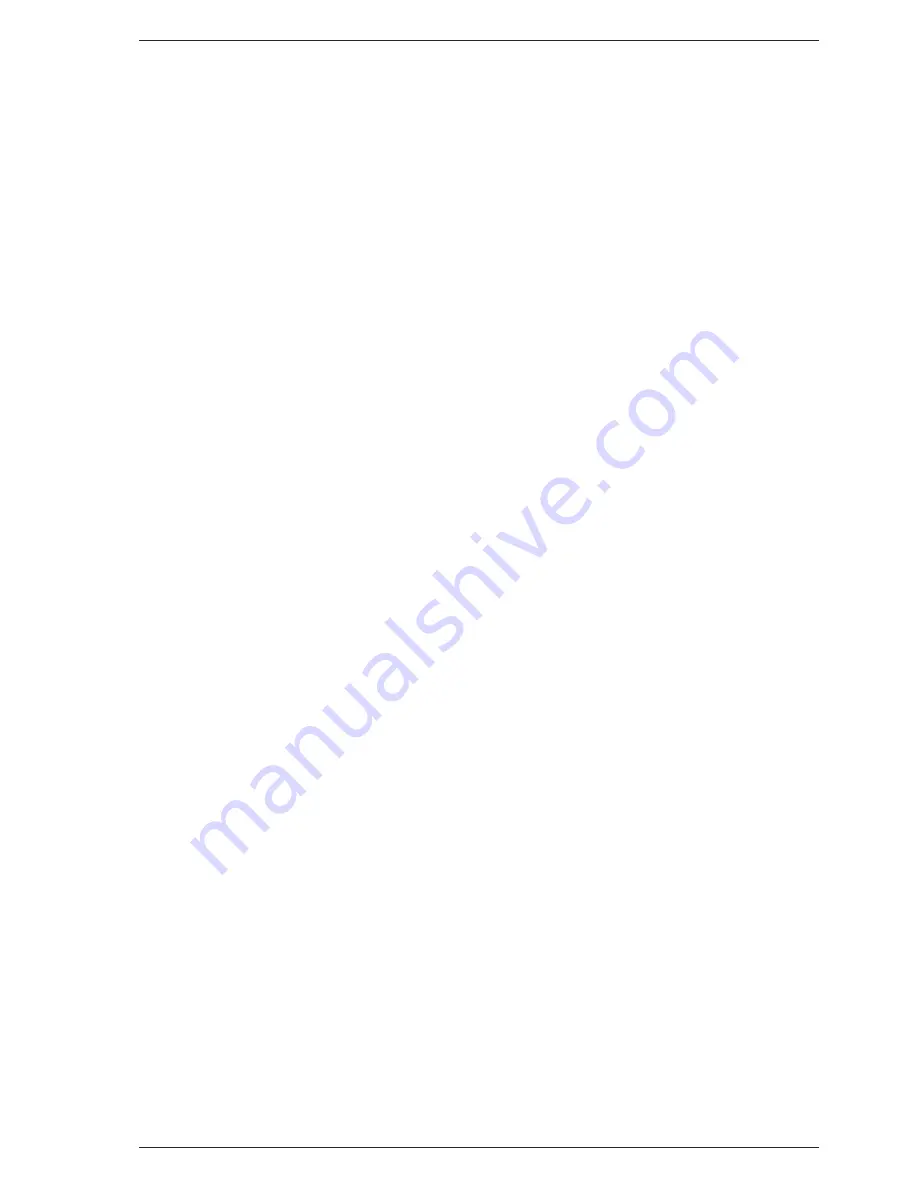
isolation valve (23 - 21 fig. 2).
– Drain the appliance through the drain plug situated
below the pump outlet and the drain point at the bot-
tom of the D.H.W. heat exchanger.
Rotate the pump to the R.H.S. to improve access to the
divertor valve.
– Drain the D.H.W. circuit by opening any D.H.W. tap
below the level of the boiler.
– Remove the two screws TCB M4 x 10 (2 fig. 14) and
pivot the control box downwards.
– Disconnect all union connections from the divertor
valve.
Withdraw the valve and remove the electrical connec-
tions.
– Transfer the electrical connections onto the new valve.
Refer to the wiring diagrams in section 7.
– Re-assemble in reverse order, using the new gaskets
supplied with the valve.
Refill and re-commission the system as described in sec-
tion 4.1.
