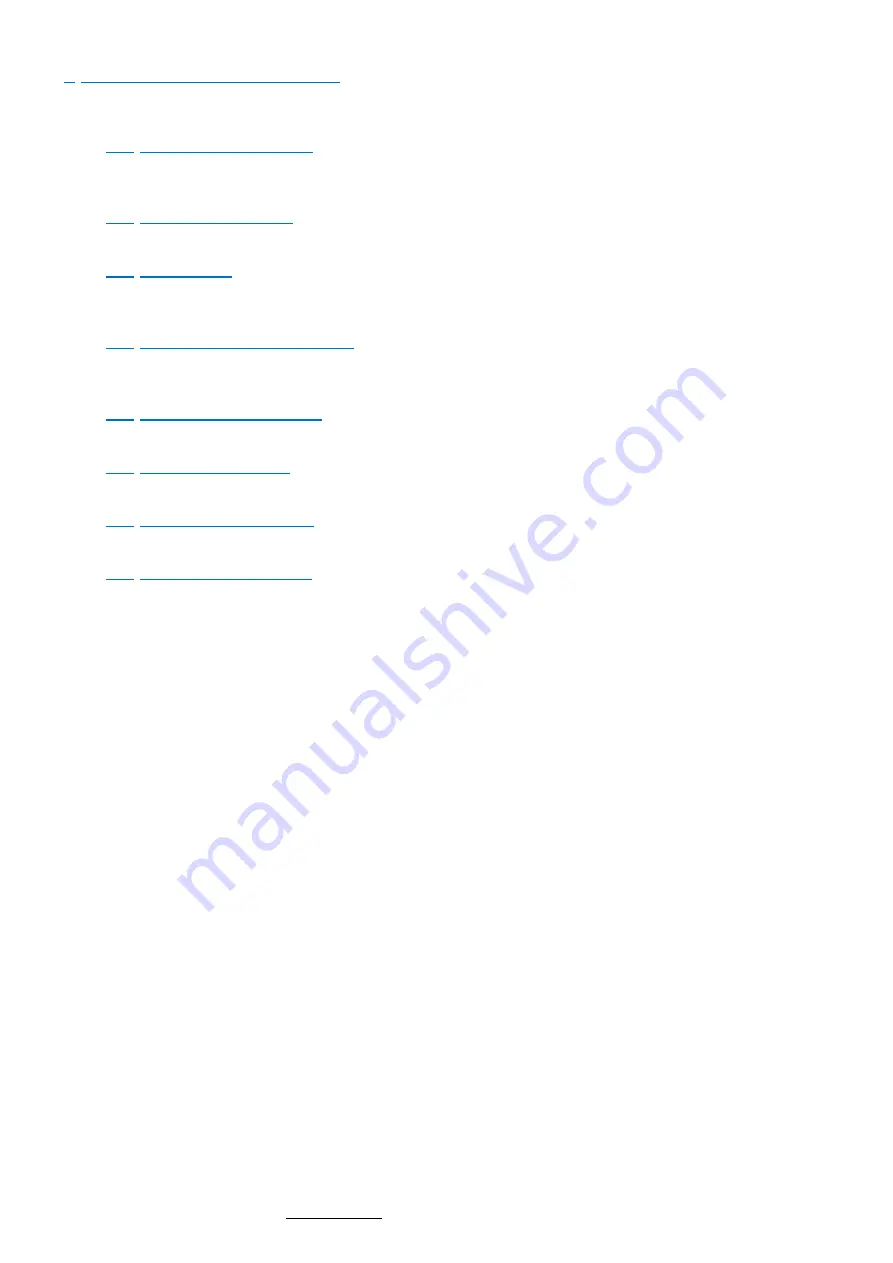
28
SCAIME Manual : NU-eNod4B-ETH-E-236708-D.docx
8
MEASUREMENT AND STATUS
The
eNod4
transmits measure after signal and data processing through different protocols available. The accessible variables
are:
8.1
Gross measurement
The
‘gross measurement’
stands for the digital value after measurement scaling. It is affected by all the
‘zero’
functions
(power-up zero, zero tracking and zero requests). Zero request value can be saved in non-volatile memory (option).
8.2
Net measurement
The
‘net measurement’
stands for the digital value after measurement scaling and tare subtraction.
8.3
Tare value
The
‘tare value’
stores the calibrated value that is subtracted from the
‘gross measurement’
so as to give the
‘net
measurement’
. This value can be saved in non-volatile memory (option).
8.4
Factory calibrated points
The
‘factory calibrated points”
contains the measurement value without the user calibration layer. It is directly linked to the
analog input voltage.
8.5
Logical IN/OUT level
The
‘logical IN/OUT level’
allows reading any time
eNod4
logical inputs and outputs level.
8.6
Preset Tare value
A previous calculated tare can be restored using this variable. This value can be saved in non-volatile memory (option).
8.7
Measurement status
The measurement status contains information on eNod4 measurement parameters.
8.8
Weighing diagnosis
8.8.1
Global weighing diagnosis
An internal alarm flag reflects the integrity of the whole measurement chain. It’s used to set logical output active or optional
analog output in an error mode in order to warn about any defection on the measurement chain (defective measurement).
This variable is set active when at least one of the followings conditions occurs:
-
sensor input control result out of tolerances
-
sensor input control command in progress
-
sensor input control command failed (timeout)
-
sensor input reference command in progress
-
gross meas. < (- max capacity)
-
gross meas. > (max capacity)
-
analog signal out of the A/D converter input range
-
EEPROM failure
This internal alarm flag is featured with adjustable specific de-bounced time and minimal activation time.
8.8.2
Sensor input control
eNod4
features a weighing diagnosis system allowing to check the integrity of analog sensor input by electrically simulating a
load, resulting to a simulated weight value. This diagnostic system can be used together with the others defects detection
systems in order to achieve overall integrity check of the measurement chain. This system involves two phases initiated by
the user:
-
The first, just after user calibration, allows taking a simulated reference weight value when the measuring chain
integrity is OK.
-
The second, when the user wants to check the integrity of the system, allows to make the difference between a new
simulated weight value and the reference. Then this difference can be compared with a dedicated maximum
tolerance value.