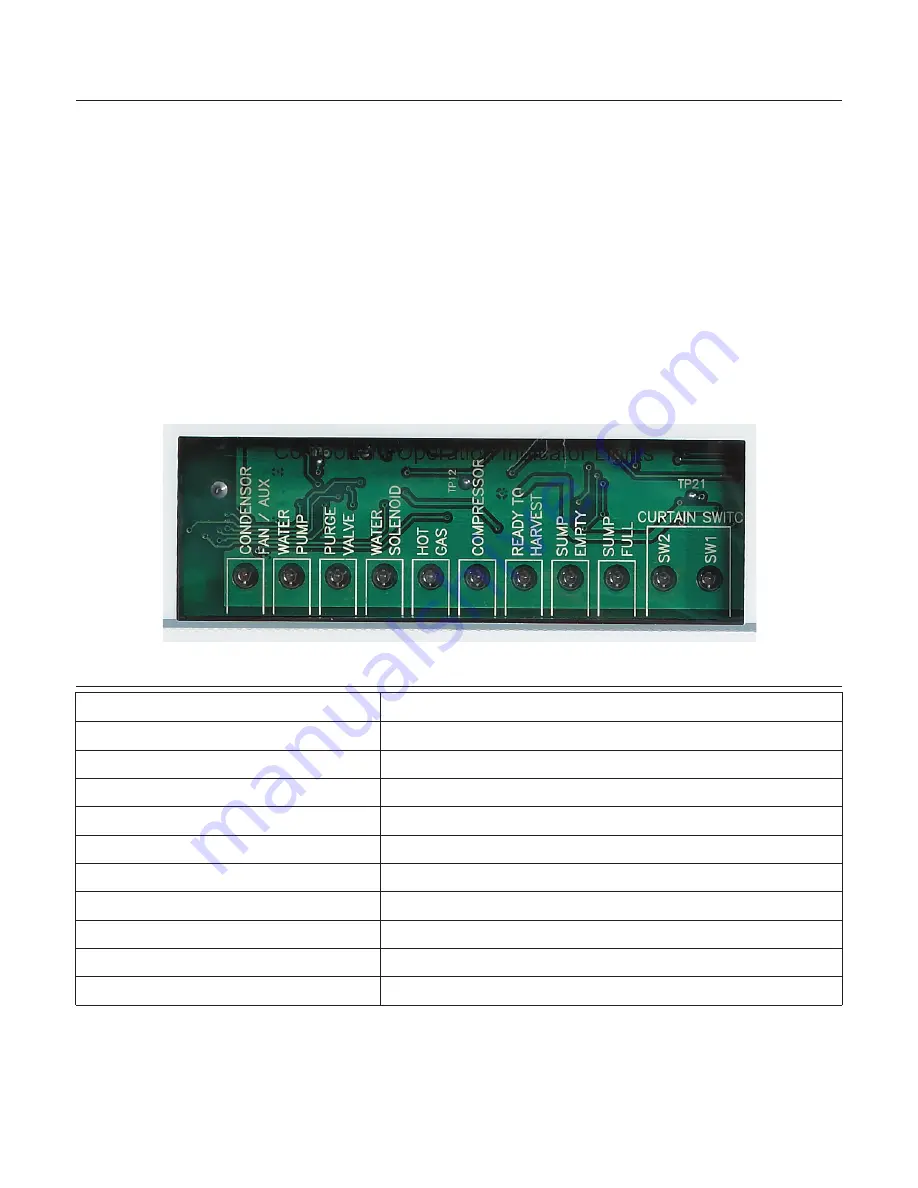
Controller Information
Component Indicator Lights
•
Condenser Fan / Aux
•
Water Pump
•
Purge Valve
•
Water Solenoid
•
Hot Gas
•
Compressor
•
Ready to Harvest
•
Sump Empty
•
Sump Full
•
Curtain SW1
•
Curtain SW2
May 2008
Page 15
CU1526, CU2026, CU3030
Service Manual
Component Indicator Light Table
System
Indicator Light ON
Condenser Fan / AUX
Fan Motor Powered
Water Pump
Pump Motor Powered
Purge Valve
Purge Valve Opens
Inlet Water Solenoid Valve
Not used this model
Hot Gas
Hot Gas Valve Opens and harvest assist solenoid powered
Compressor
Contactor Closes
Ready to Harvest
Water contacting ice thickness sensor probe
Sump Empty
Open between mid sensor and common
Sump Full
Closed between top probe and mid probe
Curtain Switch
Curtain open