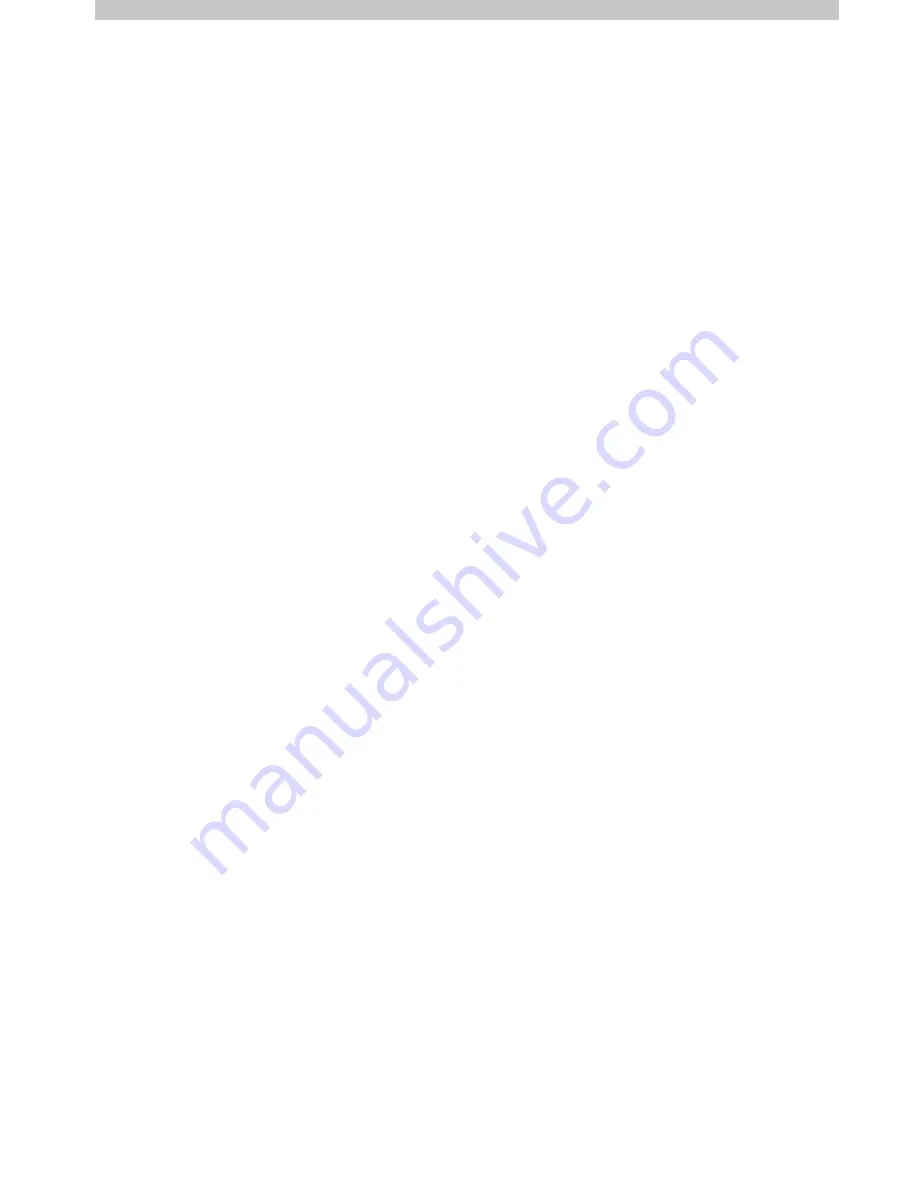
LCQ / LCS / LCQI / BMQ / CPQ / TBQ / TBS / TBQI / TBSI EVAPORATIVE COOLER INSTALLATION MANUAL
|
1
SAFETY
Employer and Employee Responsibilities
The installation and maintenance of evaporative coolers at
height has the potential to create Occupational Health and
Safety issues for those involved. Installers are advised to
ensure they are familiar with the relevant State and Federal
legislation, such as Acts, Regulations, approved Codes of
Practice and Australian Standards, which offer practical
guidance on these health and safety issues. Compliance
with these regulations will require appropriate work practices,
equipment, training and qualifications of workers.