8.16
DIVERTOR VALVE - MICROSWITCH
ASSEMBLY
– Remove the outer casing as described in section 5.1.
– Rotate the pump to improve access to the divertor valve.
– Pull out the microswitch circlip, and lift off the micro-
switch assembly.
– Transfer the electrical connections onto the new micro-
switch assembly. Refer to the wiring diagrams in sec-
tion 7.
– Re-assemble in reverse order.
8.17
C.H. EXPANSION VESSEL
In the unlikely event of failure of the expansion vessel
diaphragm it is acceptable to leave the vessel in position
and to fit a replacement vessel (of similar or greater capa-
city) external to the appliance but as close as possible to the
C.H. return.
Alternatively the vessel can be replaced as follows.
Note replacement is not recommended if a rear flue outlet
is used or if the clearance above the casing is less than
300 mm.
– Remove the outer casing as described in section 5.1.
– Isolate the C.H. flow and return valves (23 fig. 2), and
drain the appliance through the drain plug situated
below the pump.
– Unscrew the expansion vessel pipe union at it’s connec-
tion with the D.H.W. heat exchanger.
– Remove the screw securing the expansion vessel bracket
at the top, rear of the appliance.
– If a rear flue outlet is used it is necessary to disengage
the flue and air duct temporarily. Refer to section 3.5.
– Remove the adjusting screws (5 fig. 7) on the wall
mounting bracket thereby allowing the appliance to
move slightly forwards at the top.
– Lift the expansion vessel, bracket, and pipe out of the
appliance through the top.
– Transfer the bracket and pipe to the new expansion ves-
sel, and re-assemble in reverse order.
Re-pressurise and re-commission the system as descri-
bed in section 4.1.
8.18
SUMMER/WINTER SWITCH
– Remove the outer casing as described in section 5.1.
– Remove the two screws TCB M4 x 10 (2 fig. 14) and pivot
the control box downwards, then remove the two self tap-
ping screws (1 fig. 14) and remove the control box cover.
– Squeeze the switch to depress the retaining clips, then
withdraw the switch forwards.
– Pull off the connections to the switch.
– Fit the new switch and reassemble in reverse order, with
reference to the wiring diagrams in section 7.
8.19
PRESSURE GAUGE
– Remove the outer casing as described in section 5.1.
– Remove the two screws TCB M4 x 10 (2 fig. 14) and
pivot the control box downwards.
– Isolate the C.H. flow and return valves (23 fig. 2).
– Drain the appliance through the drain point situated
below the pump.
– Unscrew the pressure sensor from the top of the safety
valve.
– Squeeze the gauge to depress the retaining clips, then
ease the gauge forwards.
– Reassemble in reverse order. Refil and recommission the
system as described in section 4.1.
8.20
SAFETY VALVE
– Remove the outer casing as described in section 5.1.
– Remove the two screws TCB M4 x 10 (2 fig. 14) and
pivot the control box downwards.
– Isolate the C.H. flow and return valves (23 fig. 2).
– Drain the appliance through the drain point situated
below the pump.
– Unscrew the pressure sensor from the top of the safety
valve.
– Unscrew the union supporting the outlet pipe from the
valve, and remove the valve by unscrewing it from the
main pipe connection.
– Fit the new safety valve using a suitable jointing com-
pound and reassemble in reverse order. Refil and recom-
mission the system as described in section 4.1.
8.21
AUTOMATIC AIR VENT
– Remove the outer casing front panel as described in
section 5.1.
– Refer to fig. 8. Remove the casing R.H. side panel by
unscrewing the two fixing screws.
– Isolate the C.H. flow and return valves (23 fig. 2).
– Drain the appliance through the drain point situated
below the pump and unscrew the automatic air vent.
– Fit the new automatic air vent using a suitable jointing
compound and reassemble in reverse order. Refil and
recommission the system as described in section 4.1.
8.22
VIEWING WINDOW
– Remove the outer casing and sealed chamber front
panel as described in section 5.1.
28
Содержание SUPER 102
Страница 1: ...Super Combination Boilers installation and servicing instructions...
Страница 2: ......
Страница 25: ...21 7 INTERNAL WIRING DIAGRAMS AND VIEWS 7 1 FUNCTIONAL FLOW WIRING DIAGRAM Fig 23 a...
Страница 26: ...22 7 2 ILLUSTRATED WIRING DIAGRAM Fig 23 b...
Страница 35: ......