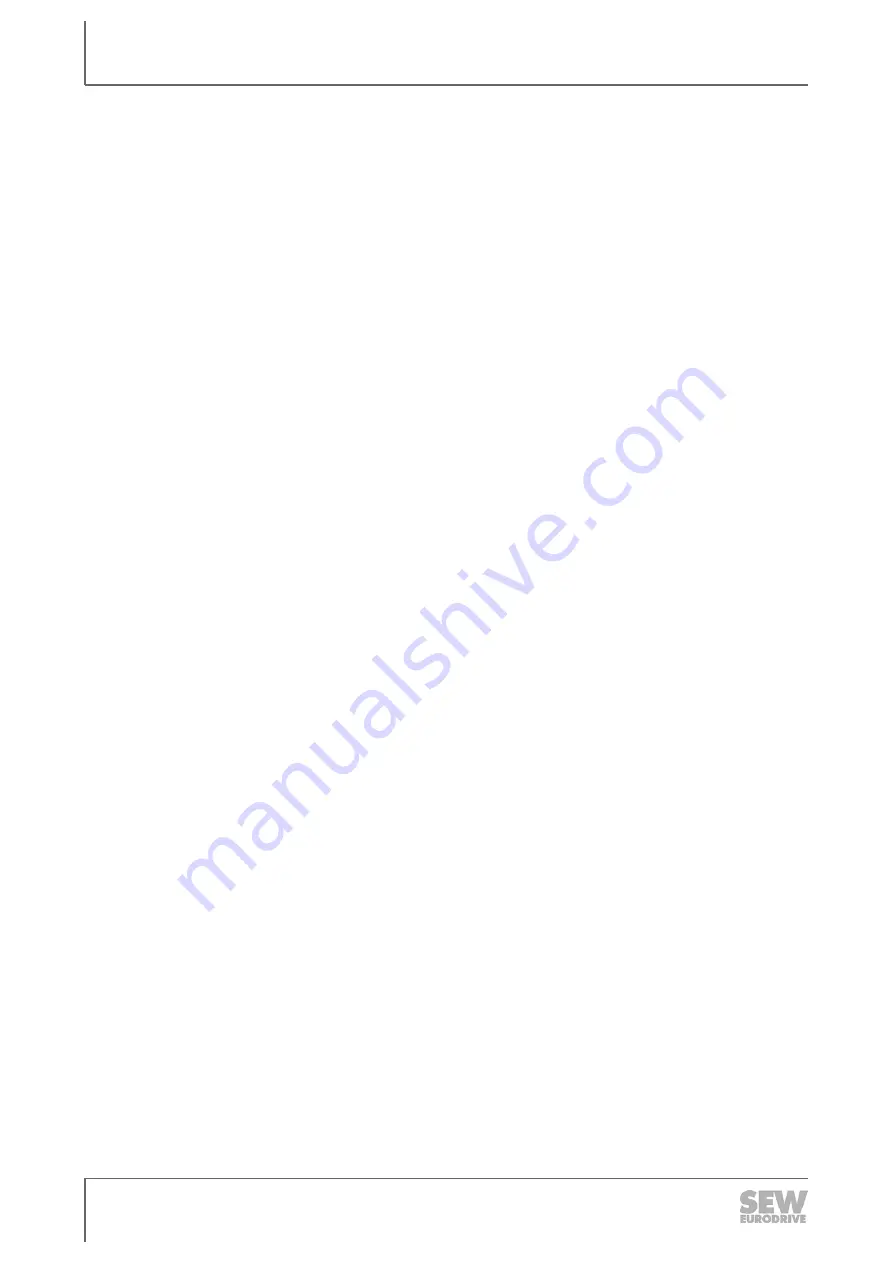
Commissioning
92
Commissioning
21
258
_10
0300
06/EN - 0
3/2
022
Operating manual [27779289/EN] - MAXO-RG single-axis controls
21.6
Operation
During operation, the controls automatically carry out all actions according to the pro-
gramming. This means no actions are necessary during automatic operation.
In the event of a failure, proceed as described in section „"Malfunctions" (
94).“