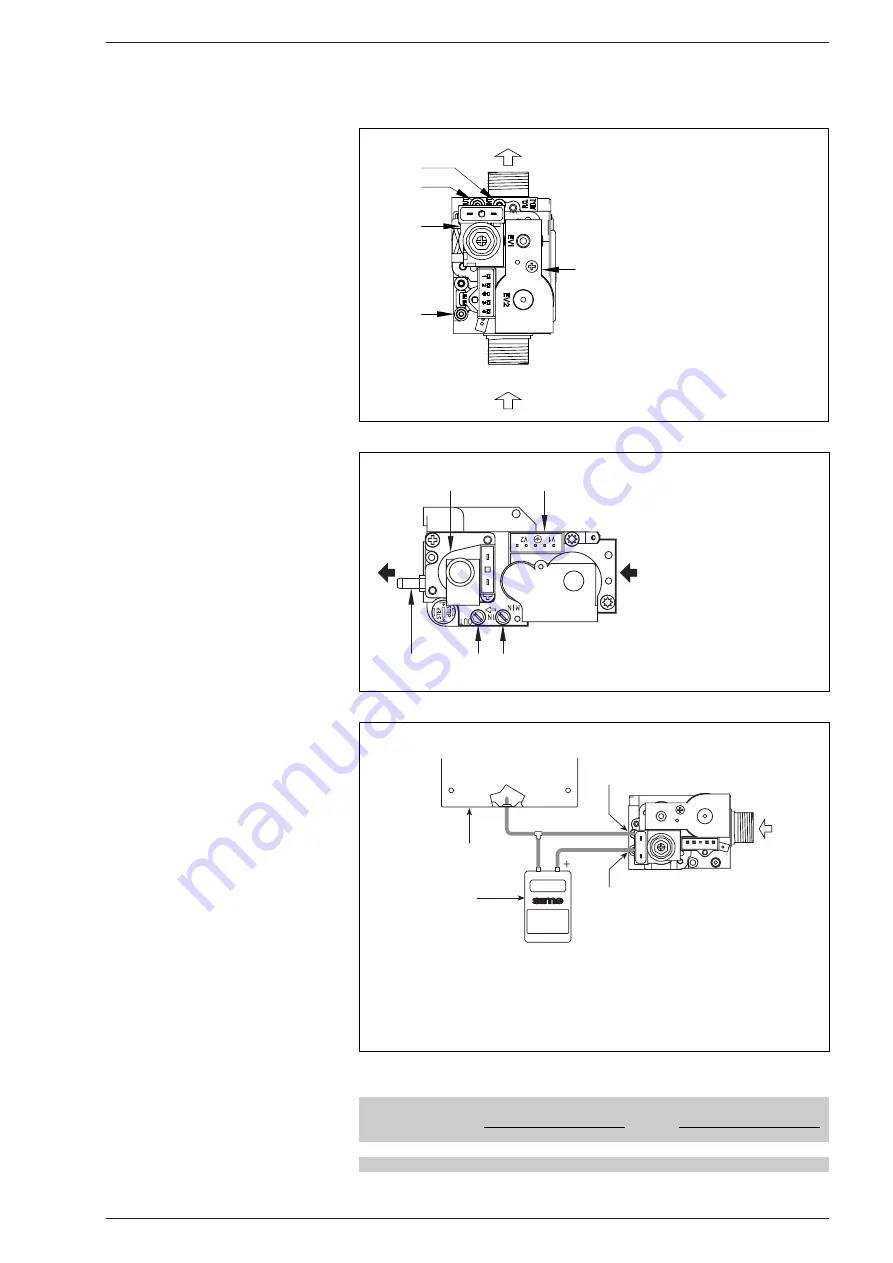
16
SIME SUPPORT THE
BENCHMARK INITIATIVE
All relevant sections of the logbook must be
filled in at the time of installation and there-
after service information on the back page
of the logbook.
Commissioning of the boiler is not com-
plete until the logbook is filled in.
5.1
D.H.W. PRODUCTION
The preparation of hot water is guaranteed
by the glass enamelled tank unit with mag-
nesium anode for the protection of the tank
and inspection flange for its control and
cleaning. The magnesium anode must be
checked annually and substituted when it is
worn. If the boiler does not produce hot
water, make sure that the air has been
released by pressing on the manual vents
after having switched off the main switch.
5.2GAS VALVE
The boiler is produced with SIT 845 SIGMA
gas valve (fig. 19) and HONEYWELL VK
8105N gas valve (fig. 19/a).
NOTE: In case of replacement of the SIT
gas valve to HONEYWELL or vice-versa,
set propertly the Modureg connector of
electronic panel (14 fig. 17 - point 4.1.2).
With the jumper inserted the boiler is
setted for the SIT gas valve; with the
jumper removed the boiler is setted for
the HONEYWELL gas valve.
The gas valve is set at two pressure values:
maximum and minimum, that correspond,
according to the type of gas, to the values
indicated in
Table 6
.
The setting of the gas
pressure at minimum and maximum values
is carried out by SIME: variations are dis-
couraged. Only in the passing from one
type of gas supply (methane) to another
(butane or propane) is a change in the
working pressure allowed.
It is essential that this operation is car-
ried out by authorised personnel.
Once the change in working pressure has
been carried out, seal the regulators.
When proceeding with the setting of the
pressure, it is necessary to follow a pre-
established order: first the MAXIMUM and
then the MINIMUM.
5.2.1
Maximum and minimum
pressure adjustment
SIT 845 SIGMA
In order to carry out the setting of the max-
imum pressure proceed in the following
way (fig. 21):
– Connect the differential manometer as
shown in fig. 20.
– Remove the plastic cap of the modulator (1).
– Place the D.H.W. potentiometer knob on
the maximum value.
5
USE AND MAINTENANCE
3
4
2
1
5
6
Fig. 19
KEY
1
Modulator
2
EV1-EV2 coils
3
Pressure inlet upstream
4
Pressure inlet downstream
5
VENT plug
TABLE 6
Burner max.
Modulator
Burner min.
Modulator
Gas type
pressure
current
pressure
current
mbar
mA
mbar
mA
Methane (G20)
11.3
130
2.2
0
Butane (G30)
28.9
165
5.5
0
Propane (G31)
36.2
165
7.3
0
1
2
4 3
5
Fig. 19/a
1
2
3
4
Fig. 20
KEY
1
Modulator
2
EV1-EV2 coils
3
Pressure inlet upstream
4
Pressure inlet downstream
5
VENT plug
KEY
1
Pressure inlet downstream
2
VENT plug
3
Sealed chamber
4
Differential manometer
Содержание Planet Super 4 F.S.
Страница 1: ...Planet Super 4 F S Installation Servicing Instructions GB...
Страница 27: ......
Страница 29: ...Planet Super 4 F S User Instructions GB...
Страница 30: ......
Страница 41: ...Planet Super 4 W M...
Страница 74: ......
Страница 75: ......