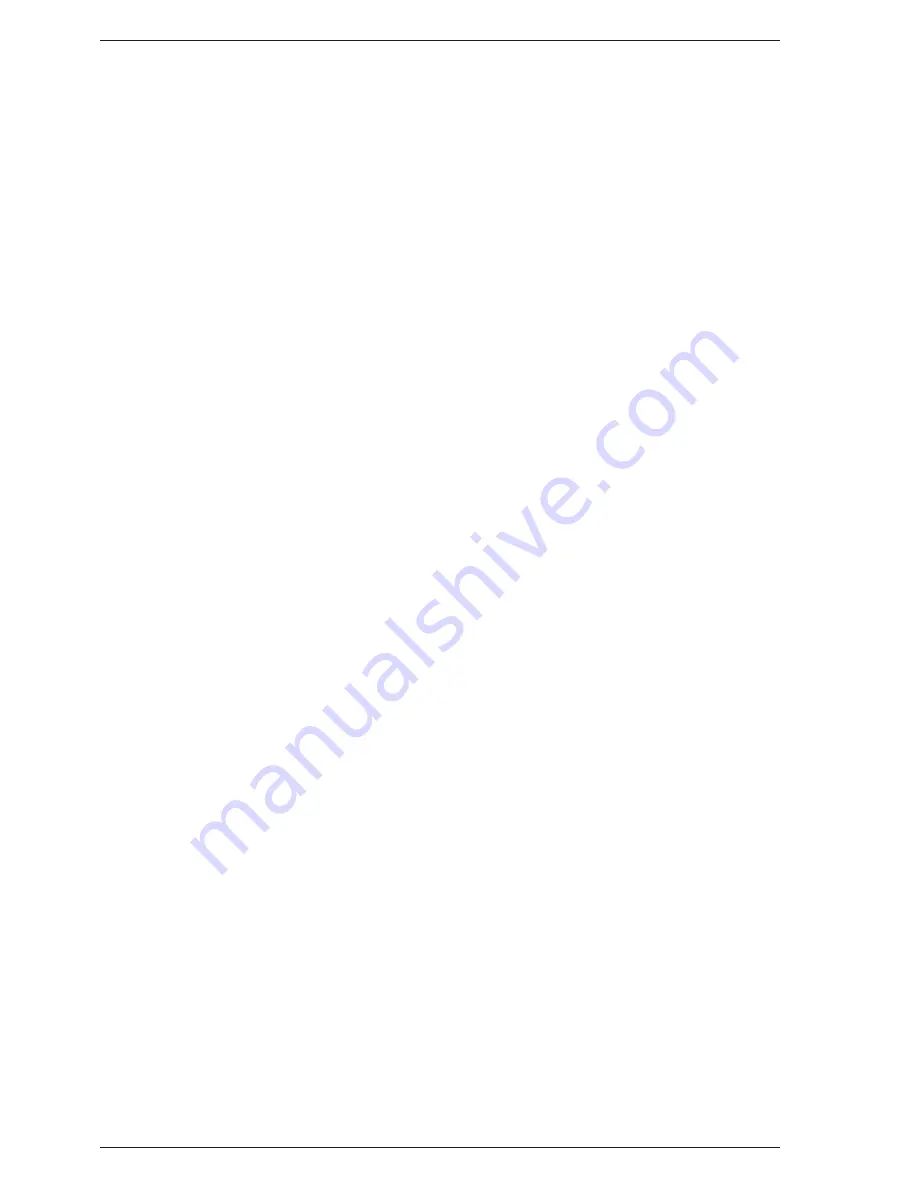
29
– Unscrew the two screws and nuts securing the viewing
window.
– Replace the viewing window and gaskets, and reassem-
ble in reverse order.
8.23
D.H.W. EXPANSION VESSEL - IF FITTED
– Remove the outer casing as described in section 5.1.
– Isolate the D.H.W. isolation valve (21 fig. 2).
– Drain the D.H.W. circuit by opening any D.H.W. tap
below the level of the boiler.
– Unscrew the D.H.W. expansion vessel and replace with
the new one, using a jointing compound suitable for
potable water.
– Reassemble in reverse order.
8.24
TIME CLOCK
– Remove the outer casing as described in section 5.1.
– Remove the two screws TCB M4 x 10 (2 fig. 14) and
pivot the control box downwards, then remove the two
self tapping screws (1 fig. 14) and remove the control
box cover.
– Pull off the electrical connections at the back of the
clock.
– Remove the four screws securing the plastic frame of
the time clock to the facia panel.
– Remove the plastic frame and pull out the time clock.
– Re-assemble in reverse order and test the operation of
the new clock.
Set it to the desired settings.
8.25
TIME CLOCK OVERRIDE SWITCH
– Follow the procedure described for the Summer/Winter
switch. (section 8.18).
8.26
FROST THERMOSTAT
The frost thermostat is located on a mounting plate on the
flow pipe, on the right hand side of the boiler (11 fig. 24).
– Remove the outer casing as described in section 5.1.
– Without disconnecting the wires, unscrew the two ther-
mostat fixing screws.
– Lift the thermostat and fixing screws out using the wires.
– Replace the thermostat and reconnect the wires (polarity
is immaterial).
Position the screws in the flange and re-fit using the wires
to position the thermostat before tightening the screws.
– Re-assemble in reverse order.
8.27
TEMPERATURE GAUGE
– Remove the outer casing as described in section 5.1.
– Remove the two screws TCB M4 x 10 (2 fig. 14) and
pivot the control box downwards.
– Remove the lower “key ring” securing the thermometer
phial in its pocket on the side of the air separator (next
to the overheat thermostat phial).
Remove the phial by sliding it downwards.
– Squeeze the gauge to depress the retaining clips, then
ease the gauge forwards.
– Re-assemble in reverse order.
Содержание SUPER 102
Страница 1: ...Super Combination Boilers installation and servicing instructions...
Страница 2: ......
Страница 25: ...21 7 INTERNAL WIRING DIAGRAMS AND VIEWS 7 1 FUNCTIONAL FLOW WIRING DIAGRAM Fig 23 a...
Страница 26: ...22 7 2 ILLUSTRATED WIRING DIAGRAM Fig 23 b...
Страница 35: ......