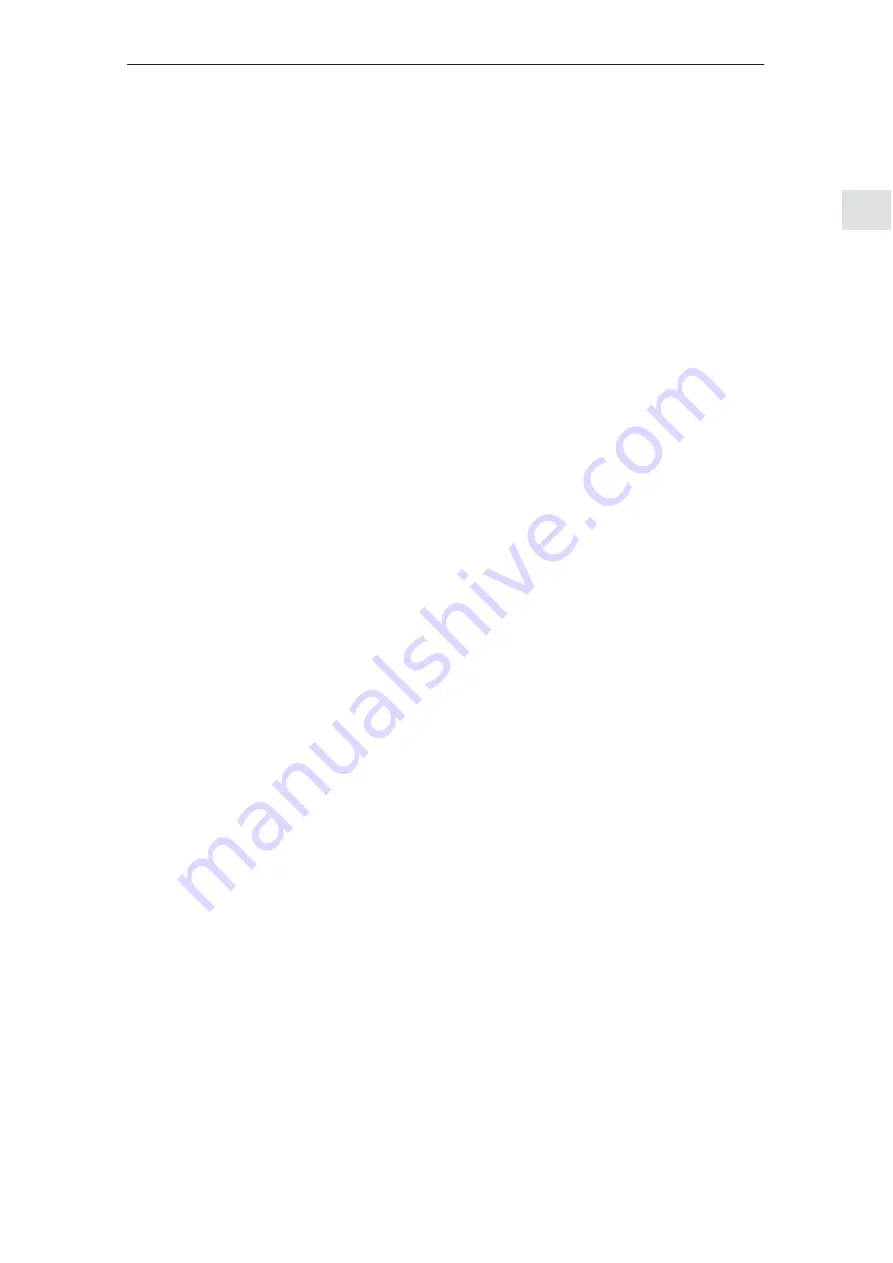
2 System Configuration
2
05.01
2.4 Position sensing/actual speed value sensing
2-49
©
Siemens AG 2012 All Rights Reserved
SIMODRIVE 611 Configuration Manual (PJU) – 02/2012 Edition
2.4
Position sensing/actual speed value sensing
The encoder system is used for precise positioning and to determine the actual
speed value of the drive motor for the particular application. The resolution of
the measuring system and the control board selected are decisive when it
comes to positioning accuracy.
2.4.1
Position sensing, direct
S
Rotary encoders with sine/cosine–shaped voltage signals.
S
Linear scales with sine/cosine–shaped voltage signals.
S
Distance–coded measuring systems (only SIMODRIVE 611 digital with NC)
S
Measuring systems with sine/cosine–shaped voltage signals and EnDat/SSI
interface (linear scales, singleturn and multiturn encoders)
The feed and main spindle drive modules can be supplied with a second mea-
suring system evaluation, e.g. for a table–top measuring system or for spindle
position sensing. A direct measuring system is needed, for example, when a
high degree of accuracy has to be achieved on the workpiece with a linear
scale or exact positioning is required with a multi–stage gear unit.
The optimum measuring system for position detection is suitable for the evalua-
tion of incremental encoders with sine/cosine voltage signals. It is possible to
connect linear scales and rotary encoders with sinusoidal voltage signals to
drive controls to operate 1FT6 and 1FK6 feed motors. The measuring signals
supplied by the encoder system are evaluated with a high degree of resolution.
Example:
With a linear scale (20
μ
m grid constant) a position resolution of 0.01 mm (Digi-
tal High Performance control) is achieved.
Description
Measuring
systems
that can be
evaluated
SIMODRIVE 611
digital, universal
02.07