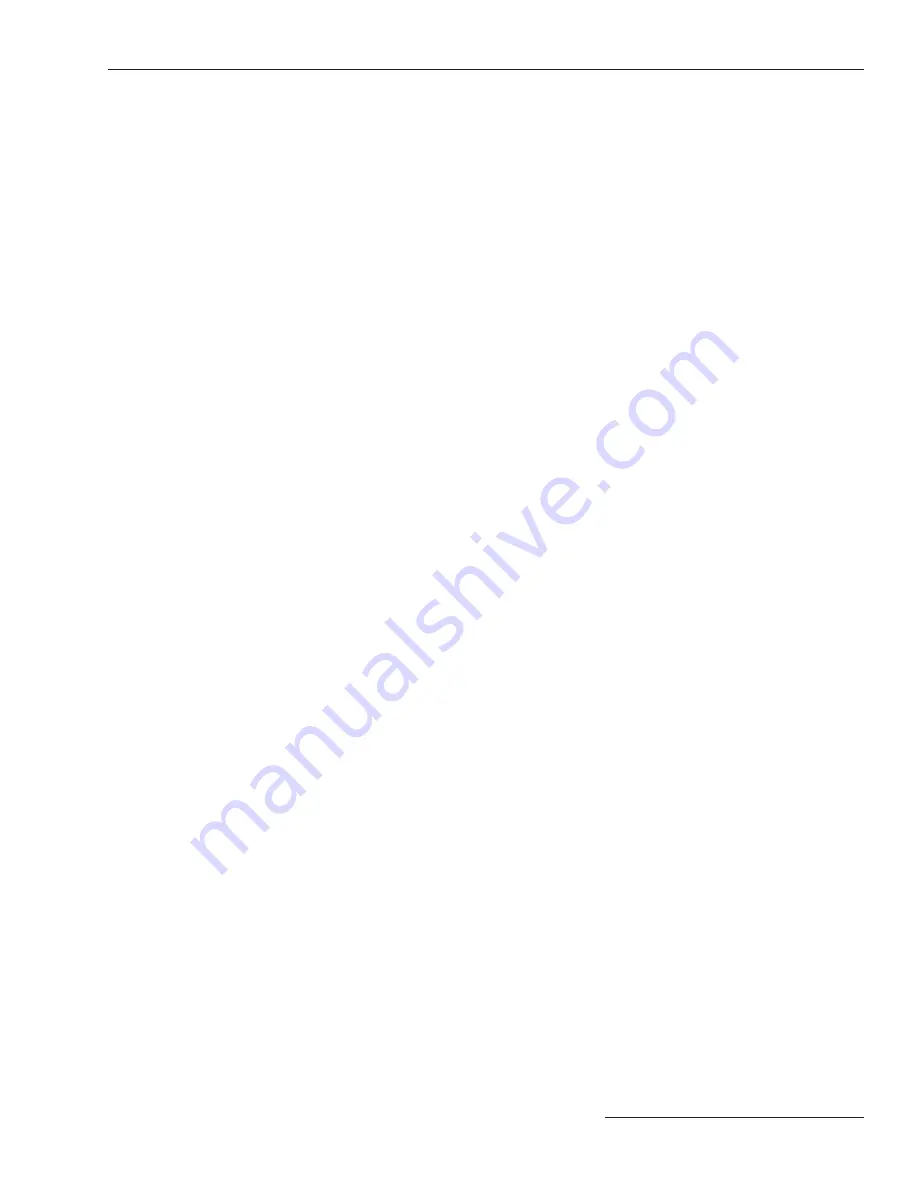
S&C Instruction Sheet 1041-540 17
Switch Control Operation
The switch control includes separate electronic paths to accommodate the different
requirements for peak versus normal operating current measurements. For normal
operating current measurements, full scale is 800 amps RMS. For peak measurements,
full scale varies with the switch type. For S&C switches, the value is approximately
4000 amps RMS and depends on the switch model. See Table 1 on page 18 for details.
Peak detection focuses on speed, with several samplings taken for each sinusoidal
peak and instantaneous analysis of the incoming data. Measurement of normal operating
current is slower and includes a finer degree of accuracy.
The switch control reports current, voltage, and phase-related data in units of amperes,
volts, and kvars. The rated accuracy of these measurements is based on the combined
accuracy of all the control components (exclusive of the sensor and sensor cable but
inclusive of all sensor conditioning components). The switch control uses the switch
calibration data and the phase angle offset values to correct all ac waveform data sampled
from the switch sensors.
Using the jumpers that come with the switch control, users can configure it in the field
for wye or delta distribution line applications. Based on the selected configuration and
certain setpoint values, the control normalizes voltages to nominal 120- or 240-Vac values.
Signal Processing
The switch control uses RMS detectors (with accuracy to the 100th 60 Hz harmonic) to
produce true RMS amplitude data for current, neutral current, and voltage waveforms.
This is particularly important when measuring neutral current because the effects of
harmonic distortion of any single phase are multiplied in the summing of the phases.
Because there is some response latency associated with this circuitry, voltage and
current changes that occur within a few tenths of a second are sensed as a single, steady
value.
For real-time, steady state monitoring and data logging, the switch control collects
data at 0.2-second intervals. It then averages eight samples and reports the “1.6-second
averaged” value. This results in a net response time of 1.6 seconds.
The switch control uses these “1.6-second averaged” values for the real-time display,
reporting via SCADA communication, and data logging. Daily high and low values are
kept for the current day and the preceding 7 days.
Waveform Analysis for Power System with Delta-Connected Customer
Transformers
The switch control treats power systems with delta-connected customer transformers
as a special case.
When the line switch has three voltage sensors and the Sensor Conditioning module
is configured with a “delta” jumper, the switch control reproduces the delta voltage wave-
form before any transducer functions are performed. This is useful for comparing the
measured voltage against that seen by customers served by phase-to-phase connected
transformers. For S&C voltage sensors, this configuration is necessary for accurate
phase-to-phase voltage measurements because these sensors measure phase-to-neutral
voltages even in a delta distribution system.
For switches with one voltage transformer for voltage sensing and control power and
three CVMI current sensors, the Sensor Conditioning module must always be configured
with a “wye” jumper. Voltage sensing and reporting are determined by the way the voltage
transformer is connected: phase to phase (delta) or phase to neutral (wye).
RMS Ac Waveform
Analysis
This section explains how the switch control components work together to detect and
respond to “faults” and voltage outages.