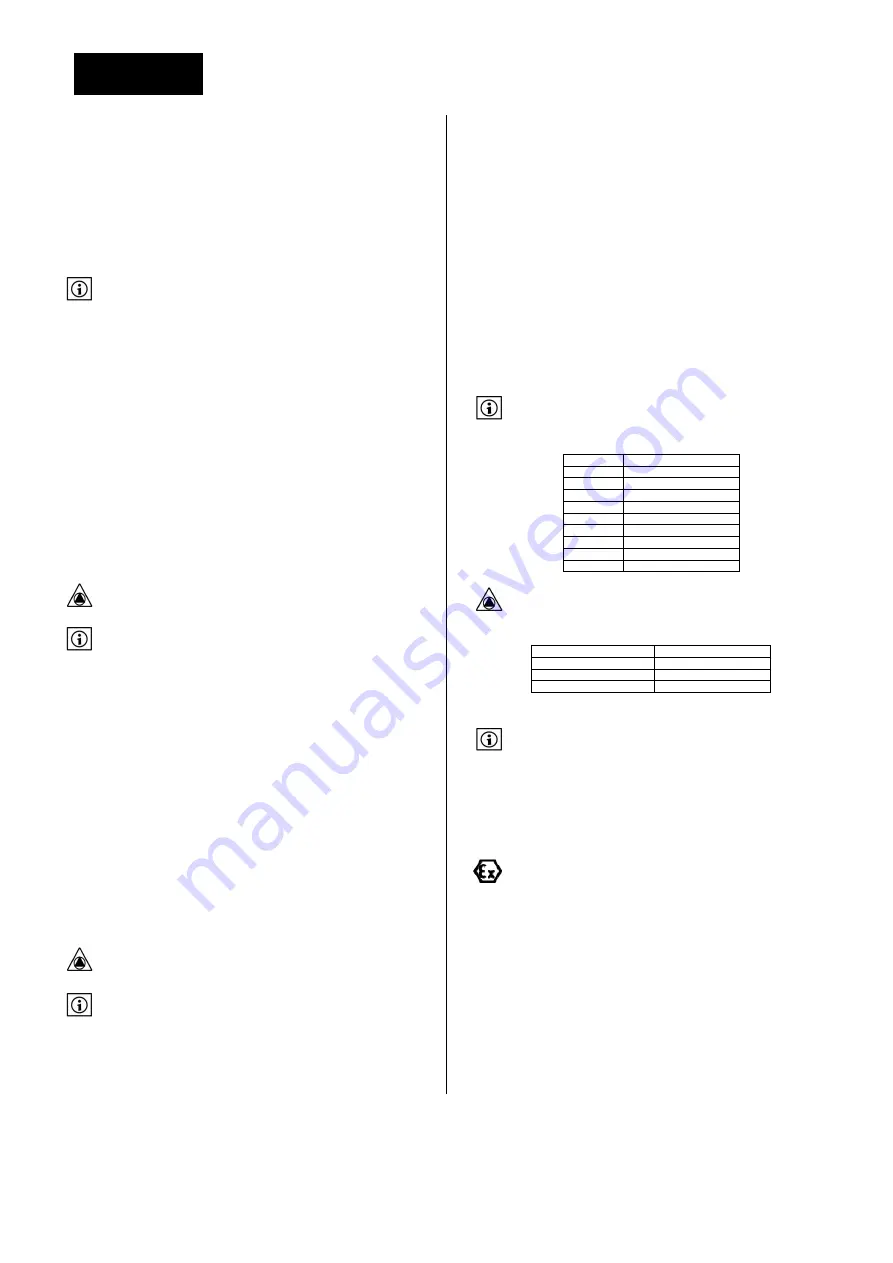
ENGLISH
16
2.
Remove
nuts
92.00
and
slide
out
the
back
pull
out
unit
from
the
casing
10.20.
Use
jack
screw
90.80
to
ease
disassembly.
Remove
gasket
40.00.
3.
Loosen
impeller
nut
92.20
and
helicoil
93.00.
4.
Slide
out
impeller
23.00
and
its
flat
gaskets
40.02
and
40.01.
5.
Loosen
screws
91.42
and
remove
wear
ring
54.20
from
casing
cover
16.10.
6.
Remove
key
94.01
and
slide
out
shaft
sleeve
52.30
with
mechanical
seal
43.30
from
shaft
21.10.
Remove
key
94.02.
Mark
position
of
mechanical
seal
before
dismantling.
7.
Remove
nuts
92.01
and
casing
cover
16.10.
8.
Remove
nuts
90.23,
take
away
cover
47.10
and
mechanical
seal
housing
48.70.
Change
gasket
40.05
for
a
new
one.
9.
Remove
screws
91.44
and
cover
36.00
on
motor
side
with
its
gasket
40.03.
10.
Slide
out
thrower
50.70
from
the
shaft.
11.
Withdraw
shaft
21.10
with
ball
bearings
32.11
and
32.20
with
care
from
bearing
bracket
housing
33.00.
12.
Remove
screws
91.43
and
cover
36.01
with
its
gasket
40.04.
13.
Remove
circlip
93.01,
loosen
shaft
nut
92.10
and
remove
lock
washer
93.01.
Extract
ball
bearing
32.11
and
32.20
from
the
shaft.
14.
Loosen
screw
90.11,
remove
washer
93.02,
and
foot
18.30.
15.
Dismantle
if
required
(worn
or
damaged
part)
the
lip
seals
42.30
and
42.31
from
covers
36.00
and
36.01.
9.3.2
RE
‐
ASSEMBLY
Refer
to
tightening
torques
table
for
screws
and
bolts.
