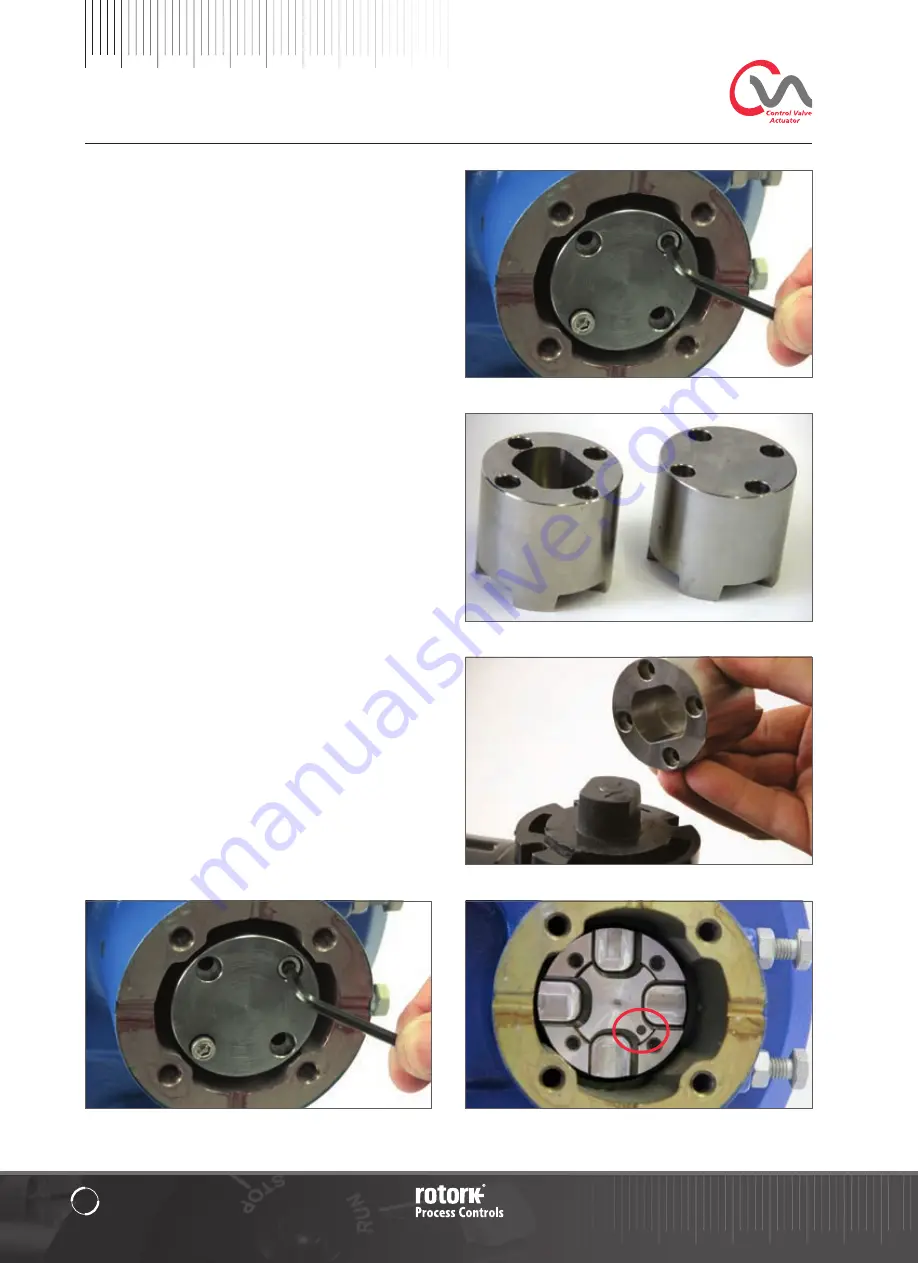
14
Mounting the Actuator
Prepare Drive Bush
Remove four caphead screws securing the blank drive bush.
Machine drive bush to suit valve stem. Ensure machined
position allows correct orientation of actuator to valve flange
and direction to close the valve.
Fitting the Drive Bush
Note: The drive bush can be fitted in four possible positions
90 degrees apart.
Check the Drive bush for fit and orientation against the valve
stem before assembly.
Whilst the Drive Bush is removed it is possible to note the
position of the actuator output shaft.
Fig 16.4 shows the actuator output shaft position indent
(circled) in the ‘Clockwise Closed’ position.
Fit the drive bush in to centre column assembly ensuring
that the stem orientation, actuator position and direction of
operation are correct for valve operation. Secure the drive
bush with cap screws supplied.
Fig. 16.1
Fig. 16.2
Fig. 16.3
Fig. 16.4
Installation & Setup Guide
Fig. 16.4
Содержание CVQ 1200
Страница 2: ...2...