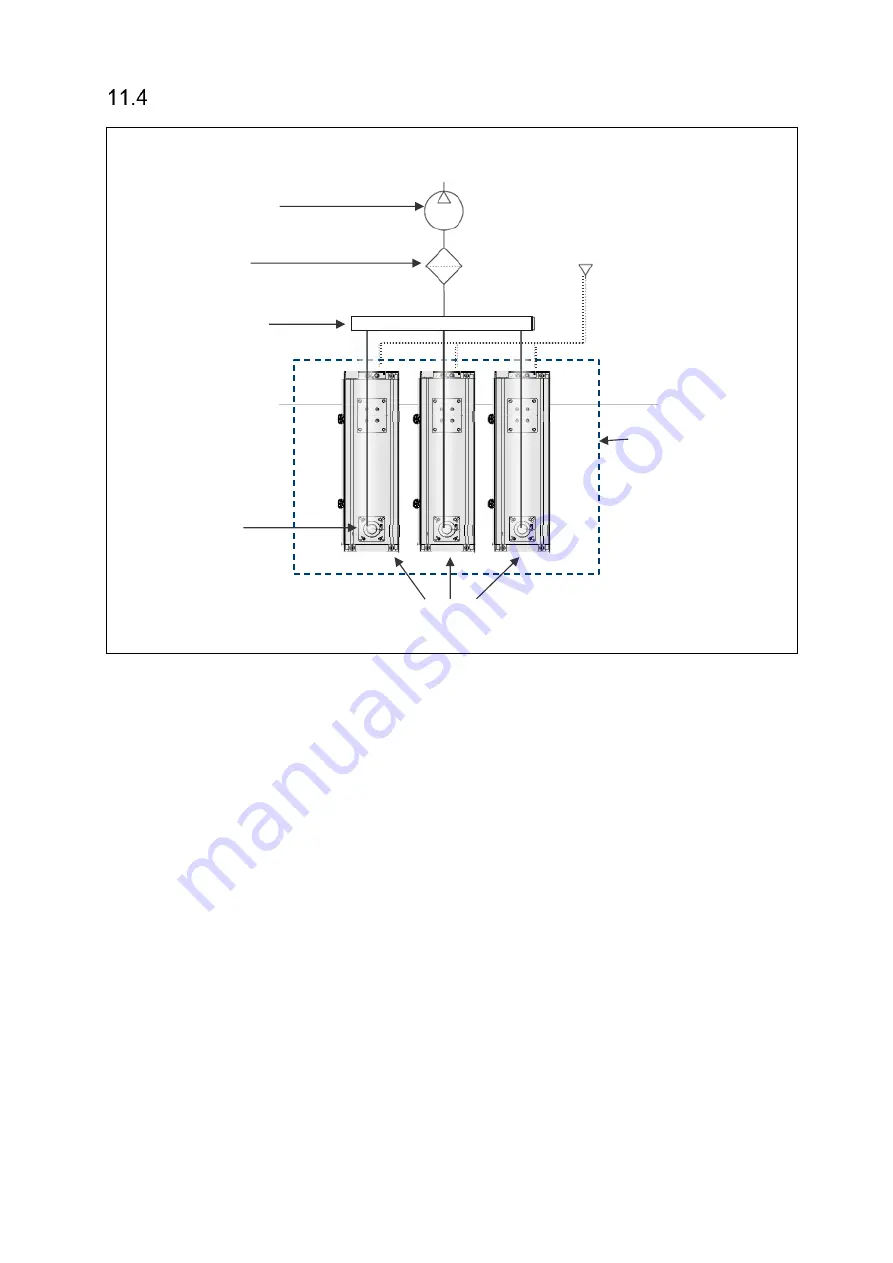
30.30.01.01648/06
www.schmalz.com
EN | 59
Pneumatic Circuit Diagram of the FMHD
– Parallel Circuit
12 Other Applicable Documents
EC declaration of incorporation FMHD
30.30.01.01665
Product Declaration of Conformity
30.30.01.02574
For versions with ejector and dust filter
Ejector instruction manual
30.30.01.01005
Dust filter instruction manual
30.30.01.00059
Compressed air source
Optimum flowing compressed
air pressure 6.0 bar
Vacuum distribu-
tor
Vacuum filter
Hose
clamps/connector
Vacuum
Included in
delivery
Vacuum area gripper
FMHD
Vacuum generator
Содержание FMHD
Страница 60: ...60 EN www schmalz com 30 30 01 01648 06 ...