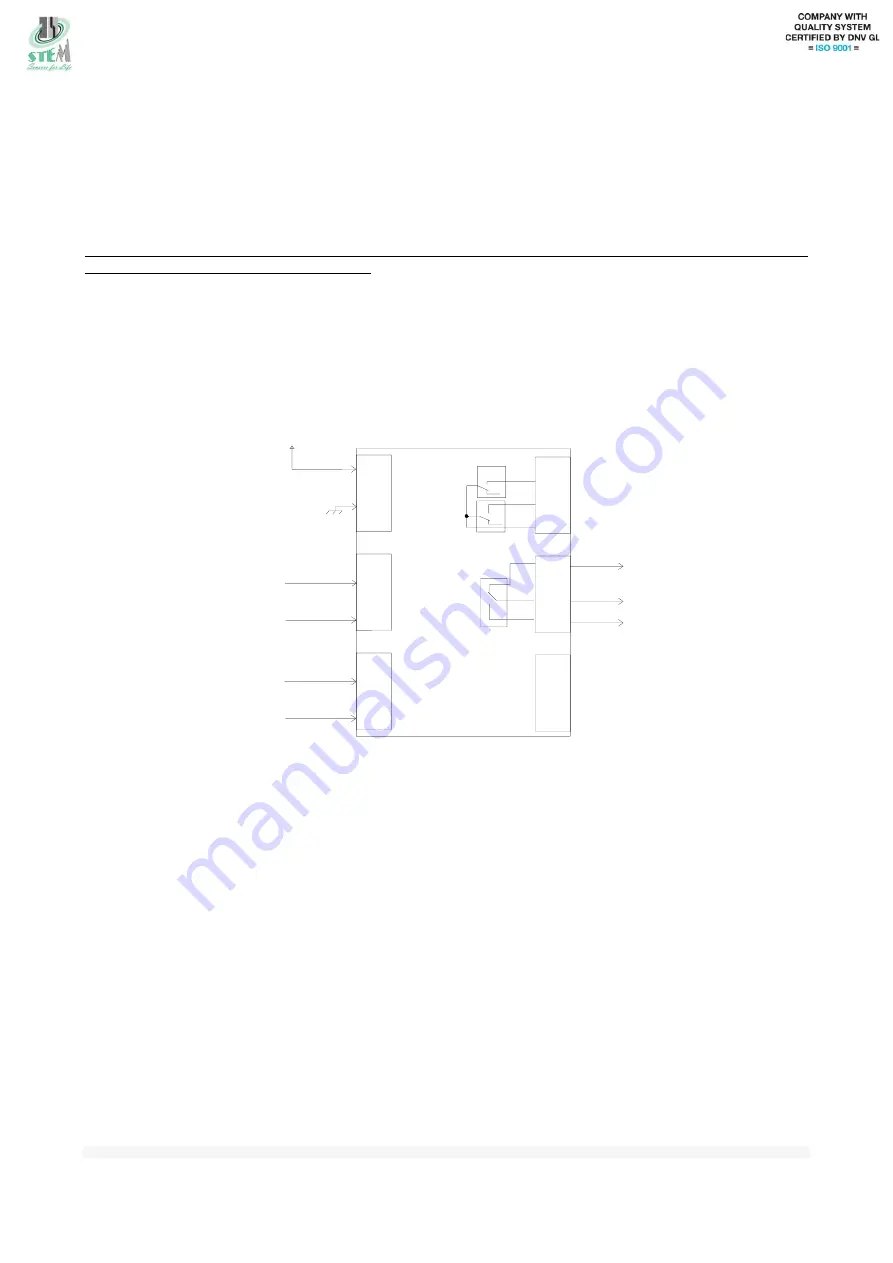
MANUAL NCBM 01 Revision 14 11/06/2021
STEM S.r.l. via della Meccanica, 2 I-27010 Cura Carpignano- Pavia Italia Tel. +39 0382 583011 Fax +39 0382 583058 www.stemsrl.it [email protected]
Subject to change without notice, no responsibility will be taken for every detail. © STEM S.r.l.
If the above conditions are met the test will start by opening the output O1 (valve V1 closed in testing) and maintaining
the output O2 closed so that the valve V2 will remain open. The duration of the test valve is set via the parameter “
test
duration”
in the configuration user interface, after the test of the first valve, after 5 seconds it will proceed to the tests
of the second valve in a similar manner (activate O1, O2 deactivated). In case a leveling command is activated (up
command active without speed signal within 5 second), the test is repeated. If during the second attempt a leveling
command is activated again the test failed. The alarm is signaled by the fault relay and the lighting of the LED
indicators. After a switch on/off of the NCBM01 the alarm remain activated until the reset button is pusher for at least
5 seconds. If, during the test one of the following commands:
door open
or
down
or
up
followed by the
speed
within
5s, the test is suspended.
If a frequency daily tests is set, the device has a time-out for the execution of the test of one hour. If the test is not
performed within 1 hour an alarm is generated. If it is set the tests frequency of one hour, there is no time-out
The parameters for the handling of activation delay of the valves, during normal elevator operation, are configured
using the masks "Valve sequence", "down valve closing delay", "down valve opening delay", as described in the
previous paragraph.
Thirty seconds before the execution of the test and for the whole duration of the same, the output TW (test warning)
will remain active to signal the imminent execution of the test. This function is useful to signal to the control cabinet the
test coming and to perform the commands necessary for the preparation of the test : door closing, lowest floor...
2.4 Bucher I-VALVE signal control
FIG. 2 Electrical scheme connection for hydraulic lift
The configuration Bucher I-VALVE allows to control the timing of the SMA signal when the travel signal is changing
the state. As indicated in the valve manual, the system detects the
error1
and
error2
:
Error 1 : when travel command goes from high level to low level, the SMA signal should change the state from 0.1s to
1s after the travel signal change, if the timing is not respected error1 has to be detected
Error 2 : when travel command goes from low to high level, the SMA signal should change the state within 0.1s after
the travel signal change, if the timing is not respected error2 has to be detected
If the error is detected the Fault relay will change state according to the relay polarity selected in the SW configuration
•
FNO, in case of alarm FNO, CF is closed
•
FNC, in case of alarm FNC,CF is closed
Led 3, Led4 and led5 continues to signal the state of the SMA and TRAVEL commands even if NCBM is in alarm
The alarm will be maintained until a manual reset will be performed.
JP1
T2
D2
D1
JP3
V1
PO2
JP2
T1
A2
A1
PO1
V2
J1
FNC
J2
CF
S1
S2
J3
FNO
K2
Fault Relay
K1
PT2
PT1
A3
A4
NCBM 01
+24VDC / L1(AC)
TRAVEL
COMAND
SMA
SIGNAL
CO
TW
O1
O2