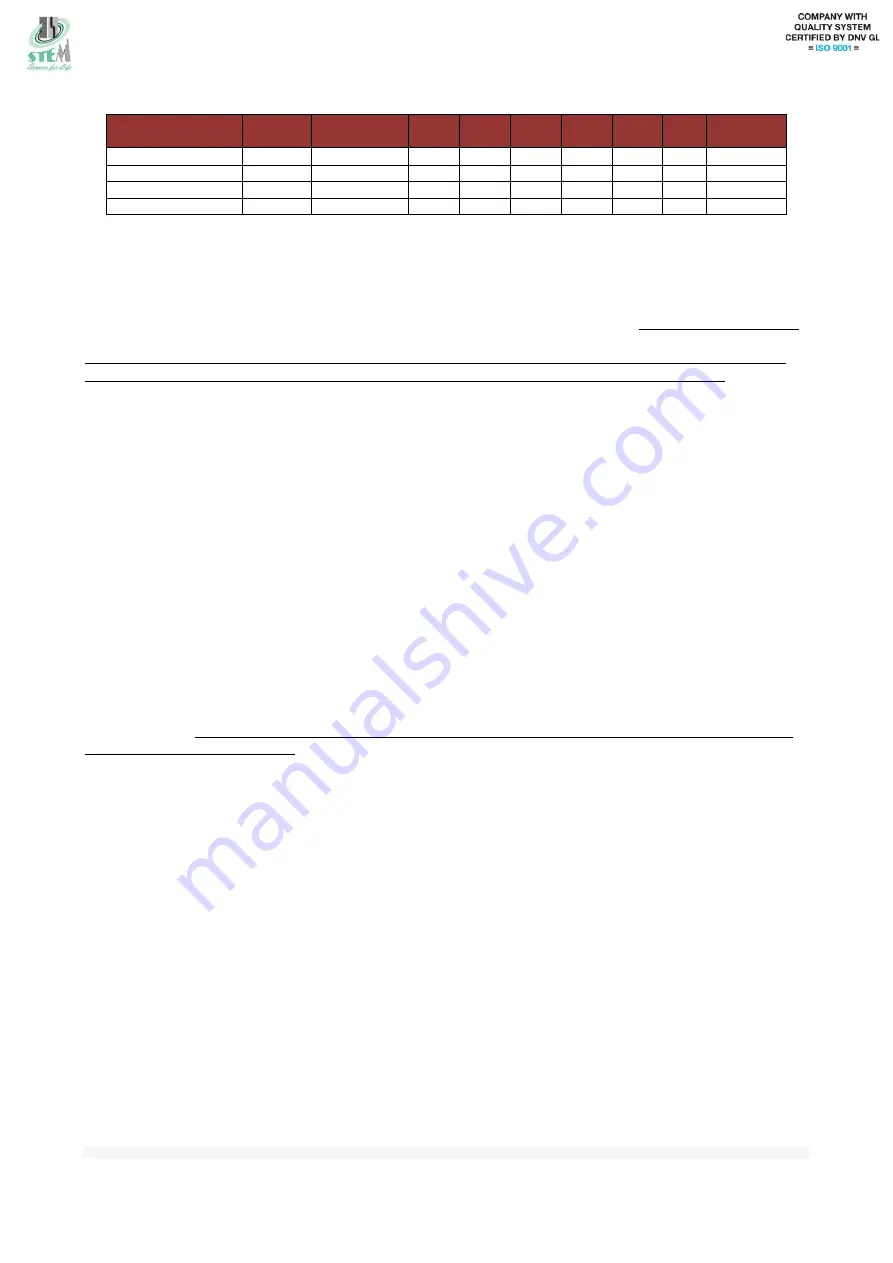
MANUAL NCBM 01 Revision 14 11/06/2021
STEM S.r.l. via della Meccanica, 2 I-27010 Cura Carpignano- Pavia Italia Tel. +39 0382 583011 Fax +39 0382 583058 www.stemsrl.it [email protected]
Subject to change without notice, no responsibility will be taken for every detail. © STEM S.r.l.
5 Generic alarm valid for all configurations
ALARM
Severity
Restore
LED1
LED2
LED3
LED4
LED5
ALL
Relay fault
Battery
No Block
Automatic
OFF
OFF
OFF
OFF
ON
ON
OFF
RTCC Alarme
No Block
Automatic
OFF
OFF
ON
OFF
OFF
ON
OFF
Alarme memory write
No Block
Automatic
OFF
OFF
OFF
ON
OFF
ON
OFF
Allrm time out HW
Block
RESET Button
OFF
OFF
ON
OFF
OFF
ON
ON
TAB. 6 Generic alarm valid for all configurations
6 HW redundancy circuitry
The NCBM is equipped with a redundancy HW circuit that in case the test is not performed within a 38-hour generates
an alarm. The reset is possible only by pressing the reset button.
Each time the monitoring test is performed, the internal counter is reset by the change of status of the outputs O1-O2
and subsequent activation of the V1-V2 (to be connected in any application hydraulic, electrical and OSG)
7 Internal clock management
The device has an internal clock that thanks to the battery, continues to operate even in the absence of main power
supply. Clock adjustment can be accomplished using the SW interface or by using the buttons on the NCBM unit.
Pressing the TIME button for 5 seconds, the current time is displayed by blinks of the led3: every flash corresponds to
one hour.
Pressing the time and reset button for about 3 seconds allows to enter in configuration mode: the LED1 will light and
every time you press the button “
time”
you will add 1 hour (example: if I need to set the 10 o clock, we must press
“TIME”
10 times ). LED4 will flash each time you press the button.
8 Battery and operation in case of power failure
In case of power failure the NCBM01 keeps in operation only internal clock. After the return of the supply voltage, the
control unit restores its normal operation within 1 minute.
The customer can select to use external 12V battery connected to the inputs A3-A4 or to use an internal battery inserted
on the front side. The internal battery should be type CR2032 220mAh the “+” polarity toward the upper part of the
device (tampo-print side). To avoid unexpected behavior when replacing the battery, it is suggested to insert it when the
control unit is on. The battery is used only to keep the clock updated, in case of traction lift configuration or hydraulic
without monitor it can be not used
9 START UP AND E PERIODIC INSPECTION
9.1 HYDRAULIC LIFT WITH MONITORING
1.
Set through the user interface SW related parameters
2.
Do some test runs up and down checking through the LEDs 1 to Led5 (Option 1 and Option 2) that the
received signals from the system are correct and the LED FAULT is not activated.
3.
Simulate the operation of re-leveling and checks by means of the LEDs1 to Led5 (Option 1 and Option 2) that
the received signals from the system are correct and the LED FAULT is not activated.
4.
PERIODIC TEST SIMULATION SUCCESSFULLY PERFORMED
:
With the system stopped at the
bottom floor and with closed doors, turn on the test input (T1 to GND, T2 to 24VAC/DC) by means of an
external pushbuttons. The test monitoring will start opening one valve at a time. If the LED fault remain off,
the test is considered passed
5.
PERIODIC TEST SIMULATION WITH NEGATIVE RESULT AT VALVE V1
:
With the system
stopped at the bottom floor and with closed doors, turn on the test input (T1 to GND, T2 to 24VAC/DC) by
means of an external pushbuttons. During the valve V1 test (V2 open) simulate a re-leveling, once the car
position is OK wait for the restart of the test (Led3/led5 flashing) and simulate again a re-leveling. The test is
considered passed if the control unit will activate the alarm LED and the fault relay will change state.