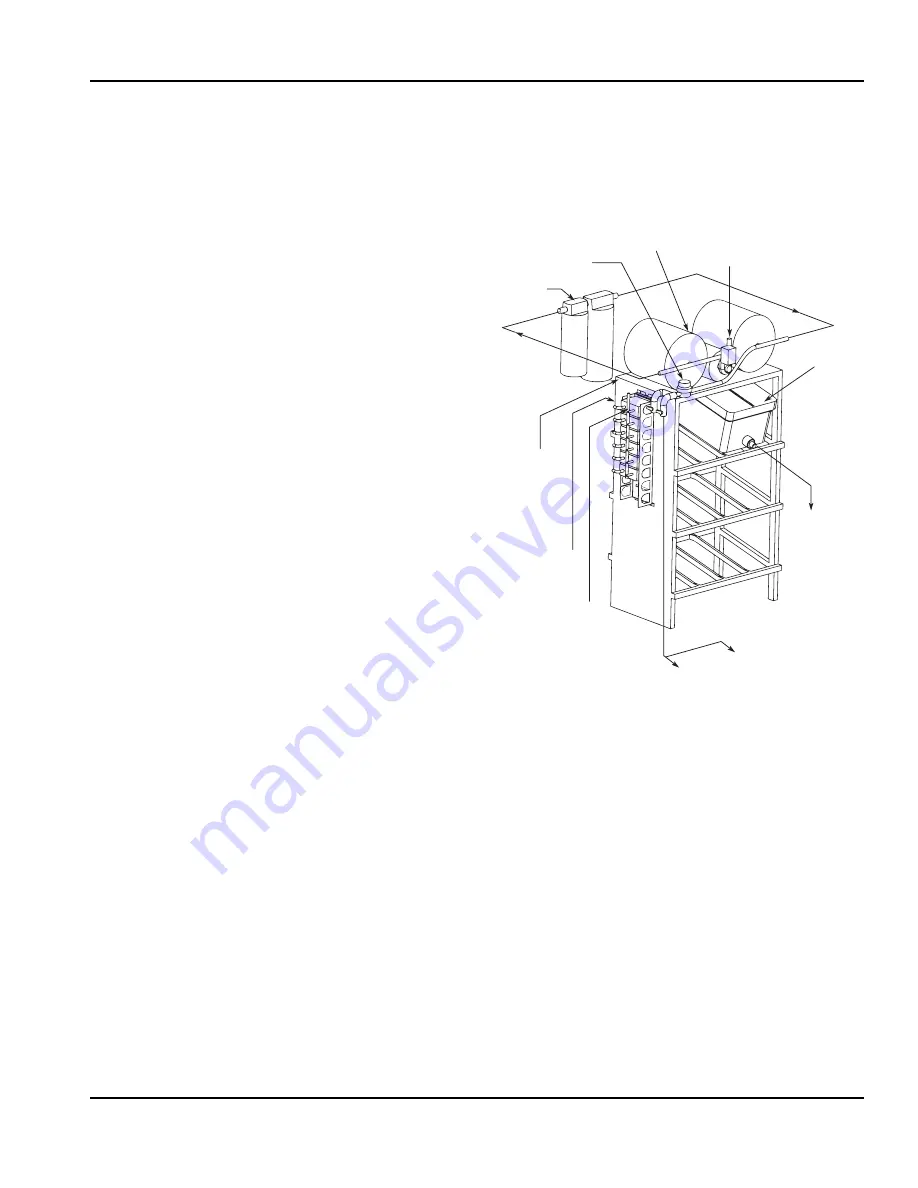
Section 3
Operation
Part Number 5030763
5/11
3-3
Sequence of Operation
BEVERAGE VALVES
Post-mix beverage valves are designed to precisely
meter the flow of both water and syrup to obtain the
proper mixing ratio. The syrup and soda water
components of the post-mix beverage are mixed as they
leave the beverage valve.
CARBONATION
The purpose of the carbonator is to take regular tap
water at street water pressure (minimum 20 PSI,
maximum 80 PSI, dynamic or flowing pressure) 1/2"
water line and increase the water to beverage system
pressure (usually 100 PSI). This water is then combined
with the CO
2
gas. Because the water and gas are at the
same pressure, the CO
2
will dissolve into the water.
Chilling the mixture before dispensing will assist in
locking the carbon dioxide into the water. After
dispensing, the CO
2
may be unlocked from the liquid.
The CO
2
will gradually leave the liquid due to pressure
and temperature changes.
Components
The components of the carbonator are: water pump, an
electric motor to operate the pump, carbonator tank
where the water and CO
2
mix, and a water level control.
Operation
Carbon Dioxide (CO
2
) leaves the storage tank and
arrives at the carbonator tank through the gas inlet.
Water supply enters the carbonator pump inlet at regular
street water line pressure (minimum 20 PSI, maximum
80 PSI, dynamic or flowing pressure). The water pump
increases the pressure of the water, which allows the
water to flow into the carbonator tank. The CO
2
and the
water mix together in the carbonator to produce the
carbonated water that is then sent to the soda dispenser.
The agitation of the water and CO
2
together in the tank
under high pressure creates the soda water. The quality
of carbonation (percent of CO
2
mixed in the water)
increases as the water temperature decreases and
exposure time increases.
The water level in the carbonator tank is controlled by a
water level control in the tank. This control turns the
pump motor off and on to maintain a preset level of liquid
in the tank. The water level control may be electronic
probes or a mechanical float.
SYRUP DELIVERY SYSTEM
Your syrup location can vary depending on the volume
of beverages served and ease of accessibility. Your
beverage system may set in a back storage room or
under the counter of the dispenser. Configurations are
almost limitless. Check the temperatures expected for
the storage location. Adverse temperatures can affect
the storage and quality of beverage products. It is
recommended the temperature of storage location must
not fall below 40°F (4°C) or rise above 90°F (32°C).
BACK ROOM PACKAGE
1.
Incoming tap water –
must be at a minimum
dynamic pressure of 40 psi and maximum static
pressure of 55 psi.
2.
Carbonator Water pump motor –
Powers the
water pump. The water pump motor is part of the
carbonator pump deck.
3.
Carbonator Water pump –
Pumps tap water into
the carbonator tank. The water pump is part of the
carbonator. The incoming water for the carbonator
must be first run through the pump before
connecting to the proper cold plate inlet.
4.
Internal/External Carbonator tank –
Combines
CO
2
gas and tap water to form carbonated water.
The “carbonator” is the carbonator tank, water pump
and water pump motor.
From Water Supply
To Noncarbonated
Water Inlet Barb
Water to
Carbonator
Pump
Filter
Water Regulator
40–55 PSI
Booster System
(If Required)
To CO
2
Manifold (BIB
Pumps) from
CO
2
Supply
60 PSI
To Syrup Inlet
Barbs on Unit
To BIB Pumps
from BIB
To BIB
Pump
BIB