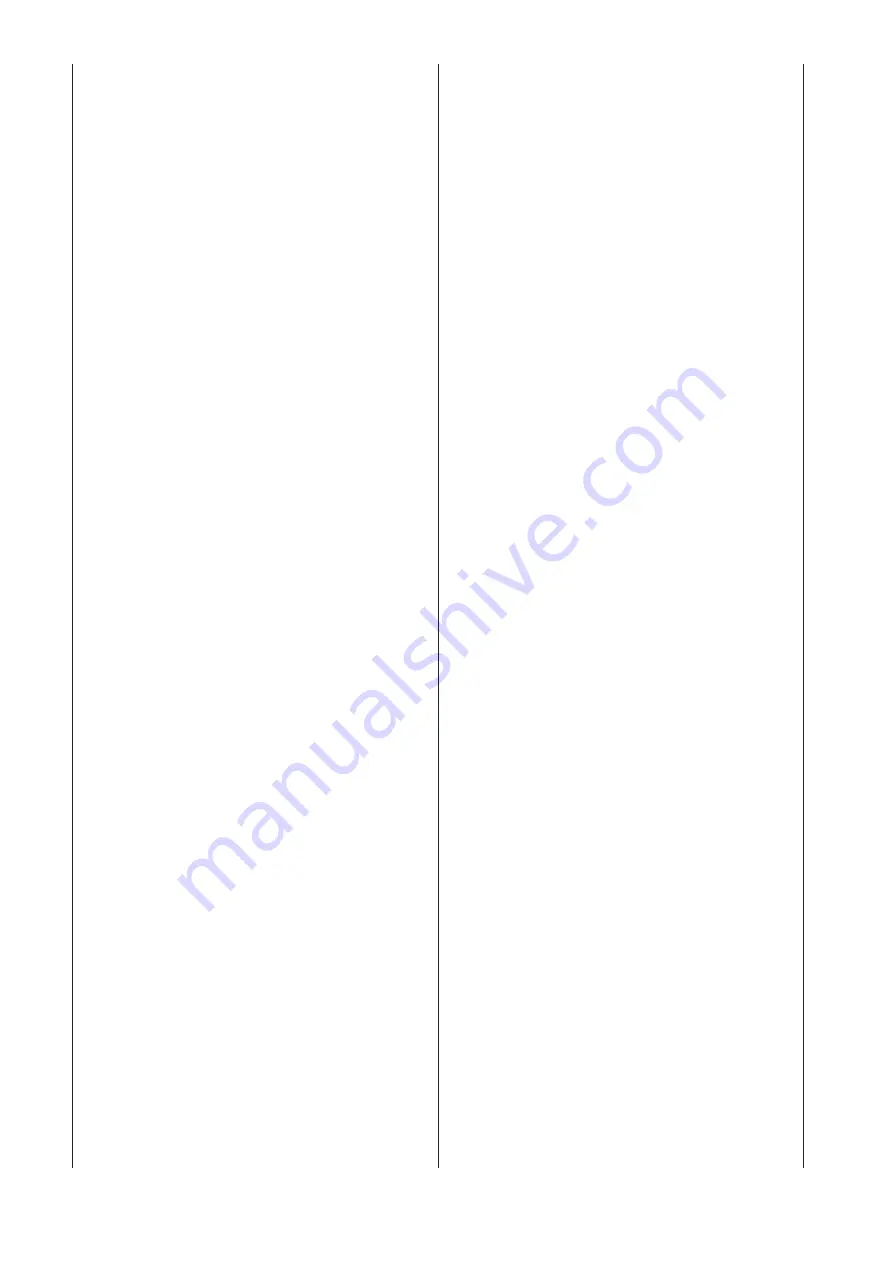
english 13
Disconnect the power plug!
Planer work – Chip removal, Fig. 6.1
The planer work chip removal is adjustable with the joint
lever 1 stepwise from 0 – 3 mm.
During work, the thicknessing table must be adjusted be-
tween 90 und 210 mm. Attention, otherwise the extraction
outlet will be clamped! Fig. 6.2
For longer work pieces (longer than the feeding or the re-
ceiving table) a roll rack (optional equipment) or similar
should be used.
Planer work – Planer shaft guard, Fig. 7
When dressing up to 75mm work piece strength, the plan-
er shaft guard must cover the work piece and the planer
shaft from above. If the work piece width is more than 75
mm, set the protective rails of the shaft guard to the width
of the work piece. Make sure to put closed hands, with
the thumb adjacent on the work piece.
