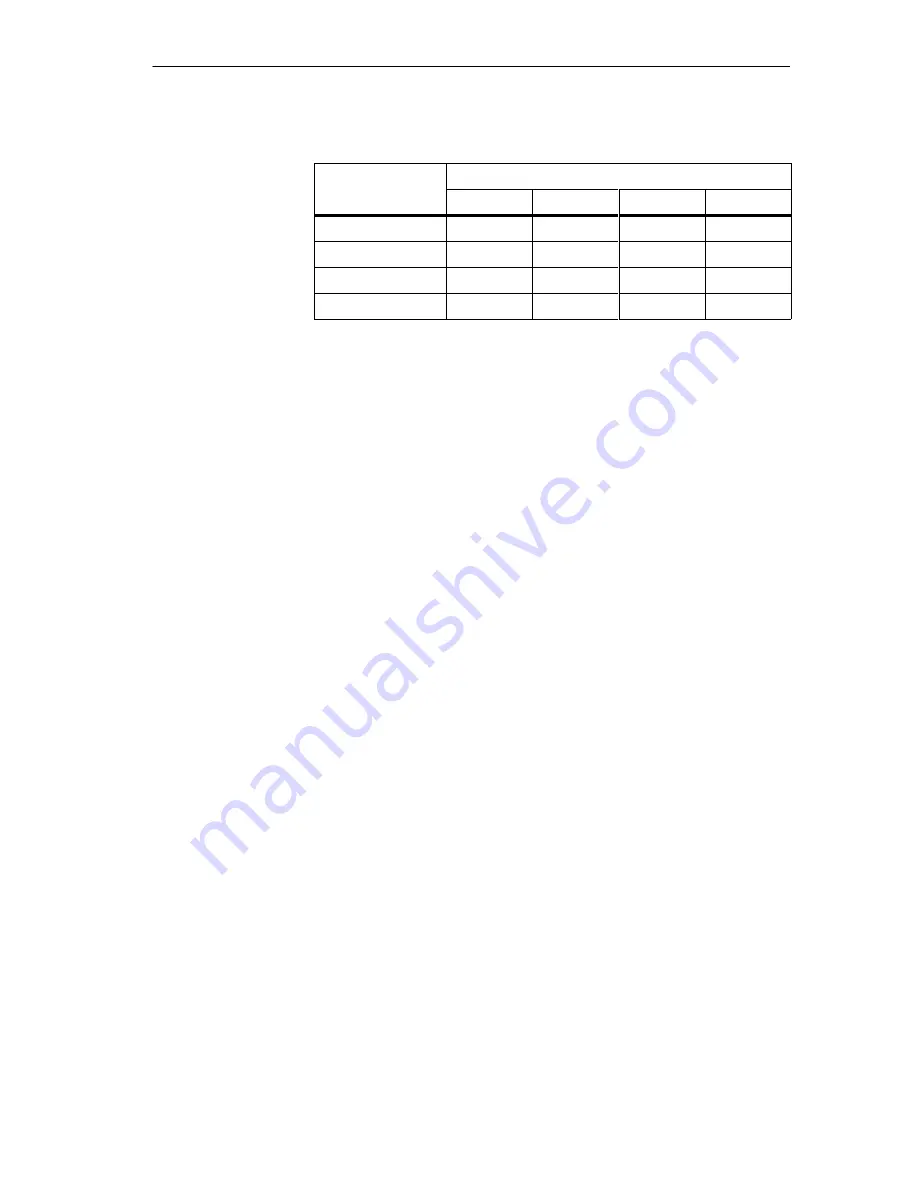
C-7
Communications Processor CP 541
EWA 4NEB 812 6188-02
Table C-6
User-Defined Bus Profile (in Bit Times)
Parameter
Transmission rate in Kbps
93.75
187.5
500
1
1500
SET (T
SET
)
45
80
80
80
ST (T
SL
)
240
400
1000
3000
SDT 1 (min T
SDR
)
45
80
80
150
SDT 2 (max T
SDR
)
200
360
360
980
1
These values are entered in default DB1.
You must use the basic parameters of the slowest station in SINEC L2. The
slowest station is the one with the highest value in parameter ST (slot time).
If you find that these values do not meet the requirements of your SINEC L2
configuration, you can modify the values. Ensure that you change the values
in all stations.
The following example shows the contents of block SL2 in DB1 for an active
CP 541 with station number (TLN) 1, a transmission rate of 500 Kbps and the
user-defined bus profile.
The highest station number of an active station is 30. The token rotation time
is set for the maximum possible communication size of 29 stations. The setup
time has been set to 80 bit times, the slot time to 1000 bit times, the smallest
station delay time to 80 bit times and the greatest station delay time to 360
bit times.
0:
KS =’SL2:
’;
12:
KS =’TLN 1 STA AKT BDR 500
’;
24:
KS =’HSA 30 TRT 30000
’;
36:
KS =’SET 80 ST 1000 SDT 1 80
’;
48:
KS =’SDT 2 360
’;
User Defined
Adjusting the
Values
Optimization
Example of SL2
Parameters of DB1