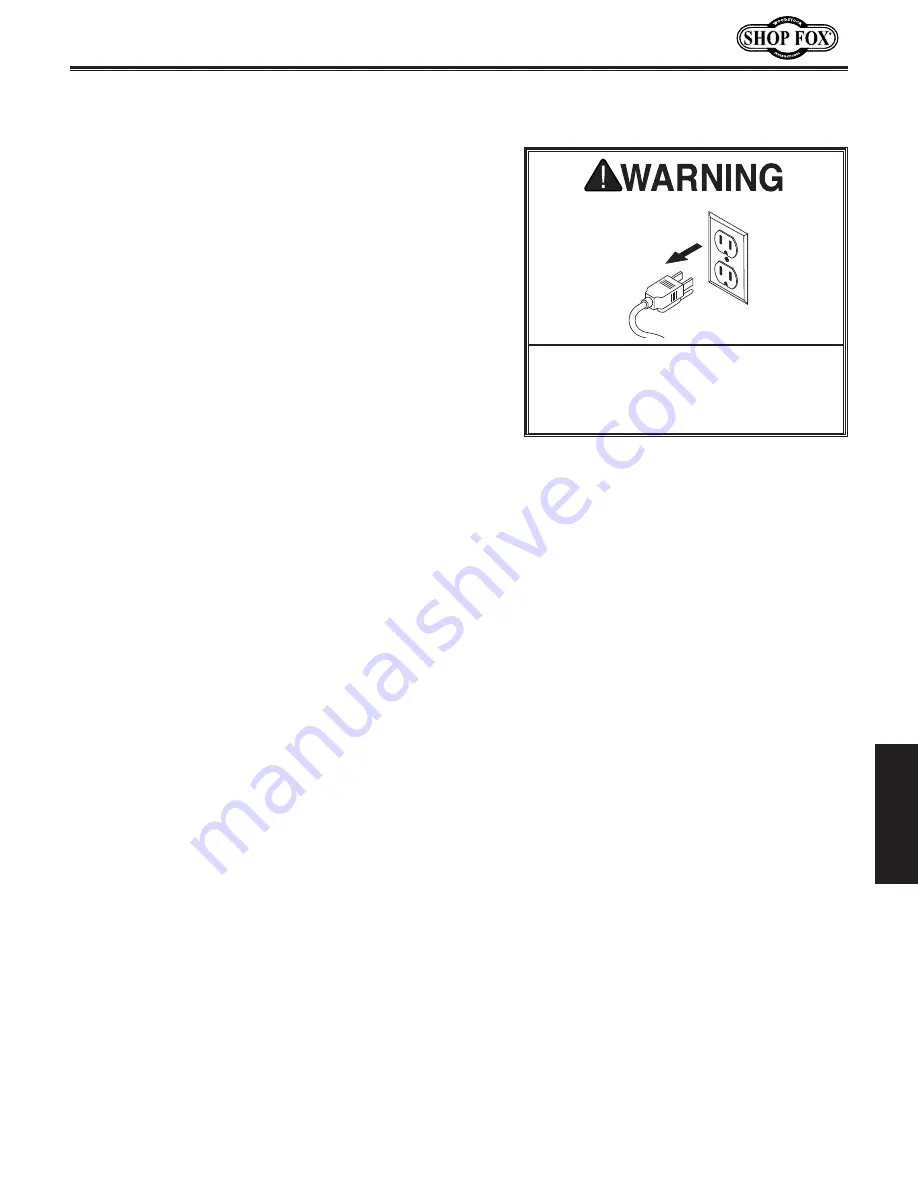
-37-
Model W1745W (For Machines Mfd. Since 9/16)
M
A
INT
EN
A
NC
E
MAINTENANCE
MAKE SURE that your machine is
unplugged during all maintenance pro-
cedures! If this warning is ignored,
serious personal injury may occur.
Cleaning the W1745W is relatively easy. Vacuum excess
wood chips and sawdust, and wipe off the remaining dust
with a dry cloth. If any resin has built up, use a resin-
desolving cleaner to remove it.
Protect the unpainted cast-iron table by wiping it clean
after every use—this ensures moisture from wood dust
does not remain on bare metal surfaces. Keep the table
rust-free with regular applications of quality lubricants.
Cleaning & Protecting
For optimum performance from your machine, follow
this maintenance schedule and refer to any specific
instructions given in this section.
Daily Check:
•
Inspect cutters for damage or wear.
•
Check for loose mounting bolts/nuts.
•
Check cords, plugs, and switch for damage.
• Check for the proper function of the cutter guard
(see
Page 21
).
• Check for any other condition that could hamper the
safe operation of this machine.
• Wipe the table clean after every use—this ensures
moisture from wood dust does not remain on bare
metal surfaces.
Weekly Maintenance:
• Wipe down the table surface and grooves with a
lubricant and rust preventive such as SLIPIT
®
.
• Vacuum dust buildup from the motor housing and
inside cabinet.
• Clean the pitch and resin from cutterhead with a
cleaner like OxiSolv
®
Blade & Bit Cleaner.
Monthly Maintenance:
•
Check/tighten the V-belt tension (
Page 18
).
Every 6–12 Months:
• Lubricate
table gibs and ways.
General