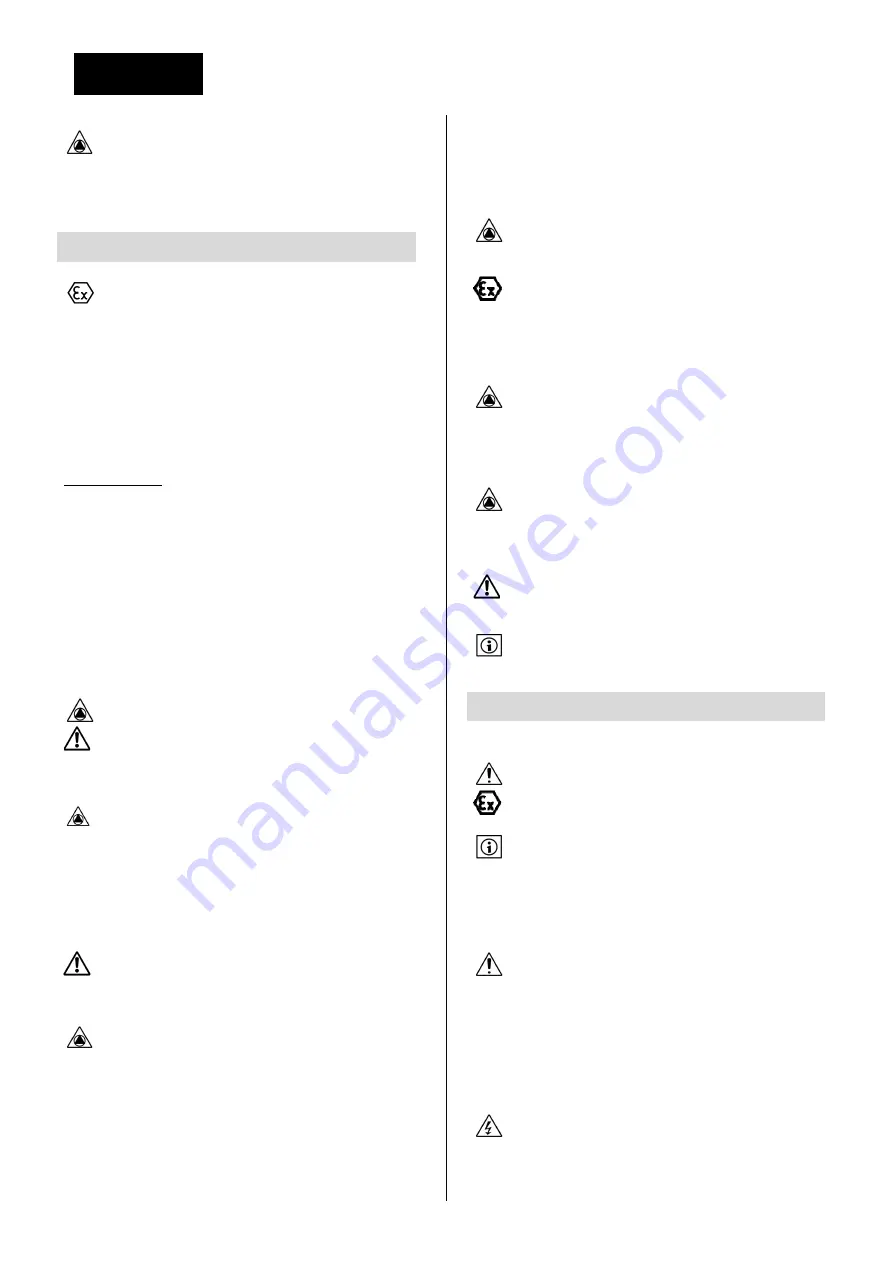
ENGLISH
14
The
harmonic
currents
that
are
created
by
the
VSD
pass
through
motor
ball
bearings.
Standard
ball
bearings
can
be
used
up
to
55KW.
For
higher
installed
power
(see
engraved
power
on
motor
name
plate),
the
motor
should
be
equipped
with
isolated
ball
bearings
(specific
ball
bearing)
or
with
isolated
bearing
housing
(and
standard
ball
bearing).
