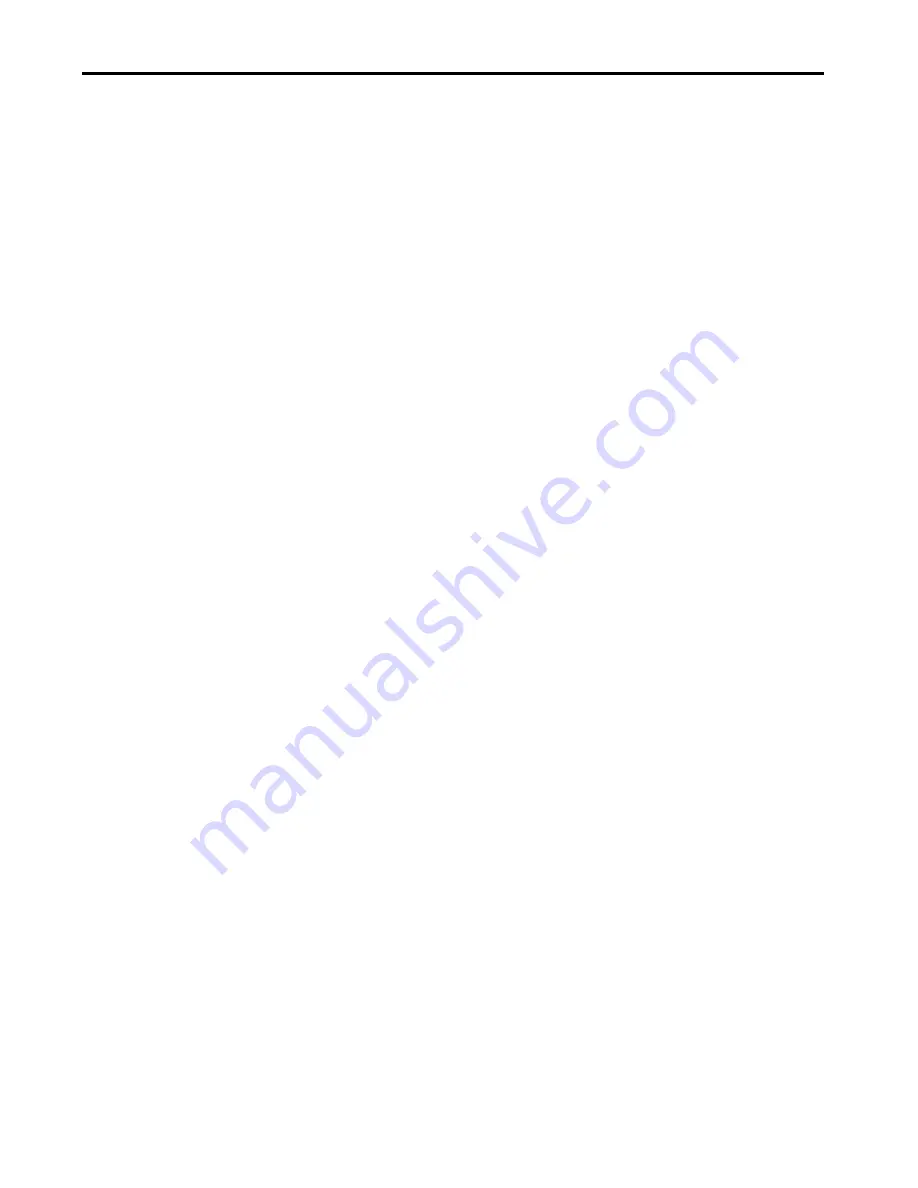
Rockwell Automation Publication LDAT-UM001A-EN-P - April 2016
39
Commission
Chapter 4
Typically, the fold back causes a closed-loop servo system to operate with
reduced dynamic control performance, particularly when accelerating and
decelerating. If the reduced dynamic control results in undesirable Position
Error and the Position Error Tolerance is set to large value, such as, the default
value, the increase in Position Error can go undetected. If proper precautions
are not in place, it could lead to equipment damage and serious injury.
Prevent Reduced Dynamic Control Performance
To prevent reduced dynamic control, take normal motion system precautions
and monitor the drive motor capacity.
Normal motion system precautions include:
• Interlocks for access
• Range of motion hardware and software limits
• Use Motion Analyzer to size your motor and drive combination with
sufficient margin.
We recommend that you monitor motor capacity when commissioning
the axis
Additionally, monitor the drive motor capacity in case of unexpected
obstruction or axis mechanical failures. Take the following precautions to
monitor the motor capacity.
• Make sure the Position Error Tolerance is set appropriately for your axis.
• Turn on Motor Capacity Real Time Attribute on the Axis Properties
Drive/Motor tab.
• Determine your worst case expected axis.MotorCapacity during normal
axis operation.
• In your application run-time code, monitor the axis.MotorCapacity
Real Time attribute. Drive foldback occurs when axis.MotorCapacity
reaches 108% of rated continuous torque.
• Implement a program that brings your axis to a controlled stop before
axis.MotorCapacity reaches 100%.
Configure Your Kinetix 6500
or Kinetix 5500 Drive with
Logix Designer Application
For linear thrusters powered by a Kinetix 6500 drive and linear thrusters with
an absolute encoder powered by a Kinetix 5500 drive, use the next four
sections to configure, hookup test, tune, fine-tune and configure homing for
the linear thruster.
Linear thrusters with the absolute encoder option powered by a Kinetix 5500
drive require the use of the DSL Converter Kit, catalog number 2198-
H2DCK, feedback connector.
The procedures assume the linear thruster and a servo drive have been installed
and wired as one axis of the motion system.
Содержание Allen-Bradley LDAT-S03 Series
Страница 6: ...6 Rockwell Automation Publication LDAT UM001A EN P April 2016 Table of Contents Notes...
Страница 50: ...50 Rockwell Automation Publication LDAT UM001A EN P April 2016 Chapter 4 Commission Notes...
Страница 75: ...Rockwell Automation Publication LDAT UM001A EN P April 2016 75 Index Notes...