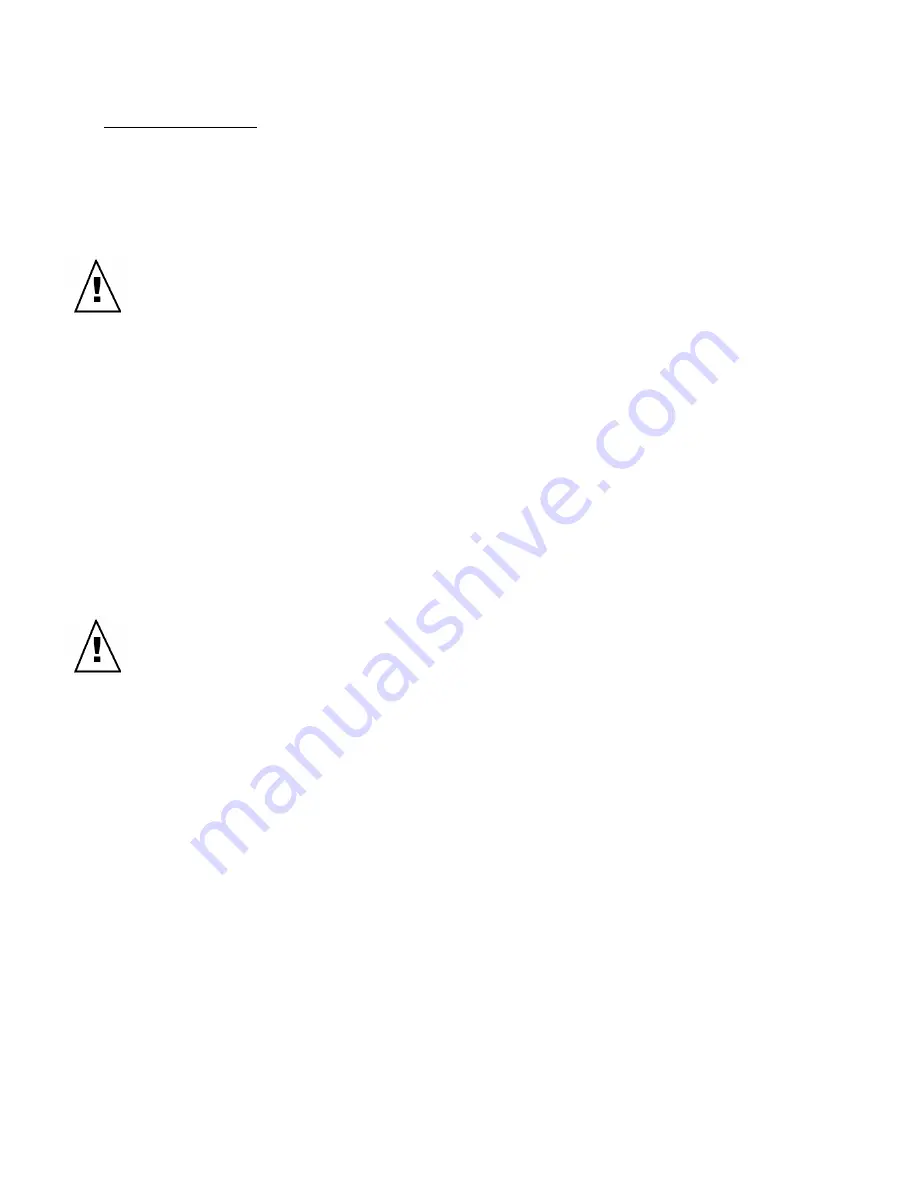
27
b) Liquid Refrigerants: Open the container
slightly and put in a few drops of liquid
refrigerant. Loosely close the container and
allow time for the refrigerant to gasify. A
bag will expand some as the liquid
evaporates.
Caution: Do not close a rigid
sample container tightly, because
refrigerants
expand
and
can
create pressure. Do not allow
pressure to build up in the sample
container.
Step 3:
Manual measurement of sample.
Switch the monitor to manual override.
Manual Override is accessed by pressing
the "ENT" (enter) key on the front panel
display of the monitor. Press the "3" key to
enter Manual Override. Place the 1/4 inch
tube into the sample container and connect
it to the sample inlet to simulate a
concentration of refrigerant in the air.
Caution:
Never
connect
a
pressurized
refrigerant
bottle
directly to the monitor. The unit is
designed to operate only at
atmospheric pressure. Doing so
can damage the unit.
After approximately 5 seconds, the PPM
reading should start to rise. Within 30 to 45
seconds, the PPM level should level off. A
sample prepared as described in step 2
should easily contain more than 150 PPM.
If the PPM reading does not rise above the
highest alarm setting in the monitor, repeat
the sample preparation procedure with a
larger amount of refrigerant. Readings of
150 or higher indicate a successful test of
the monitor's ability to sense refrigerant.
Disconnect the sample from the monitor
and save for the next step. The sample
container should now have a measured
concentration of
refrigerant greater than the
highest alarm level. This will be used to
test the end-to-end performance of the
system in the next step.
Once
the
sample
tube
has
been
disconnected
from
the
monitor,
the
readings should fall slowly down to at or
near zero PPM. When the PPM level
reaches near zero, press the "ENT" (enter)
key to exit Manual Override and return to
normal operation.
End-to-End System Test
After manually verifying the operation of the
monitor, and obtaining (creating) a sample
known to have a PPM level higher than the
highest alarm, the next step is to perform
an end-to-end test of the system. This test
will verify that the monitor will correctly
trigger alarms and the external devices
connected. This will be done by connecting
the sample of refrigerant from the previous
test to the sample inlet and observing the
alarms. This test is best done after the
monitor has run through at least two
complete auto sample and auto zero
cycles.
After approximately 5 seconds, the PPM
reading should start to rise. When the
monitor exceeds the alarm threshold, it will
switch to "Leak Wait" mode. This mode
ensures the presence of a leak before
triggering an alarm. The leak wait period
can be as short as 7 seconds and as long
as 3 minutes.
Note: The more the
reading exceeds the alarm trip point, the
shorter the time to enter alarm.
The
system should progress from Low alarm,
through Main alarm and into High alarm.
Note: If the monitor exceeds high alarm
while in leak wait, it will appear to trigger
Main alarm and High alarm at the same
time. This is normal, correct operation.
Содержание IR-SNIF-MC-1
Страница 54: ...05 21 2008 ...