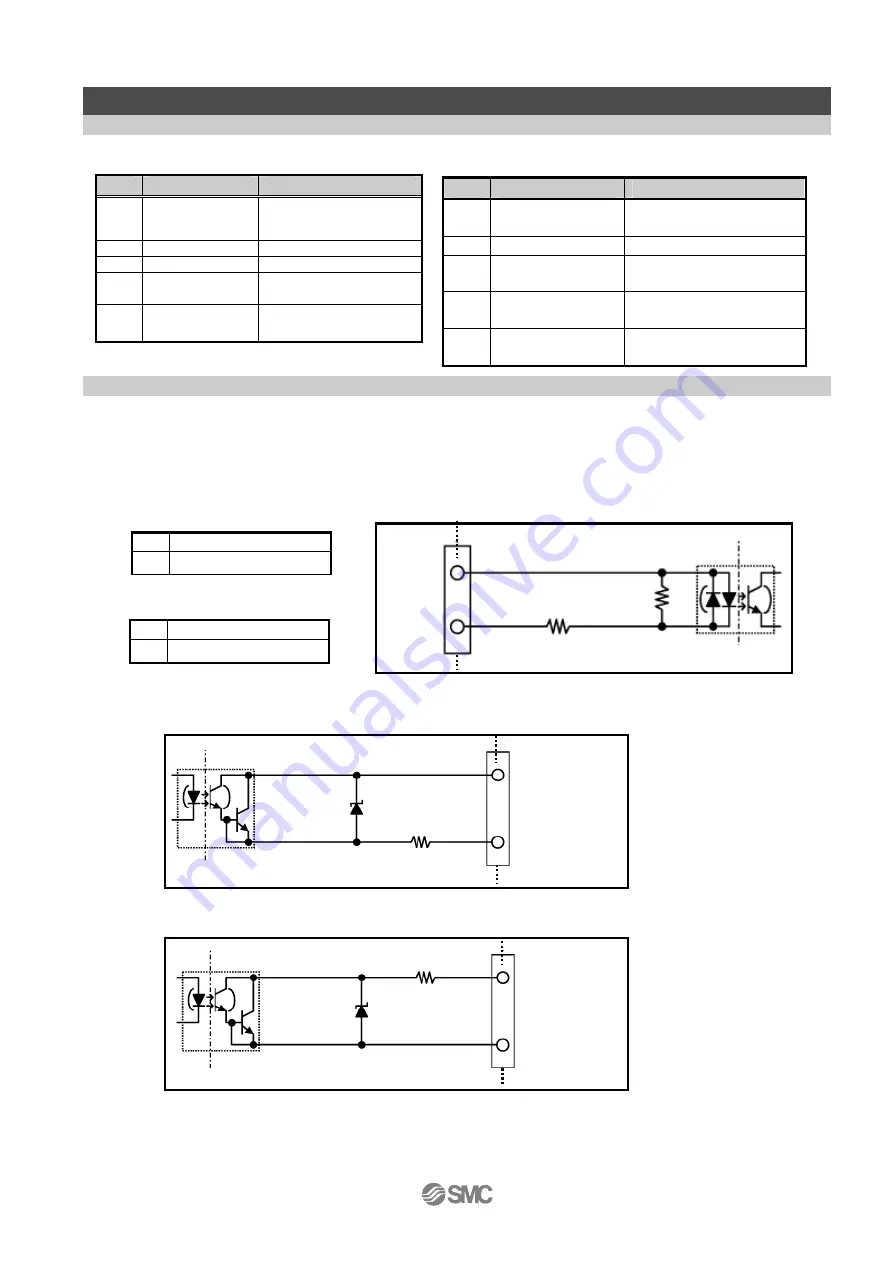
- 19 -
6. CN4: Parallel I/O cable
6.1 Paralles input / output
■Input specifications
■
Output specifications
6.2 Parallel input / output circuit (NPN, PNP)
There are two types of parallel input / output types for this controller.
NPN type
(
LECP1N
□□
-
□
)
PNP type
(
LECP1P
□□
-
□
)
(1) Parallel I/O input circuit (NPN, PNP common)
(2) Parallel I/O output circuit
NO.
Item
Specifications
1
Output circuit
Internal circuit and the
photo coupler insulation
2
No. of output
6 opints
3
Maximum voltage
between terminals
DC30V
4
Maximum output
current
10mA
5
Saturation voltage
between terminals
2.0V (Maximum)
NO.
Item
Specifications
1 Input
circuit
Internal circuit and the
photo coupler insulation
2
No. of inputs
6 points
3 Voltage
DC24V±10%
4
Input current
at ON
3.5mA±20%(at DC24V)
5
Input current /
voltage at OFF
1.5mA or less of current
11V or less of voltage
(a)
(b)
Inside of the controller
(a)
「
COM+
」〈
1
〉
(b) IN0
〈
9
〉~
STOP
〈
14
〉
PNP TYPE
(a)
「
COM-
」〈
2
〉
(b) IN0
〈
9
〉~
STOP
〈
14
〉
NPN TYPE
PNP TYPE
Outside
OUT0
〈
3
〉
~
ALARM
〈
8
〉
OUT0
〈
3
〉
~
ALARM
〈
8
〉
「
COM-
」
〈
2
〉
「
COM+
」
〈
1
〉
Inside of the controller
Outside
Inside of the controller
Outside
NPN TYPE