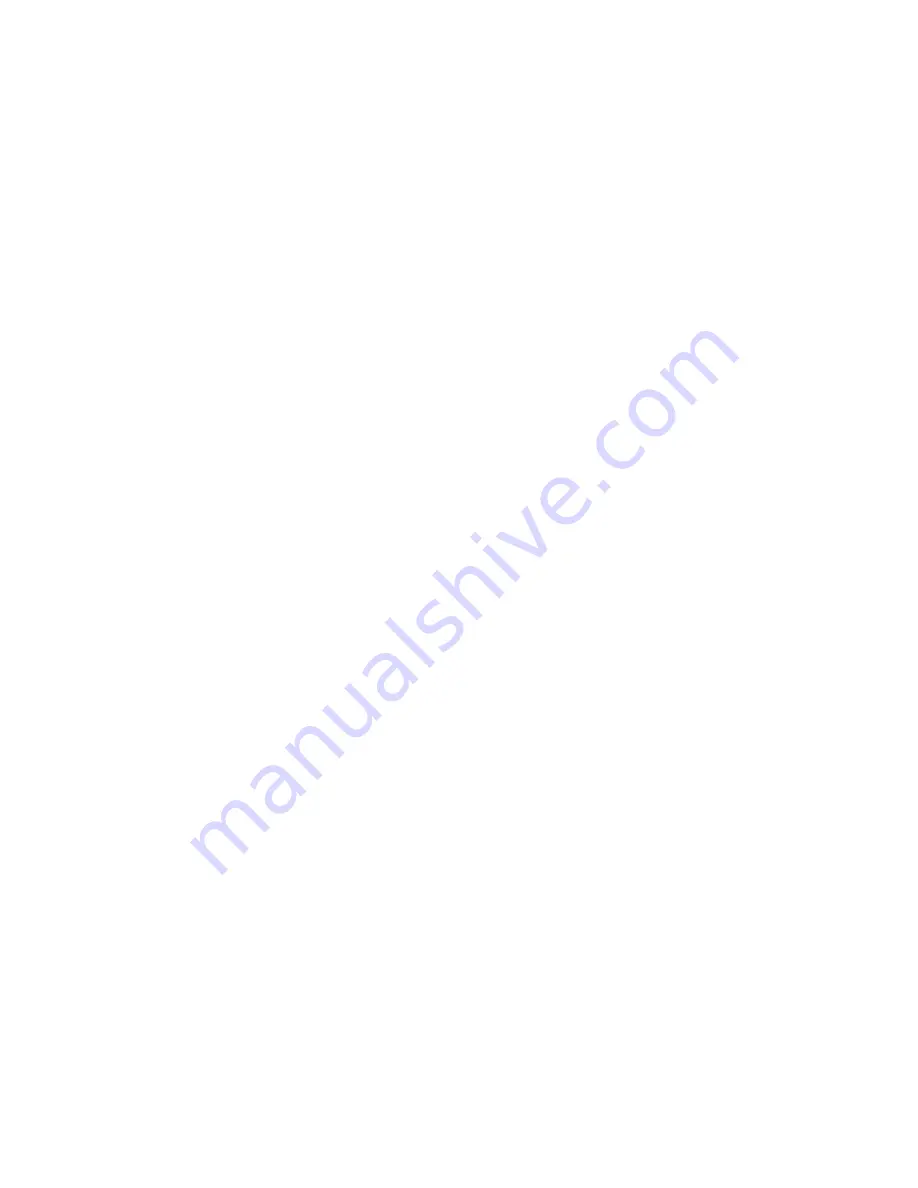
32
7. Keys don’t always work in the lock when gauged off the bottom shoulder stop. This is a
common problem caused by the key blank manufacturers. In recent years many of the key
blank manufacturers have stopped paying attention to the bottom shoulder stop on most keys
blanks since they are seldom used by the lock cylinder. We’ve seen Schlage C key blanks
with variations of up to 15 thousandths of an inch (.015”) between top and bottom shoulder
positions – between keys taken from the same box. It happens more often than you think.
The solution? Don’t bottom shoulder gauge your keys anymore.
Cutter Stalls Out
There are six possible causes for this problem.
1. You are cutting keys from Tip-to-Bow. This one can fool you if you’re not careful. Cutting
keys from tip to bow will work when you cut only shallow keys—sometimes a shop can cut
keys all day long and never hit upon a key with a deep cut. You think everything is O.K.
when all of a sudden your cutter stops dead halfway along the key. The problem? The deep
cut put the cutter into the key past the cutter tooth area on the left side of the cutter—you just
reinvented the disk brake!
SOLUTION—ALWAYS CUT FROM BOW-TO-TIP.
2. Oil on the belt and pulleys. Clean the pulleys with safety solvent and install a new drive belt.
3. Left-hand nut securing the cutter wheel isn’t tight.
4. Belt tension needs to be increase and/or replaced the drive belt.
5. You’re in your service vehicle. You’re Redi-Line generator needs repair, or your wiring
needs replacing (usually from the battery to the Redi-Line), or your battery is weak. Another
possibility is that you’ve been using a power converter and it is marginal.
6. Your cutter wheel is really dull.
Stylus Shaves Material Off Key
The situation is caused by the fact that the cutter wheel is made to a sharp point and therefore to
cut keys accurately the stylus must also be made with a sharp edge. A key blank dragged across a
sharp edged stylus has no choice but to scrape material from the key blank. The solution is to
lightly “blunt” the sharp edge of the stylus. This has to be done carefully because if the edge of
the stylus is blunted to much you will narrow the width of the pin seat somewhere in the middle—
if the stylus is sharp it will scrape the key to much, if the stylus is blunted to much it will produce a
duplicate key with a slightly narrower pin seat area.
If you’re going to cut more than 5 or 10 duplicates off one key we recommend that you make “first”
generation keys and then make additional duplicates off of them. For example if you had to make 50
duplicates off the same key you should make 5 or 10 “first” duplicates and make 5 or 10 duplicates off
of each of them. This is a classic example of why your key machine should always be maintained in
perfect depth and space adjustment.
Cutter Leaves Ridges on Cut Key
This situation is related to the example above. The cutter wheel is made with a dead-sharp edge or
point. You will always get ridges on the cut surface when the cutter has sharp pointed teeth The ridges
will get smoother as the cutter wears—until finally you have to buy a new cutter or get the old cutter
resharpened. When you put on the new or resharpened cutter you’re back to ridges again.
Machine Makes Whirring Sound
There are four possible causes.
1. The sound is coming from the ball bearing belt tension idler. This idler pushes against the
backside of the drive belt—the backside of the drive belt is ridged and some belts used have
large ridges than others. The sound comes from the idler rolling against these ridges on the
drive belt. It’s O.K.
Содержание RY256
Страница 2: ...2...