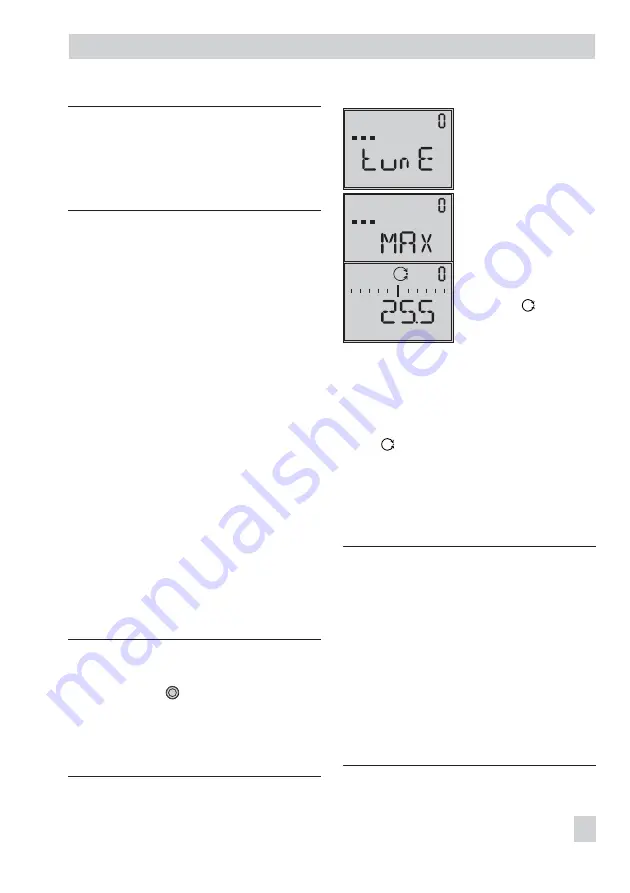
NOTICE
If the positioner is mounted onto another ac-
tuator or its mounting position is changed,
reset the positioner to its default settings be-
fore re-initializing it. Refer to section 7.8.
During initialization the positioner adapts it-
self optimally to the friction conditions and
the signal pressure requirements of the con-
trol valve.
The type and extent of self-adaptation de-
pends on the initialization mode selected:
4
MAX
maximum range
(standard range)
Initialization mode for simple start-up of
valves with two clearly defined mechani-
cal end positions, e.g. three-way valves
(see section 7.5.1)
4
NOM
nominal range
Initialization mode for all globe valves
(see section 7.5.2)
4
MAN
manually selected range
Initialization mode for globe valves with
an unknown nominal range (see section
7.5.3)
4
SUB
substitute calibration
(emergency
mode)
This mode allows a positioner to be re-
placed while the plant is running, with
the least amount of disruption to the
plant (see section 7.5.4)
Note:
The initialization procedure can be in-
terrupted while running by pressing the ro-
tary pushbutton (
).
StOP
appears three
seconds long and the positioner then
changes to the fail-safe position (SAFE). The
fail-safe position can be canceled again
over Code
0
(see section 8.2.2).
Alternating displays:
Initialization running
Initialization progress
indicated
(MAX, NOM, MAN or SUB
appears, depending on the
initialization mode selected)
Initialization successful
Positioner in
automatic
mode
The time required for an initialization pro-
cess depends on the stroking speed of the
actuator and may take several minutes.
After a successful initialization, the
positioner runs in automatic mode indicated
by the
closed-loop control icon.
A malfunctioning leads to the process being
interrupted. The initialization error appears
on the display according to how it has been
classified by the condensed state. See sec-
tion 8.3 on page 60).
Note:
The setting of Code
48 - h0
= YES
starts the plotting of the reference graphs re-
quired for valve diagnostics (drive signal
steady-state d1 and hysteresis d2) after ini-
tialization.
tESt
and
d1
and
d2
appear on
the display in an alternating sequence.
An unsuccessful plotting of the reference
graphs is indicated on the display by Code
48 - h1
and Code
81
(see error code list).
The positioner still works properly, even
though the reference graph plotting has not
been completed successfully.
EB 8387-3S EN
51
Start-up – Settings
%
Содержание TROVIS SAFE 3731-3
Страница 5: ...EB 8387 3S EN 5...
Страница 92: ...92 EB 8387 3S EN...
Страница 93: ...EB 8387 3S EN 93...
Страница 94: ...94 EB 8387 3S EN...
Страница 95: ...EB 8387 3S EN 95...
Страница 96: ...96 EB 8387 3S EN...
Страница 97: ...EB 8387 3S EN 97...
Страница 98: ...98 EB 8387 3S EN...
Страница 101: ...EB 8387 3S EN 101...
Страница 102: ...102 EB 8387 3S EN...
Страница 103: ...EB 8387 3S EN 103...