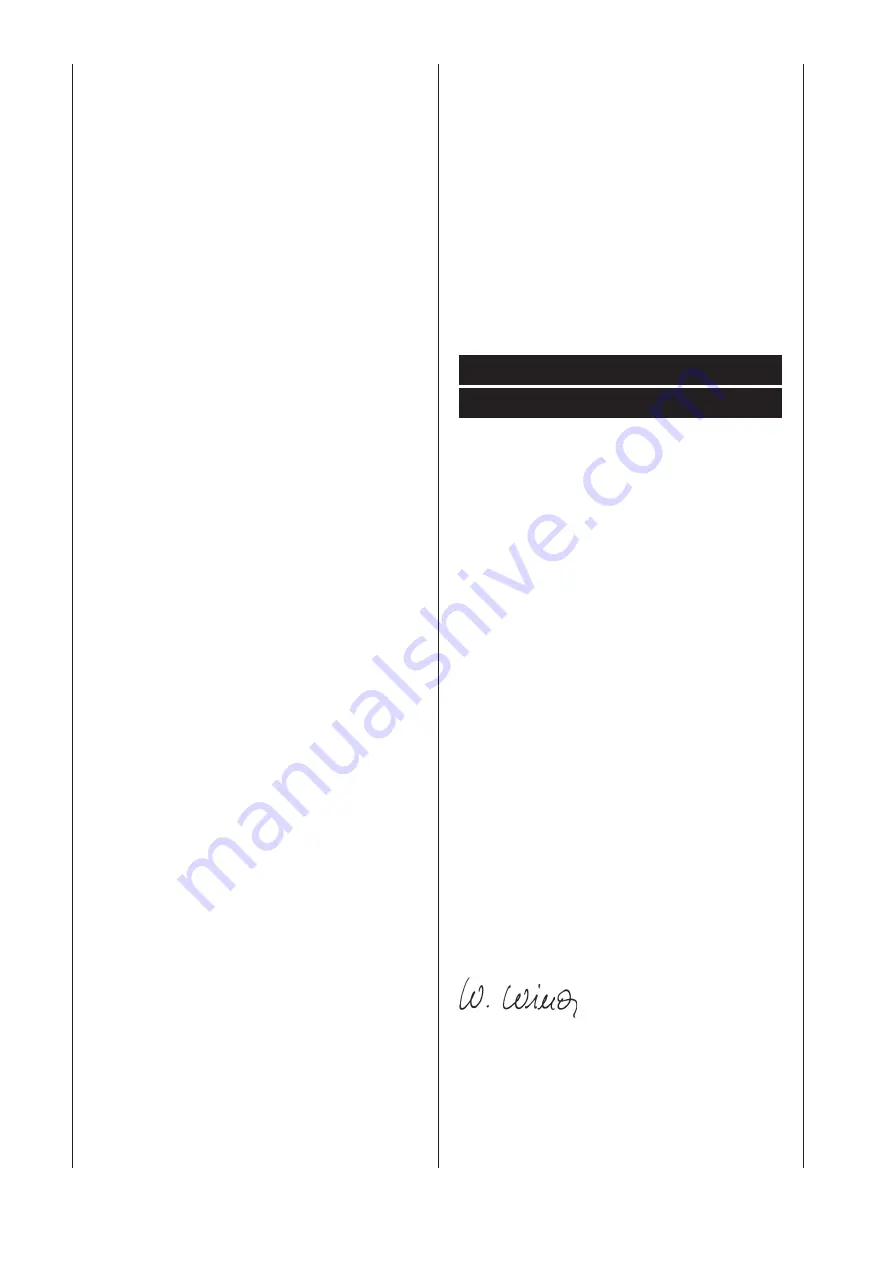
english 15
shaft and the tool spindle. In new conditions, warming is
part of the design but it goes away after some time.
Clean the feeder cylinders regularly.
Oil the bearing and shaft with hinges of the sliding bearing
of the feeder cylinders and the adjustment spindle of the
thicknessing table after the first 5 hours of operation. After
that, oil every 20 hours of operation.
Check the chain tension. If needed, tighten and oil it.
When tightening the thicknessing table chain, pay atten-
tion to the prallelism of the thicknessing table.
Planer blades
The planer blades at work are beveled and setup correctly,
ready for use.
Only well-sharpened and exactly set planer blades can
guarantee safe operation.
We recommend:
Always keep a spare beveled planer blade ready, in need
of replacement.
