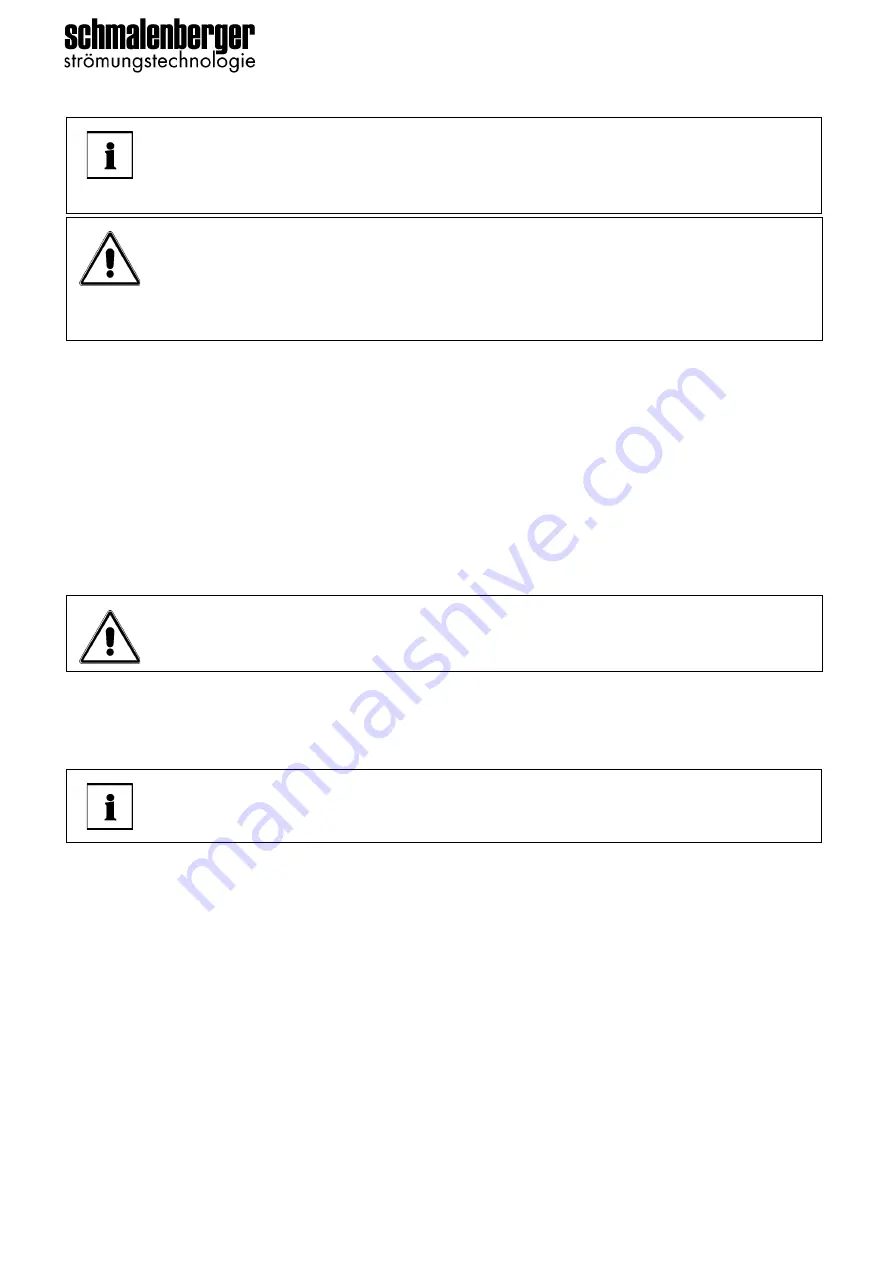
12
Pump NB/FB/WP/SM/F
Version: 27216 - E
Schmalenberger GmbH + Co. KG
D-72072 Tübingen / Germany
2.3.3
Connecting the Pipelines
For short pipelines, the nominal widths should at least match those of the pump
connections. For longer pipelines, determine the most cost-effective nominal width from
case to case.
Transition pieces to larger nominal widths should be designed with an expansion angle of
about 8° to prevent increased pressure loss.
The suction line rises continuously to the pump. Lay pipelines continuously falling for the
supply to prevent air lock from forming.
Depending on the type of system and pump, installation of backflow prevention valves and
shut-off elements is recommended.
Expansion of pipelines due to temperature must be countered by suitable measures. We
recommend installing compensators in the pipeline.
Always avoid fittings in pipelines that close suddenly (rapidly). Pressure peaks which occur
as a result of these fittings may exceed the maximum permissible housing pressure of the
pump several times over! To avoid strong pressure peaks, install pressure absorbers or air
chambers.
Often welding beads, pipe scale and other impurities do not come loose until some time
has passed. They must be kept out of the pipe by installing a sieve in the suction line. The
open cross-section of the sieve must be at least three times the cross-section of the
pipeline to prevent too much resistance from building up due to trapped foreign objects.
Experience shows that hat-shaped sieves containing a mesh wire net with a mesh size of
2.0 mm and a wire diameter of 0.5 mm and made of corrosion resistant material are
effective.
The pump must never under any circumstances be used as a point for securing
the pipeline. No forces or moments (for example caused by warping or heat
expansion) from the pipelines may be allowed to affect the pump. Pipes must
be intercepted directly before the pump and connected with no tension.
Danger of death! When working with hot, corrosive ,and toxic pumping
media!
If pipeline forces are exceeded, points with faulty seals may develop on the
pump itself or on the flange connections, which may result in powerful ejection
of pumping medium.
Important
Pipe compensators must not be used to make up for inaccuracies in the
pipelines, for example with a centre offset of the flange.
After assembly is complete or before starting up the system, the containers,
pipelines and connections must be thoroughly cleaned, rinsed and blown out
with air.