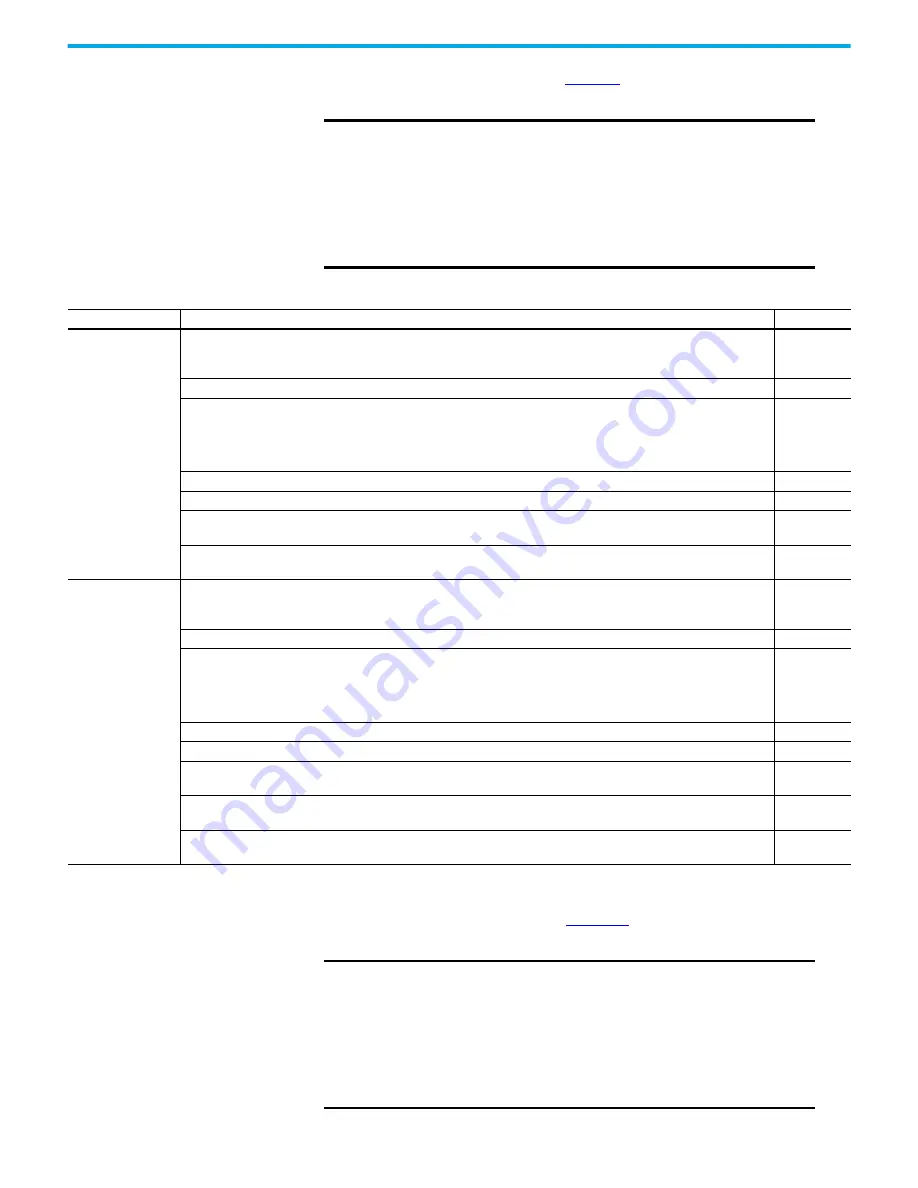
Rockwell Automation Publication 35-UM001A-EN-P - May 2022
213
Appendix A Integrated Safety Instruction Validation Checklist
Safely-limited Speed (SLS)
Use the SLS instruction checklist in
to verify normal operation and
the abnormal operation scenarios.
Safely-limited Position
(SLP)
Use the SLP instruction checklist in
to verify normal operation and
the abnormal operation scenarios.
IMPORTANT
Perform I/O verification and validation before validating your
safety ladder program. SFX instruction must be verified within
your application.
When possible, use immediate operands for instructions to
reduce the possibility of systematic errors in your ladder
program.
Instruction operands must be verified for your safety ladder
program.
Table 99 - SLS Instruction Checklist
Test Type
Test Description
Test Status
Normal Operation
Initiate a Start command.
• Verify that the machine is in a normal machine run condition
• Verify proper machine status and safety application program status
Operate the machine within the desired speed range.
Set up a trend with expected time scale and the following tags to graphically capture this information:
SFX_Name
.ActualSpeed
SLS_Name
.SLSLimit
SLS_Name
.ActiveLimit
SLS_Name
.Output 1
Initiate SLS demand.
Verify that the drive achieves the speed below the
SLS_Name
.ActiveLimit without asserting the
SLS_Name
.SLSLimit output.
While the system is in SLS monitoring state and with the sensor subsystems in a safe state, remove the SLS demand.
• Verify proper machine status and safety application program status
Resume normal machine operation.
• Verify proper machine status and safety application program status
Abnormal Operation 1
Initiate a Start command.
• Verify that the machine is in a normal machine run condition
• Verify proper machine status and safety application program status
Operate the machine within the normal speed range.
Set up a trend with expected time scale and the following tags to graphically capture this information:
SFX_Name
.ActualSpeed
SLS_Name
.SLSLimit
SLS_Name
.ActiveLimit
SLS_Name
.Output 1
Initiate SLS demand.
Verify that the drive achieves the speed below the
SLS_Name.
ActiveLimit without asserting the
SLS_Name
.SLSLimit output.
While the system is in the SLS monitoring state, initiate a motion command that violates the
SLS_Name
.ActiveLimit.
• Verify that the
SLS_Name
.SLSLimit output is asserted and the programmed stop action is initiated
While the system is stopped with the sensor subsystems in a safe state, initiate a Start command.
• Verify proper machine status and safety application program status
While the system is stopped, initiate a Reset command.
• Verify proper machine status and safety application program status
IMPORTANT
Perform I/O verification and validation before validating your
safety ladder program. SFX instruction must be verified within
your application.
When possible, use immediate operands for instructions to
reduce the possibility of systematic errors in your ladder
program.
Instruction operands must be verified for your safety ladder
program.
Содержание Allen-Bradley 35E
Страница 10: ...10 Rockwell Automation Publication 35 UM001A EN P May 2022 Table of Contents Index 223 ...
Страница 222: ...222 Rockwell Automation Publication 35 UM001A EN P May 2022 Appendix B Configure a Message Instruction Notes ...
Страница 225: ...Rockwell Automation Publication 35 UM001A EN P May 2022 225 Armor PowerFlex AC Drives User Manual ...