You can find a spare planer blade from your specialist Type
Nr. 6200 4134.
Feed unit Fig. 13.2 – Warning!
The plastic cogwheels, chain wheels and chains and bolts
must be greased every 40 operating hours.
Beveling planer blades
Dull planer blades raise the risk of accidents, the work ef-
ficiency is no longer guaranteed.
Bevel the blade only up to 15 mm knife height. The blade
cutting angle should avarage 40 ± 2 degrees.
For regrinding, bring the blade to an authorised grinding
workshop, or ship it back to the manufacturer.
Installing planer blades Fig. 16
1 Adjusting screw
2 Pressure screw
3 Planer blades
4 V-ledge
5 Markings
6 Adjust gauge
Make sure during installation that
the risk of injury for fingers and hands is mounted.
•
the clamping surface in the cutter spindle and the V-
•
ledge are clean.
the beveled planer blades are deoiled.
•
only blades that have been beveled in a pair are in-
•
stalled.
the installation of the planer blades and the V-ledge
•
correspond to the illustration
close the planer blades and the V-ledge on both
•
sides.
all of the clamping screws are tightened (8,9 N/m).
•
Warning!
The details of blade fastening, blade protection length,
blade thickness, should be kept for a minimum during
warm up spin and optimally for the starting of the blade
attachment screw.
Planer blade adjustment, Fig. 17
To adjust, apply the provided adjustment gauges.
•
First, adjust one blade, then the other.
•
• Shift the blade on the adjusting screw, alternating sides,
till the cutting edge that lies over the work table touches
the adjustment gauges.
The right marking must align, corresponding to the il-
•
lustration, with the edge of the table panel.
During spinning the planer blade must be in sync with
•
the adjustment gauges as much as possible, optimally
to the second marking.
Left and right adjustment should be done following the
•
exterior of the blades.
Tighten the pressure screws of the V-ledge with a flat
•
wrench SW 8. (8,9 N/m)
Adjust and clamp the second blade in the same way.
•
Perform a test run after each blade change and then
•
retighten the pressure screws. (8,9 N/m)
The planer blade must be tested before use to make sure
that the above mentioned instructions have been fol-
lowed.
Please be attentive of all the safety warnings before turn-
ing the machine on.
Declaration of compliance
with EG-guidelines
Hereby we, the Scheppach Manufacture of Woodworking
Machines GmbH, Günzburger Str. 69, D-89335 Ichen hau-
sen, declare that the subsequent qualified machine by way
of its construction and design as well as commercial use
meets the corresponding regulations of the EG-guidelines
stated below. In case of a modification of the machine this
declaration is no longer valid.
Name of the machine:
Thicknessing and Planing machine
Type of machine
hms 2600ci, Art.-Nr. 7137 0901, 7137 0902
Relevant EC directives:
EC machine directive 98/37/EG (< 28.12.2009),
EC machine directive 2006/42/EG (> 29.12.2009),
EC Low voltage directive 2006/95/EWG,
EC-EMV directive 2004/108/EWG.
Applied
harmonized
European
standards:
EN 55014, EN 55104, EN 60555-2, EN 60204-1, EN 861, EN
847-1, EN 12100-2
Notified body:
Technical Committee on Wood, 70504 Stuttgart; Checking
and certifying body BG-Approval certificate
Enabled to:
EG-Baumusterprüfung, Zertifikatsnummer 041051
GS-Prüfung, Zertifikatsnummer 041052
BS-staubgeprüft, Zertifikatsnummer 041053
Place, Date:
Ichenhausen, 26. 09. 2005
Signature:
i.V. Wolfgang Windrich (product manager)
Содержание hms 2600ci
Страница 75: ...international 77 INTERNATIONAL...
Страница 76: ...78 international...
Страница 77: ...international 79...
Страница 78: ...80 international...
Страница 79: ...international 81...
Страница 80: ...82 international...
Страница 81: ...international 83...
Страница 82: ...84 international...
Страница 83: ...international 85 71370045 71370046 06 06 2008...
Страница 84: ...86 international 0RWRU EURZQ EOXH EODFN UHG ZKLWH EOXH EODFN 8 EOXH EODFN EURZQ 9 9 8 8 0RWRU JUH 9 9 8...
Страница 85: ...international 87...
Страница 86: ...88 international...
Страница 87: ...international 89...
Страница 88: ...90 international...