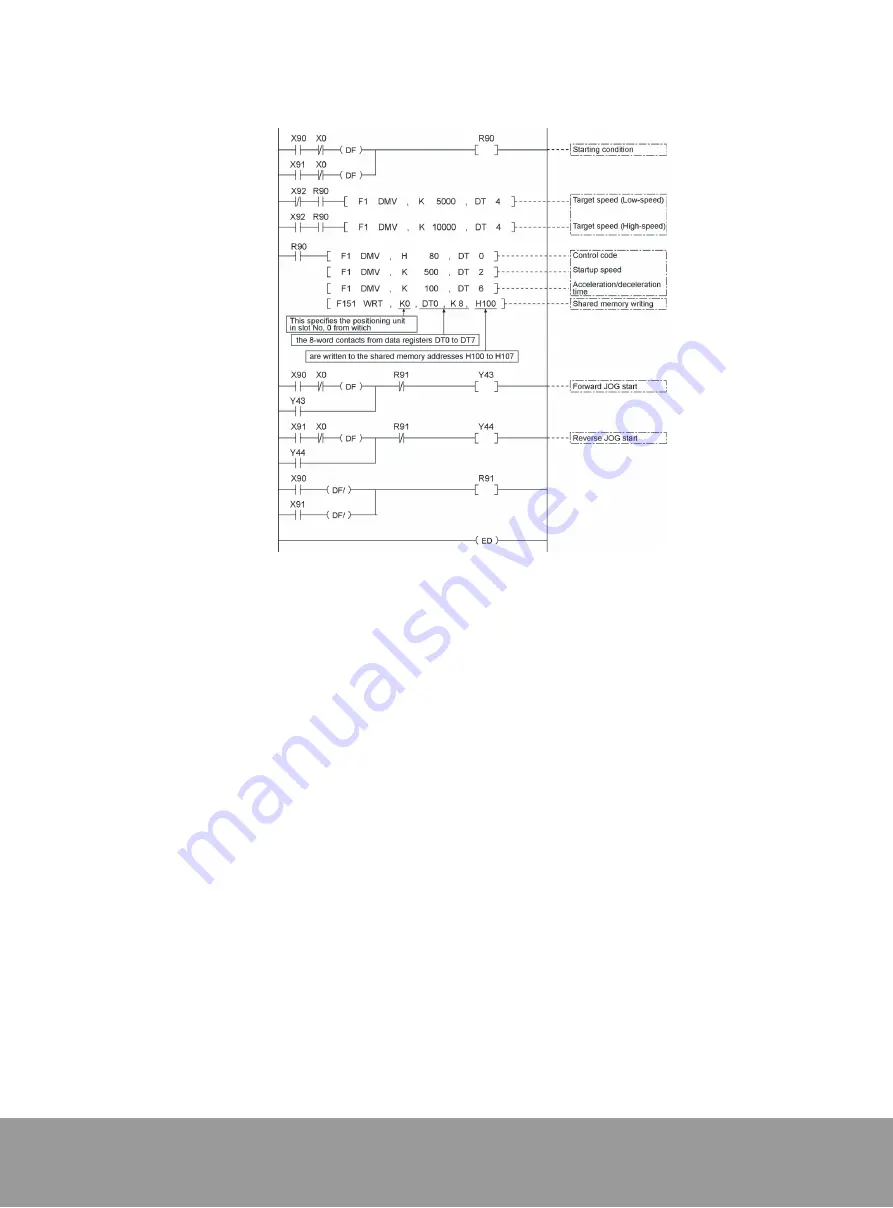
98
Program
Precautions concerning the program
The same shared memory areas to which the various control parameters are
written are used for acceleration/deceleration control, JOG positioning
operation, home return, and other types of control. These should not be
overwritten by other conditions.
If the values for the startup speed, the target speed, or the acceleration/
deceleration time exceed the range of values which can be specified, a set value
error will occur, and operation cannot be initiated.
The number of the start flag varies depending on the number of axes the unit
has, and the installation position. Refer to Chapter 1.
The specified slot number and shared memory address vary depending on the
slot position and axis number of the positioning unit. Refer to Chapter 1.
If forward and reverse rotation are started at the same timing, forward rotation
takes precedence. Also, if one or the other is started first, rotation in that
direction takes precedence.
Содержание NX-POSI1
Страница 1: ...Catalog Number s NX70 POSIx NX POSIx NX70 700 Position User Manual ...
Страница 6: ...6 ...
Страница 14: ...14 ...
Страница 22: ...22 ...
Страница 38: ...38 ...
Страница 64: ...64 ...
Страница 79: ...79 Program ...
Страница 82: ...82 Program ...
Страница 106: ...106 Pulse output diagram ...
Страница 107: ...107 Sample Program ...
Страница 110: ...110 ...
Страница 123: ...123 Action of the I O Flag Before and After a Home Return Operation Return Operation ...
Страница 132: ...132 ...
Страница 145: ...145 11 Deceleration Stop and Forced Stop Sample Program In progress Stopping Emergency Stopping Overrun ...
Страница 147: ...147 Pulse output diagram Deceleration stop operation In progress stop ...
Страница 148: ...148 Forced stop operation Emergency stop Overrun ...
Страница 158: ...158 ...
Страница 170: ...170 ...
Страница 178: ...178 Oriental Motor Co Ltd UPK W Series Open collector output stepping drive connection ...
Страница 179: ...179 NX700 PLC External Dimensions 1 System Dimensions mm Motherboard Installation Diagram mm ...
Страница 180: ...180 2 CPU I O Analog Unit Dimensions mm 3 Special Unit Dimensions mm ...
Страница 183: ...183 Program ...
Страница 187: ...187 Program ...
Страница 188: ...188 ...
Страница 194: ...Publication NX700 UM007A PositionA EN December 2010 ...
Страница 195: ......
Страница 196: ...Copyright 2010 RS Automation Co Ltd All rights reserved ...