1 Work stopper
2 Planer shaft guard
Joining, Fig. 8
Use the work stopper for this purpose, leave the planer
shaft protector on the table and set the protective rails to
the width of the work piece.
Push the work piece against the planer stopper and then
lead it over the planer shaft with both hands. As long as
the board reaches high enough on the receiving table, put
the left hand on it and shift it without interruption over the
blade shaft.
Planer work – Shavings emission, Fig. 9
While work, the work table must be locked.
The extraction tube should be connected to the extraction
hood.
When connected to the extraction unit can then be ex-
tracted.
Extraction connection caliber 100mm
Planer thicknessing – Machine adjustment, Fig. 10.1
Set the work table high and open it.
Adjust the height to the highest possible.
Set a high pivot and heighten (bolt).
Attach the extraction connections and tighten the knurled
screw.
When connected to the extraction unit can then be ex-
tracted.
Planer thicknessing – Table adjustment, Fig. 10.2
The height of the thicknessing table is adjustable by a
hand wheel.
The integrated position gauge indicates aperture height
from 5 to 210 mm.
One rotation of the hand wheel corresponds to 2 mm
Keep the thicknessing table and the work table free of
resin. Shaving thicknes max. 3 mm.
The graduation lines on the graduated collar make a fine
adjustment possible, whereby 1 graduation line corre-
sponds to 0, 05 mm.
V-belt tension motor, Fig. 11, 12, 12.1 + 12.2
Warning!
Re-tighten the flat belt and v-belt after the first 3 hours
•
of operation. Then check the belt tension and regularly
re-tighten, if necessary, after 40 operating hours.
Remove 4 hexagon sockets on both inner sides of the
•
encasing, Fig. 11.
Remove both side walls.
•
Losen clamping nut A on both sides (Fig. 13.1 +
•
13.2).
Push the motor seesaw down.
•
Tighten clamping nut A on both sides.
•
Attach the side walls.
•
V-belt feeder cylinders, Fig. 11, 12 + 13.3
Remove 4 hexagon sockets on both inner sides of the
•
encasing, Fig. 11 + 12.
Take off the sides.
•
Losen 4 hexagon nuts B, Fig. 13.3.
•
Adjust belt tension.
•
Tighten 4 hexagon nuts B.
•
Loosen the “C” screw, tighten the v-belt, then re-tight-
•
en the “C” screw
Attach the side walls.
•
Feeder cylinders adjustment, Fig. 14
To guarantee an efficient feeder the pressure springs must
be set to the adjacent dimensions.
Changing of the feeder- feeder cylinder, Fig. 15
The coating of feeder cylinders is from abrasion-resistant
rubber.
After long-term great operational demand they can suffer
from abrasion, which will lead to a change of feeder-feeder
cylinder.
1 Feeder cylinder
2 Support clip
3 Chain wheel
4 Spiral pivot
5 Pressure springs
6 Hexagon nut
Perform the change as follows
Remove 4 hexagon sockets on both inner sides, Fig.
•
11 + 12.
Take off the sides.
•
Take off feeder chain.
•
Remove feeder cylinder (1) with a hexagon nut (6).
•
Transfer the chain wheels to the new feeder cylinder.
•
Install the new feeder cylinders.
•
At the end, put the machine together again.
•
Work table safety
To prevent accidental closure of the work table, it is
equipped with a hinge shear.
When closing the table no special safety precautions need
to be taken.
Work table, Fig. 6.1
The planer work chip removal is adjustable with the joint
lever 1 in 0 – 3 mm steps.
The work table can get displaced during the time of use
and an accurate to dimensions shavings removal is no
longer possible. In this case, the hexagon screws need
retightening, so that the work table could perform the ac-
curate shavings removal on its own.
Содержание hms 2600ci
Страница 75: ...international 77 INTERNATIONAL...
Страница 76: ...78 international...
Страница 77: ...international 79...
Страница 78: ...80 international...
Страница 79: ...international 81...
Страница 80: ...82 international...
Страница 81: ...international 83...
Страница 82: ...84 international...
Страница 83: ...international 85 71370045 71370046 06 06 2008...
Страница 84: ...86 international 0RWRU EURZQ EOXH EODFN UHG ZKLWH EOXH EODFN 8 EOXH EODFN EURZQ 9 9 8 8 0RWRU JUH 9 9 8...
Страница 85: ...international 87...
Страница 86: ...88 international...
Страница 87: ...international 89...
Страница 88: ...90 international...