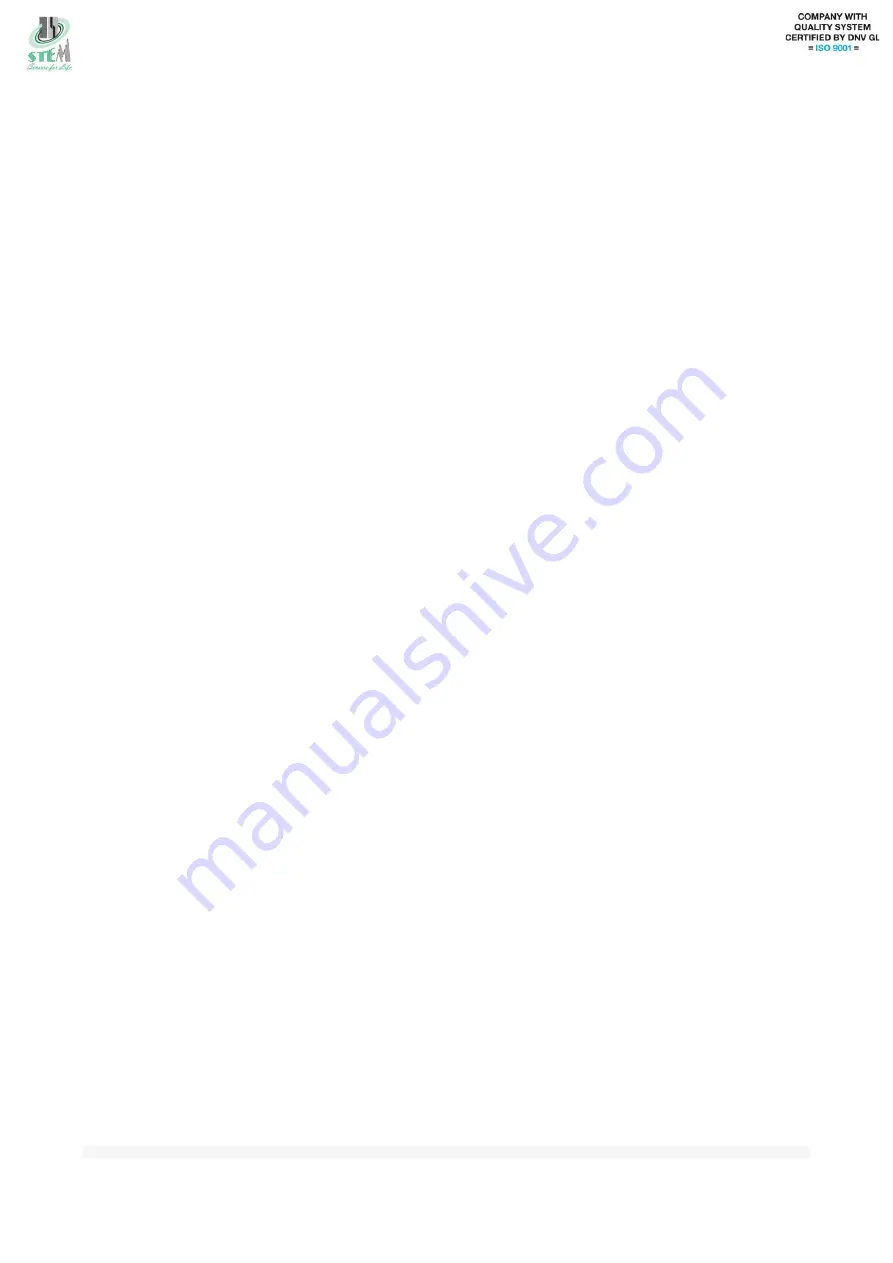
MANUAL NCBM 01 Revision 14 11/06/2021
STEM S.r.l. via della Meccanica, 2 I-27010 Cura Carpignano- Pavia Italia Tel. +39 0382 583011 Fax +39 0382 583058 www.stemsrl.it [email protected]
Subject to change without notice, no responsibility will be taken for every detail. © STEM S.r.l.
6.
PERIODIC TEST SIMULATION WITH NEGATIVE RESULT AT THE POWER ON:
after the alarm generated at the step 5) remove and reconnect the power supply make sure that the alarm
remains active, then press the reset button for approximately 5 seconds to reset the faulty condition.
7.
PERIODIC TEST SIMULATION WITH NEGATIVE RESULT AT VALVE V2
:
with the system
stopped at the bottom floor and with closed doors, turn on the test input (T1 to GND, T2 to 24VAC/DC) by
means of an external pushbuttons. During the valve V2 test (V1 open) simulate a re-leveling. Once the car
position is OK, wait for the restart of the test (Led3/led5 flashing) and simulate again a re-leveling. The test is
considered passed if the control unit will activate the alarm LED and the fault relay will change state.
8.
Do again the point 6
9.
Checks the time and eventually set it to the correct value.
9.2 HYDRAULIC LIFT WITH BUCHER I-VALVE
1.
Set through the user interface SW related parameters
2.
Do some test runs up and down checking through the LEDs that received signals from the system are correct
and the LED ALL and the relay FAULT are not activated.
3.
I-VALVE ERROR 1 DETECTED:
disconnect the SMA signal, travel command high (run elevator) than
travel command low (stop the elevator), checks activation of the relay alarm and the correct led status
4.
I-VALVE ERROR 2 DETECTED:
connect the
P01 to 24V, travel command high (run elevator), checks
activation of the relay alarm and the correct led status
9.3 TRACTION LIFT USING BRAKES
1.
Set through the user interface SW related parameters
2.
Do some test runs up and down checking through the LEDs 1 to Led5 (Option 1 and Option 2) that the
received signals from the system are correct and the LED FAULT is not activated.
3.
TEST SIMULATION WITH NEGATIVE RESULT:
simulate a non opening and a non-closing of the
microswitch per each of them which is used.
4.
TEST SIMULATION WITH NEGATIVE RESULT AT THE POWER ON:
after the alarm generated at the step 3) switch on and off the power supply make sure that the alarm remains
active, then press the reset button for approximately 5 seconds to reset the faulty condition.
5.
Checks the time and eventually set it to the correct value.
9.4 TRACTION LIFT USING OSG
1.
Set through the user interface SW related parameters
2.
Do some test runs up and down checking through the LEDs 1 to Led5 (Option 1 and Option 2) that the
received signals from the system are correct and the LED FAULT is not activated.
Type 1
OSG with electromagnet released each time the elevator stops at floor:
Perform the test 8.2 from points 3 to 5
Type 2
OSG with electromagnet released only in case of undeteced movement
Option 1:
1.
TEST SIMULATION SUCCESSFULLY PERFORMED:
With the system stopped at the bottom
floor and with closed doors, turn on the test input (T1 to GND, T2 to 24VAC/DC) by means of an
external pushbuttons. After the pending time (30s), the test sequence will start, with the opening and
subsequent closing output O1 in series with the electromagnet. If there is proper switching sequence
on the OSG contact: opens when O1 opens, closes when O1 closes, the test ends successfully
2.
TEST SIMULATION WITH NEGATIVE RESULT (contact failure to open):
a.
Jumper output O1 so that the electromagnet remains always powered
b.
With the system stopped at the bottom floor and with closed doors, turn on the test input (T1
to GND, T2 to 24VAC/DC) by means of an external pushbuttons. After the pending time
(30s), the test sequence will start
opening the output O1, but the microswitch will not change
state because the electromagnet remain energized. The monitoring alarm will be activated