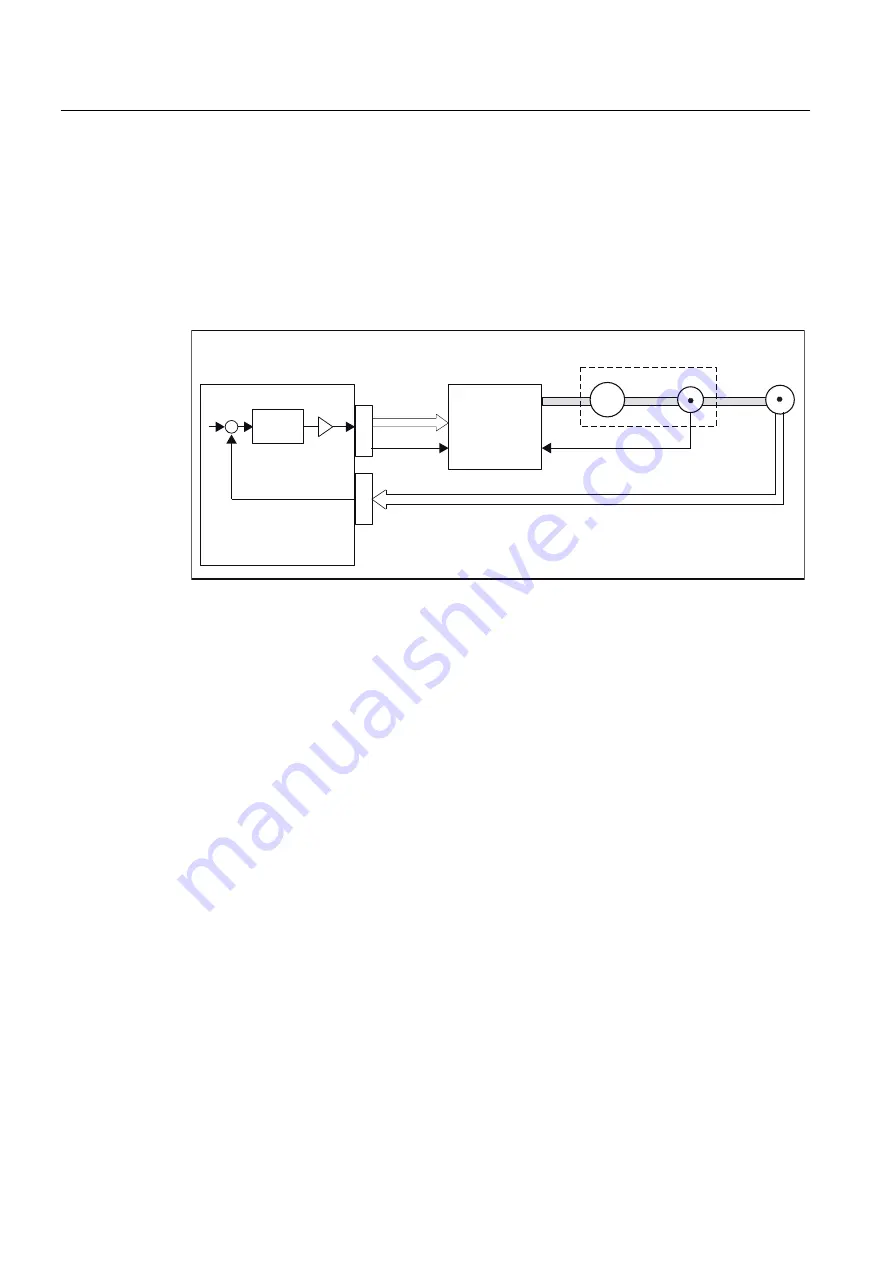
Description
1.3 The fundamentals of motion control
SIMOTION C
20
Operating Instructions, 02/2012
1.3
The fundamentals of motion control
Position-controlled motion control for servo axes via the onboard drive interface (C230-2, C240)
These enable position-controlled motion control of up to four axes. The C230-2/C240
provides one analog output per axis for the speed setpoint and one encoder input per axis
for the cyclic measurement of the actual position value.
&RQYHUWHU
$FWXDOSRVLWLRQYDOXH]HURPDUN
(QFRGHU
$FWXDOVSHHGYDOXH
6HUYRPRWRU
6SHHG
FRQWUROOHU
&XUUHQW
FRQWUROOHU
3RZHUXQLW
UHOHDVH
6SHHG
VHWSRLQW
'$&
3RVLWLRQ
FRQWUROOHU
;
;
0
a
;
;
;
&&
Figure 1-4
Servo system with converter, e.g. SIMODRIVE 611 universal, with built-in incremental
encoder
Incremental encoder (C230-2, C240)
For position measurement, the encoders usually connected supply counting pulses
according to their resolution for the distances traveled. These can be rotary encoders or
linear scales.
Homing is necessary to determine the absolute position reference.
Absolute encoder (SSI, C230-2, C240)
Instead of conventional incremental encoders, which supply only a relative dimension for the
distance traveled, absolute encoders with a serial interface can be connected. No homing
operation need be performed for these encoders as they always supply the absolute position
as an actual value.
A one-time adjustment is required for an axis with an absolute encoder when the machine is
initially commissioned.