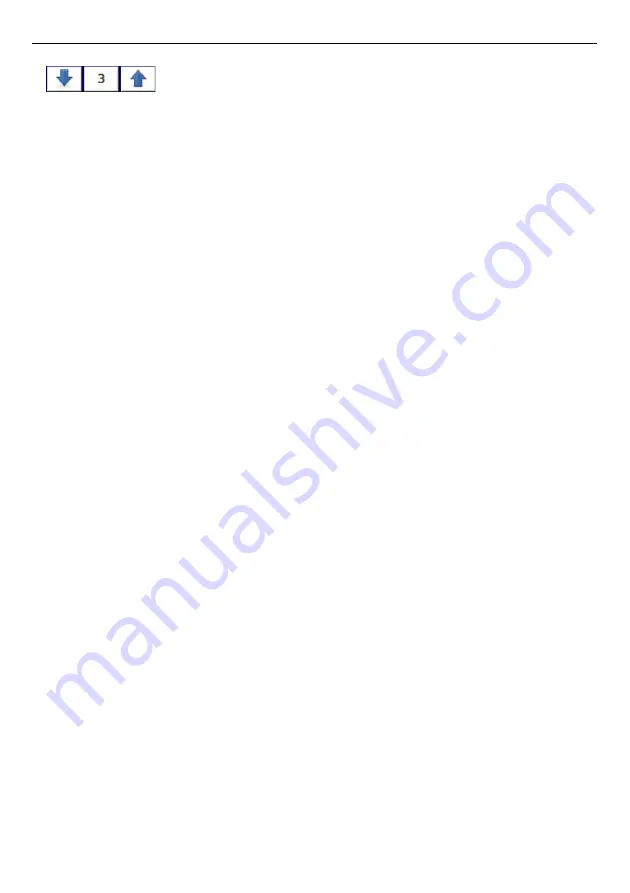
User Manual For - CONTROLLER/DATA RECORDER MultiCon CMC-N16
The arrows placed in the upper right corner of the screen allow
switching between controllers to configure settings of controller
parameters. The middle button allows a direct selection of a specific
controller from the list.
The parameters of
Controllers
are:
–
Controller name
– it gives the name to the Controller,
–
Autotuning parameters
parameter block - this block contains the following
parameters:
•
Start autotuning –
the button calling the autotuning procedure,
•
Mode
– the button for enabling / disabling the autotuning mode,
•
Set point mode
– this parameter sets a source for set point value, only for
autotuning process, takes options:
◦
value
– defines constant value as a source for set point value,
◦
from log. Channel –
defines logical channel as a source for set point value,
•
Set point value
– sets set point value, only for autotuning process,
•
Set point source
– defines logical channel that will be a source for set point,
only for autotuning process,
•
Feedback source
– defines logical channel that will be a source of feedback,
only for autotuning process,
•
Start mode
– parameter takes three options:
◦
manual
– starts with the button,
◦
from log. channel
– starts if set specified logical channel,
◦
start-up
– starts if device is during start-up,
•
Start source
– occurs when
Start mode: from log. channel,
defines logical
channel that will be a source of start autotuning,
•
Start triggering
– occurs when
Start mode: from log. channel,
defines the
start edge of autotuning, the first edge activates and the second deactivates
autotuning, takes options:
◦
rising edge
– reacts to rising edge,
◦
falling edge
– reacts to falling edge,
•
Timeout
– determines the maximum duration of autotuning in hours (max 24h),
–
Controller
parameters
parameter block - this block has the following parameters:
•
Mode
– defines one of the three available modes:
PD
,
PI
or
PID
,
•
P coefficient
– this parameter is always visible, allows to set the value of the
proportional coefficient,
•
I coefficient
– this parameter is available for the
Mode
:
PI
and
PID
and allows
to set the integral coefficient,
•
D coefficient
- this parameter is available for the
Mode
PD
and
PID
and allows
to set the derivative coefficient,
•
Differentiated signal
- this parameter is available for the
PD
and
PID
mode and
allows the selection of the option (see
◦
feedback (measured)
- this option should be used when the value of the
Feedback source
which is the source of data coming from the controlled
object is directly transmitted (no error recalculation at the controller input
and no dead zone control) on the derivative signal, which enables a faster
response of the device to fast changes of the controlled object,
◦
error (deviation)
- this option should be used, when the value of the
Feedback source
, which is a source of data coming from the controlled
object, is sent to the derivative signal after an earlier calculation of the error
188