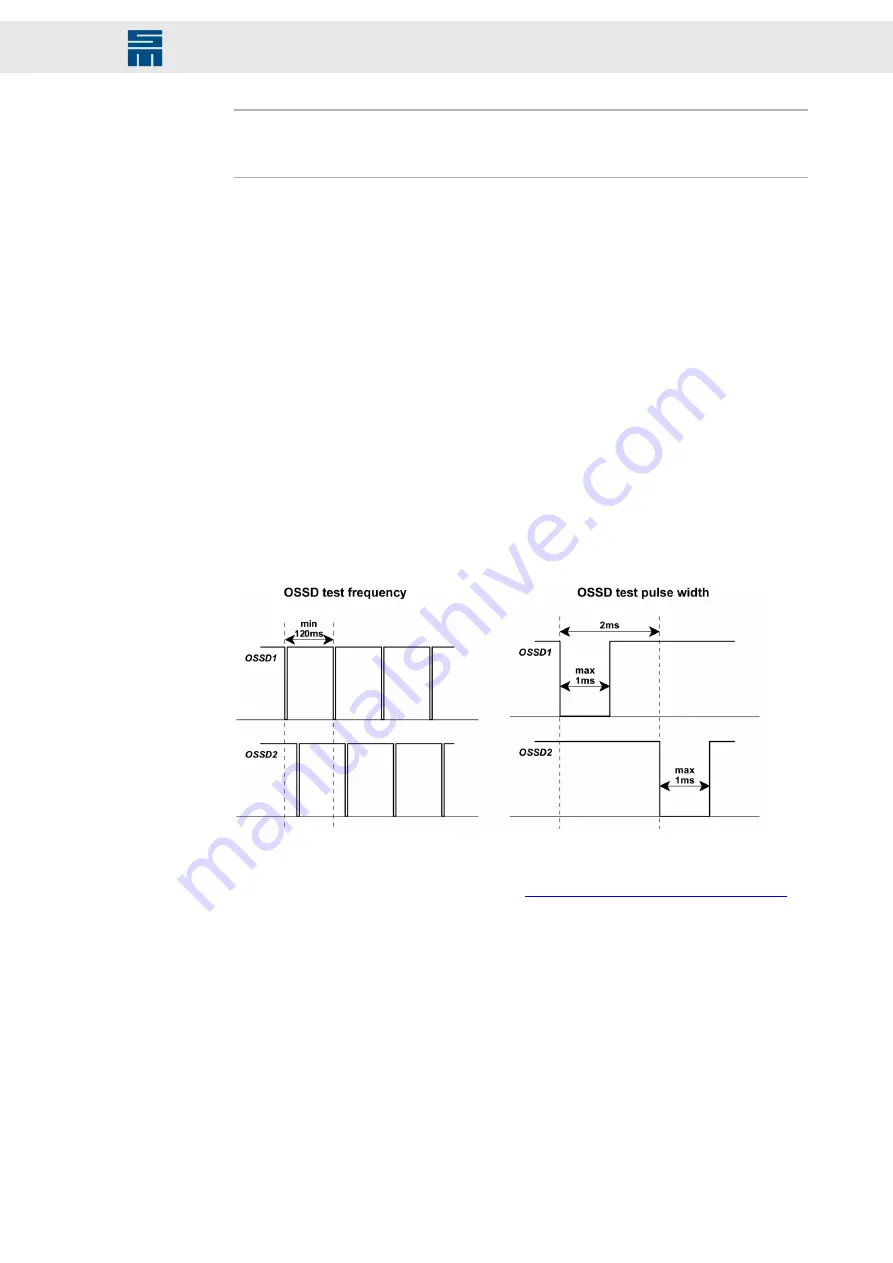
Note
All mounting locations for safety devices of the control system as well as components
mounted outside have to correspond to an IP code IP54, if mounted correctly.
10.1
Functional Description of the Restart Lock
The restart lock locks the respective drive of an installation. All further drive modules
(servo amplifiers / frequency converters) remains ready for operation.
A TÜV checked safety circuit accesses relevant control of the output stage transistors of
the drive to be locked by interrupting the voltage supply of the controls. Thus, no control
pulses can be passed on to the transistors of the output stages and the motor is at a
secure standstill.
OSSD (Output Signal Switching Device)
Part of the contactless protective unit (German abbreviation = BWS) which is connected
with the machine control and which switches over into the OFF state, when the sensor
unit is triggered during the intended operation. (Source IEC 61496-1).
The OSSD signal is a pulsed signal, of which the phase position is shifted in relation to
the different channels. All error can be detected by checking the pulse pattern, short-
circuit for supply, cross-circuit or defect of the device. This ensures a very high safety
level (SIL 4).
Fig. 14: OSSD
The TÜV checked safety circuit is controlled by the OSSD1+2 signal or via one or sever-
al emergency stop switch devices. See also
chapter 10.2 “Wiring Example”, page 58
If the OSSD signals or at least one of the +24 V conductors fail, the safety circuit switch-
es the pulse pattern of the output stage control sectors off. The response time of the
restart lock is
max. 4 ms
.
The restart lock must only be controlled when
▸
the drive is at a secure standstill (stop category 2),
▸
the higher-ranking control has deactivated the drive module,
▸
(reference speed value 0)
▸
the holding brake of the motor has been arrested.
57
Drive Amplifier SD2B plus - 0362171DA1xxxx, 0362171DB1xxxx
Safety circuit / restart lock (STO)