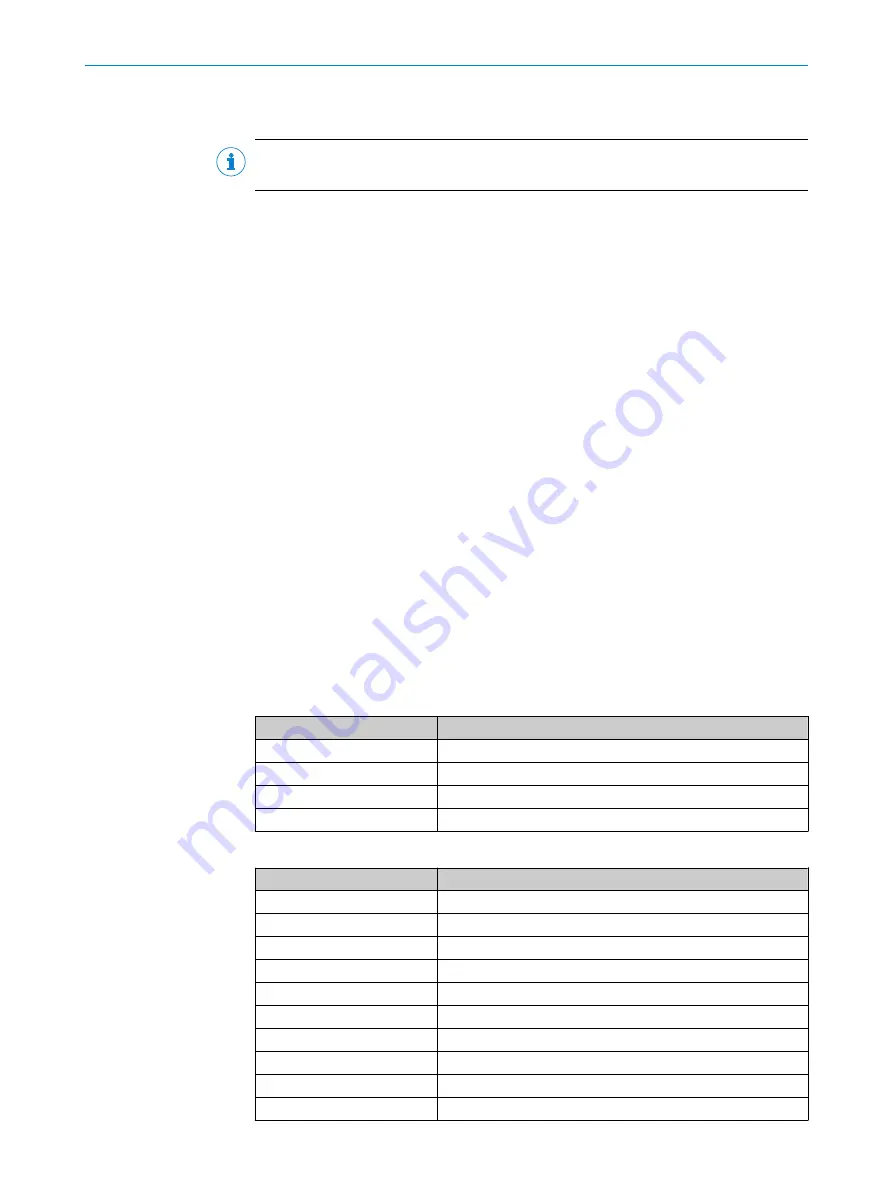
6
Electrical installation
NOTE
Information is included in the operating instructions for the components.
6.1
General requirements
The manufacturer must take measures against failures resulting from the same cause.
These are to be documented in SISTEMA accordingly. During the electrical installation,
the following, for example, must be taken into consideration:
•
Separation of the signal pathways for the safety system signals, e.g., by separated
cable laying
•
Protection against overvoltage, overcurrent, etc. per the manufacturer instructions
for the individual components
•
Mechanical fastening of the wiring of the pushbutton for the hold to run device,
e.g., with cable ties
•
Measures for controlling the consequences of voltage failure, voltage fluctuations,
overcurrent and undercurrent in the voltage supply of the robot controller
6.1.1
Measures when using relays
External device monitoring (EDM) of the relays is necessary to achieve high diagnostic
coverage. For this reason, the relays must have mechanically connected, positively
guided contact elements.
This must be evaluated by the manufacturer or integrator. The number of switching
cycles must also be evaluated by the manufacturer or integrator with respect to compli‐
ance with the safety requirements.
6.2
Safety controller pin assignment
Manual reset
Table 14: UE410-MU4T0 main module inputs
Connection
Function
I1
OSSDs of primary protective device (e.g. safety light curtain)
I2
OSSDs of primary protective device (e.g. safety light curtain)
I3
OSSDs of safety laser scanner
I4
OSSDs of safety laser scanner
Table 15: UE410-MU4T0 main module outputs
Connection
Function
Q1
Not used
Q2
Not used
Q3
Protective stop
Q4
Protective stop
X1
Test output, connected to S1
X2
Not used
EN
Enable, connected to +24 V DC
A1
Voltage 24 V DC
A2
Voltage supply 0 V DC
S1
Connected to X1
6
ELECTRICAL INSTALLATION
38
O P E R A T I N G I N S T R U C T I O N S | sBot Stop
8023421/12KF/2019-01-22 | SICK
Subject to change without notice