Before
starting
assembly
of
the
pump
see
sectional
drawings
of
the
pump.
Respect
screws
and
bolts
tightening
torques.
1.
Install
ball
bearings
32.11
and
32.20,
the
circlips
93.01
onto
the
shaft
21.10.
Screw
nut
92.01.
When
installing
new
ball
bearing
on
the
shaft,
heat
them
up
to
80°C
to
ease
assembly.
2.
Press
lip
seals
in
bearing
covers
36.00
and
36.01.
Use
news
seals
if
necessary.
3.
Install
bearing
cover
36.01
on
pump
side
with
its
flat
gasket
40.04
and
screws
91.43.
4.
Fasten
foot
18.30
using
washer
93.02
and
screw
90.11.
Slide
shaft
assembly
inside
the
ball
bearing
housing
33.00.
5.
Install
ball
bearing
cover
with
the
flat
gasket
40.03
and
the
thrower
50.70.
6.
Install
cover
47.10
and
mechanical
seal
stationary
seat
48.70,
the
new
gasket
40.05
in
the
casing
cover
16.10
and
fasten
it
with
screws
90.23.
7.
Assemble
casing
cover
16.10
and
bearing
bracket
assembly
with
screws
90.21.
8.
Press
the
key
94.02
into
the
shaft
and
install
mechanical
seal
rotating
part
43.30
onto
shaft
sleeve.
Press
the
key
94.01
in
the
shaft
21.10.
Make
sure
that
seals
and
friction
faces
are
not
damaged
during
assembly
(scrubs
on
the
sleeve,
dirt,
…).
It
is
recommended
to
add
light
oil
on
the
shaft
to
ease
assembly.
9.
Install
wear
ring
54.20
and
screws
91.42.
10.
Install
impeller
23.00.
11.
Install
the
complete
back
‐
pull
‐
out
assembly
into
the
casing
with
the
casing
seal
40.00
between.
9.3.3
MOTOR
In
order
to
ensure
an
optimum
lifetime
of
the
integrated
motor
a
minimum
maintenance
is
necessary
:
clean
cooling
fins
regularly,
check
coupling
alignment
(if
any),
check
cable
gland
tightening,
…
Ball
bearing
lifetime
depends
on
axial
and
radial
forces
applied
on
motor
shaft
therefore
on
the
pump
design
(close
‐
coupled
pump,
pump
sets
with
elastic
coupling,
…).
Motor
can
be
fitted
with
lifetime
lubricated
ball
bearings
(identified
ZZ
or
2Z)
or
greased.
Greasing
nipples
are
located
at
the
ball
bearings
and
re
‐
greasing
quantities
are
indicated
on
motor
nameplate.
See
motor
instructions
manual
to
find
data
about
maintenance
work
to
be
performed.
9.4
TIGHTENING
TORQUES
Tightening
torques
depend
on
the
material
used
in
the
assembly
and
on
the
type
of
lubricant
that
is
used.
Refer
to
applicable
regulation
to
know
the
tightening
torques
for
the
fastening
of
cast
iron
or
stainless
steel
made
flanges.
The
values
given
below
should
be
only
indicative.
If
real
tightening
torques
are
required
please
ask
our
technical
services.
Threads
Tightening
torques
M6
8,5
Nm
M8
12
Nm
M10
25
Nm
M12
40
Nm
M16
90
Nm
M20
175
Nm
M24
300
Nm
M30
500
Nm
M36
700
Nm
Stainless
steel
bolts
:
apply
anti
‐
fretting
paste
before
assembly.
Tightening
torque
for
impeller
nut
item
92.20
:
Bearing
bracket
size
Tightening
torque
55
405
Nm
65
490
Nm
75
580
Nm
9.5
TOOLS
REQUIRED
A
typical
range
of
tools
that
are
required
for
pump
maintenance
is
listed
below.
Those
tools
are
standard
one
and
should
be
available
in
every
industrial
maintenance
Dpt.
•
Wrenches
to
suit
up
to
M48
nuts,
•
Socket
spanner
up
to
M
48,
•
Allen
keys
up
to
10
mm,
•
Range
of
screwdrivers,
•
Soft
mallet.
If
maintenance
work
must
be
performed
in
an
ATEX
classified
area
then
make
sure
that
use
of
all
necessary
tools
are
authorized
in
the
area.
More
specialized
equipment
:
•
Bearing
pullers,
•
Bearing
induction
heater
for
ball
bearing
assembly,
•
Coupling
grip
spanner.
Additional
equipments
used
for
coupling
alignment
:
•
Calipers,
•
Crowbar,
•
Straightedge,
•
Shims,
•
Sledgehammer.
Содержание NOEH
Страница 2: ......
Страница 3: ...NOEH INSTALLATION ET MISE EN SERVICE FRAN AIS N M S n 4095567 Ed 3 10 13...
Страница 4: ...2...
Страница 22: ...FRAN AIS 20 12 1 1 PLAN EN COUPE HYDRAULIQUE SIMPLE VOLUTE HYDRAULIQUE DOUBLE VOLUTE 12 1 2 NOMENCLATURE...
Страница 24: ...FRAN AIS 22 13 DECLARATION CE...
Страница 25: ......
Страница 26: ...NOEH INSTALLATION AND OPERATING INSTRUCTIONS ENGLISH N M S n 4095567 Ed 3 10 13...
Страница 27: ...2...
Страница 44: ...ENGLISH 19 12 1 1 SECTIONAL DRAWING SINGLE VOLUTE CASING DOUBLE VOLUTE CASING...
Страница 46: ...ENGLISH 21 13 EC DECLARATION OF CONFORMITY...
Страница 47: ......