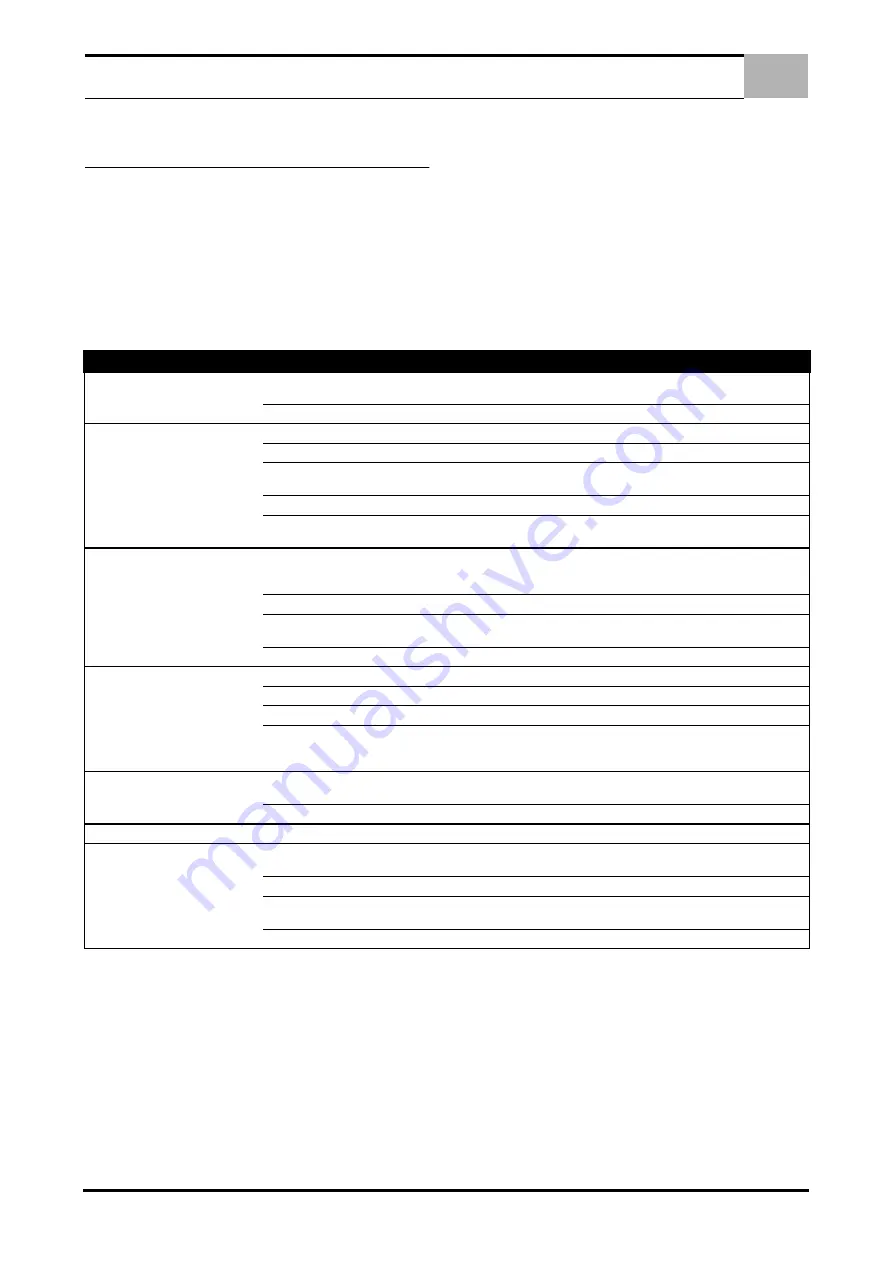
8 EN
GENERAL MAINTENANCE
EN
9.0
GENERAL MAINTENANCE
DISCONNECT THE POWER SOURCE FROM THE MAINS BE-
FORE PERFORMING ANY MAINTENANCE WORK.
Every 5-6 months, remove accumulated dust from the inside of
the welding unit with a jet of dry compressed air (after removing
side panels).
BE EXTREMELY CAREFUL TO AVOID BENDING MOVE-
MENTS, WHICH COULD DAMAGE AND CHOKE THE TORCH.
NEVER MOVE THE POWER SOURCE BY PULLING THE
TORCH.
PERIODICALLY CHECK THE CONDITION OF THE TORCH,
WHICH IS THE PART MOST SUBJECT TO WEAR.
9.1
TORCH MAINTENANCE:
1.
GAS NOZZLE:
periodically apply welding spray and clean
nozzle interior of residue.
2.
WIRE GUIDE TUBE:
check the wire passage of the tube for
wear. Replace as necessary.
9.2
CONNECTING THE TORCH
Before connecting the torch to the machine, make sure that the di-
ameter of the wire liner, the groove of the motor-rolls and the con-
tact tip corresponds to the wire used.
Ensure that the wire guide hose doesn’t touch the roll.
TYPE OF BREAKDOWN
POSSIBLE CAUSES
CHECKS AND REMEDIES
No functions operate.
Faulty power cord (one or more phases
disconnected).
Check and remedy.
Blown fuse.
Renew.
Irregular wire feed.
Insufficient spring pressure.
Try tightening regulating knob.
Wire-guide sheath blocked.
Renew.
Wrong race - unsuitable for wire, or exces-
sively worn.
Turn roller over or change it.
Braking on coil excessive.
Loosen brake using adjusting screw.
Oxidized, poorly wound,poor quality wire,
with tangled or overlapping coils, etc.
Remedy by removing defective coils. If problem persists, change the wire
reel.
Reduced welding power.
Earth cable not connected.
Check that the power cord is in good condition and make sure that the
ground clamps are flrmly fixed to the works piece, which must be free of
rust, grease and paint.
Detached or loose connection on switches Check, tighten or renew, as necessary.
Faulty contactor
Check the state of the contacts and the mechanical efficiency of the con-
tactor
Faulty rectifier.
Visually check for signs of burn-out; if present, renew rectifler.
Porous or spongy welds.
No gas.
Check presence of gas and gas supply pressure.
Draughts in welding area.
Use a suitable screen. Increase gas delivery pressure if necessary.
Ciogged holes in diffuser.
Clear clogged holes using compressed air.
Gas leakage due to rupture in supply hos-
es.
Solenoid valve blocked.
Check and renew faulty component.
Check solenoid operation an electrical connection.
Porous or spongy welds.
Faulty pressure regulator.
Check operation by removing the hose connecting the pressure regulator
to the power source.
Poor quality gas or wire.
Gas must be extra-dry; change the cylinder or use a different type wire.
Gas supply does not switch off.
Worn or dirty solenoid valve.
Dismantle solenoid; clean hole and obturator.
Presslng torch trigger produces no
result.
Faulty torch trigger, disconnected or bro-
ken control cables.
Remove the torch connection plug and short-circuit the poles; if the ma-
chine operates properly, check the cables and the torch trigger.
Blown fuse.
Renew using a fuse of the same rating.
Faulty power switch.
Clean with compressed air. Ensure that wires are tightly secured; renew
switch if necessary.
Faulty electronic circuit.
Renew circuit.
Содержание FILCORD 353C
Страница 58: ...7 EL EL 9 0 5 6 9 1 1 2 9 2 23 47 47 2...
Страница 65: ...7 RU RU 9 0 5 6 9 1 1 2 9 2...