8
START
‐
UP
8.1
PRE
‐
COMMISSIONING
If
the
pump
is
installed
in
a
potentially
explosive
atmosphere
or
when
dangerous
or
polluting
fluids
are
pumped,
it
is
advised
(Zone
2)
or
requested
(zone
1)
to
install
additional
protection
devices.
Check
following
points
:
Pump
flow
is
always
higher
than
authorized
continuous
minimum
flow,
Pump
never
runs
dry,
Normal
leakage
of
the
shaft
seal
is
controlled,
Surface
temperature
bearings
housings
is
lower
than
the
maximum
admissible
surface
temperature
in
selected
ATEX
zone,
Pressure
on
discharge
side
of
the
pump
is
lower
than
pump
maximum
allowable
working
pressure.
Set
alarm
and
stop
trips
of
sensors.
In
every
cases
check
:
Quality
of
electrical
connections,
Protection
devices
are
installed,
Auxiliary
piping
are
connected,
Flanges
connections,
Suction
line
and
pump
casing
are
filled
with
fluid,
Motor
direction
of
rotation
is
correct,
Coupling
alignment
is
correct,
Oil
level
was
checked
and
greasing
of
ball
bearings
has
been
done,
Coupling
guard
is
installed.
8.2
FILLING
/
VENTING
Before
the
very
first
start
‐
up,
pump
casing
and
suction
line
must
be
filled
with
fluid
(depending
on
piping
system
a
vacuum
pump
may
have
to
be
used).
Pump
casing
should
be
perfectly
vented
to
avoid
that
the
mechanical
seal
runs
dry.
Take
precautionary
measures
when
manipulating
dangerous,
hot
or
polluting
fluids.
Wearing
individual
protective
devices
is
necessary.
The
operator
must
know
the
potential
hazards.
8.3
START
‐
UP
If
a
barrier
fluid,
flushing
fluid,
cooling
fluid
or
a
heating
fluid
is
used,
check
that
auxiliary
systems
are
activated
and
working
correctly
before
pump
start
‐
up.
Close
isolating
valve
on
pump
discharge
side.
Open
all
valves
in
suction
line.
Proceed
to
pump
priming
(if
not
already
done).
Pump
casing
and
suction
pipe
should
be
completely
filled
with
fluid.
Turn
the
pump
on
and
check
discharge
pressure
increase.
Compare
this
pressure
to
the
shutoff
pressure
available
on
the
hydraulic
curve
In
order
to
avoid
an
important
overheating
of
the
liquid
inside
the
pump
the
pump
should
not
work
more
than
20
to
30
seconds
against
a
closed
discharge
valve.
If
expected
pressure
is
reached
then
progressively
open
the
discharge
valve.
If
there
is
no
liquid
delivered
or
if
discharge
pressure
is
too
low
then
see
chapter
“trouble
shooting”.
8.4
RUNNING
CHECKS
During
operation
of
pump
in
duty
conditions
(capacity,
head,
temperature,
…)
the
following
points
must
be
checked
:
Check
and
note
pump
duty
point.
If
necessary
convert
pressure
value
from
bar
indicated
on
the
pressure
gauge
to
mwc
:
HMT
mce
=
(P
bar
x
100)
/
(SG
x
9,806)
with
SG=
fluid
Specific
Gravity.
Check
and
note
current
consumption
on
each
phase
of
the
motor.
Check
calibration
of
motor
protections.
Check
temperature
of
ball
bearings
(on
bearing
housing
surface).
Check
flexible
coupling
alignment
after
several
pump
starts
(only
for
concerned
pumps
variants).
Check
tightening
of
flanges
fastening
bolts.
Check
there
is
no
leakage
and
no
abnormal
running
noise.
When
pumping
hot
fluids,
the
definitive
coupling
alignment
should
be
done
only
when
system
nominal
temperature
is
reached
and
stabilized.
See
chapter
7.1.4
COUPLING
ALIGNMENT
Check
the
surface
temperature
on
the
bearing
bracket
and
on
the
pump
casing.