Seeley International provides the following information as a
guide to contractors and employees to assist in minimising risk
whilst working at height.
WARNING - TO REDUCE THE RISK OF FIRE,
ELECTRIC SHOCK OR INJURY TO OTHER PERSONS,
OBSERVE THE FOLLOWING:
1. Use this unit only in the manner intended by the
manufacturer. If you have questions, contact the manufacturer.
2. Before servicing or cleaning the unit, switch power off at
service panel and lock the service disconnecting means to
prevent power from being switched on accidentally. When the
service disconnecting means cannot be locked, securely fasten
a prominent warning device, such as a tag to the service panel.
3. Installation work and electrical wiring must be done by
qualified person(s) in accordance with all applicable codes and
standards, including fire-rated construction.
4. When cutting or drilling into walls or ceilings, do not damage
electrical wiring and other hidden utilities.
5. Ducted fans must always be vented to the outdoors.
6. Do not use this fan with any solid-state speed control device.
7. New hose sets supplied with the appliance are to be used.
Old hose sets (from previous installations) shall not be used.
8. If the supply cord is damaged, it must be replaced by the
Manufacturer, its Service Agent or similarly qualified persons in
order to avoid a hazard.
Installer and Maintenance Contractors
– Risk Assessment
A risk assessment of all hazardous tasks is required under
legislation. A risk assessment is an essential element that
should be conducted before the commencement of work, to
identify and eliminate the risk of falls or to minimise these risks
by implementing control measures. There is no need for this to
be a complicated process, it is just is a matter of looking at the
job to be done and considering what action(s) are necessary so
the person doing the job does not injure themselves.
This should be considered in terms of:
• What are the chances of an incident happening?
• What could the possible consequence be?
• What can you do to reduce, or better still, completely
eliminate the risk?
Some points to consider:
• What is the best and safest access to the roof and working
areas?
• If a worker is alone, who knows they are there and if they get
into difficulty, how can they summon help? (Call someone on
the ground? Mobile phone? etc.).
• What condition is the roof in? Should the trusses, underside
or surface be checked?
• Does the worker have appropriate foot wear?
(Flat sole jogger type is advisable).
• Are all power cables / extension leads safe and appropriately
rated?
• Are all ladders, tools and equipment in a suitable and good
condition?
•
Where ladders are to be used, is there a firm, stable base for
them to stand on? Can they be tied or secured in some way
at the top? Is the top of the ladder clear of electricity supply
cables?
• Is there a roof anchor to attach a harness and lanyard to? If
so, instruction should be issued for the use of an approved
harness or only suitably trained people used.
• Are all tools and materials being used, prevented from
slipping and falling onto a person at ground level? Is the area
below the work area suitably protected to prevent persons
walking in this area?
• Does the work schedule take into account weather conditions,
allowing for work to be suspended in high winds, thunder
storms/lightning or other types of weather giving wet, slippery
surfaces?
•
Is there an on-going safety check system of harnesses,
ropes, ladders and access/lifting equipment and where they
exist on roofs, anchor points before the commencement of
work?
• Is there a system which prevents employees from working
on roofs if they are unwell or under the influence of drugs or
alcohol?
• Are there any special conditions to consider?
(Eg: excessive roof pitch, limited ground area, fragile roof,
electrical power lines, etc)
Other Important Requirements
•
Never force parts to fit because all parts are designed to fit
together easily without undue force.
• Never drill holes in the tank of the cooler.
• Check the proposed cooler location, to ensure that it is
structurally capable of supporting the weight of the cooler, or
provide an adequate alternate load bearing structure.
• Ensure the installation complies with all local and national
regulations with regards to electrical, plumbing and bushfire
construction requirements.