Check
pumped
fluid
temperature.
Alarm
and
stop
trips
settings
should
be
done
according
those
values.
Refer
to
specific
sensors
IOM
before
adjusting
those
trips.
8.5
SHUTDOWN
Before
the
pump
is
stopped
close
the
discharge
isolating
valve.
Ensure
that
the
pump
runs
in
that
condition
no
more
than
few
seconds.
When
the
pump
has
come
to
a
standstill
:
close
the
suction
isolating
valve.
If
the
pump
is
equipped
with
auxiliary
systems
such
as
a
quench,
heating
system,
flushing,
external
lubrication,
etc
…
it
must
be
closed
at
the
last
step.
If
temperature
is
likely
to
drop
below
freezing
point,
pump
casing
and
auxiliary
connected
systems
should
be
completely
drained
or
otherwise
protected.
For
prolonged
shut
‐
downs
an
adapted
rust
protective
coating
should
be
applied
to
the
inside
and
outside
of
the
pump.
Pumping
explosive,
toxic
or
polluting
fluids
:
make
sure
that
all
necessary
actions
were
taken
to
avoid
the
creation
of
a
hazard
for
people
or
environment
during
drainage
operations.
Products
which
are
sent
back
to
Salmson
must
be
drained
and
cleaned.
Pumped
fluid
should
be
completely
removed
from
the
pump.
9
MAINTENANCE
9.1
GENERAL
INFORMATION
Only
properly
trained
and
skilled
staff
should
undertake
maintenance
operations.
Only
authorized
personnel
should
undertake
maintenance
on
ATEX
certified
equipments.
Make
sure
to
avoid
creation
of
explosion
hazard
while
proceeding
to
maintenance
in
a
ATEX
zone.
All
technical
documents
delivered
with
the
pump
should
be
known
and
should
be
available
near
the
pump.
The
maintenance
crew
should
be
informed
about
the
risks
linked
to
the
use
of
the
pump
and
to
the
pumped
fluids
before
they
can
start
working
on
the
equipment
(dangerous
products,
fluid
and
pump
temperature,
pressurized
parts,
…).
They
should
be
equipped
with
all
appropriated
individual
safety
protections
(glasses,
gloves,
…)
and
should
respect
local
industrial
and
security
rules.
Pump
contains
a
part
of
pumped
fluid
even
when
it
is
at
a
standstill.
Drain
and
flush
pump
casing
with
care
before
starting
pump
disassembly.
Appropriate
lifting
devices
should
be
available
to
help
personnel
moving
heavy
loads.
The
maintenance
area
must
be
clearly
identified.
Install
warning
boards
with
the
words
«
WARNING
:
machine
under
repair
!
»
on
the
pump
and
on
the
control
cabinet.
Any
work
on
the
machine
must
be
performed
when
pump
is
stopped.
Prior
to
any
maintenance
or
repair
work
the
motor
should
be
electrically
isolated
and
secured
against
uncontrolled
start.
Lock
the
main
switch
open
and
disconnect
circuit
breaker.
Withdraw
the
fuses
if
any.
Содержание NOEH
Страница 2: ......
Страница 3: ...NOEH INSTALLATION ET MISE EN SERVICE FRAN AIS N M S n 4095567 Ed 3 10 13...
Страница 4: ...2...
Страница 22: ...FRAN AIS 20 12 1 1 PLAN EN COUPE HYDRAULIQUE SIMPLE VOLUTE HYDRAULIQUE DOUBLE VOLUTE 12 1 2 NOMENCLATURE...
Страница 24: ...FRAN AIS 22 13 DECLARATION CE...
Страница 25: ......
Страница 26: ...NOEH INSTALLATION AND OPERATING INSTRUCTIONS ENGLISH N M S n 4095567 Ed 3 10 13...
Страница 27: ...2...
Страница 44: ...ENGLISH 19 12 1 1 SECTIONAL DRAWING SINGLE VOLUTE CASING DOUBLE VOLUTE CASING...
Страница 46: ...ENGLISH 21 13 EC DECLARATION OF CONFORMITY...
Страница 47: ......