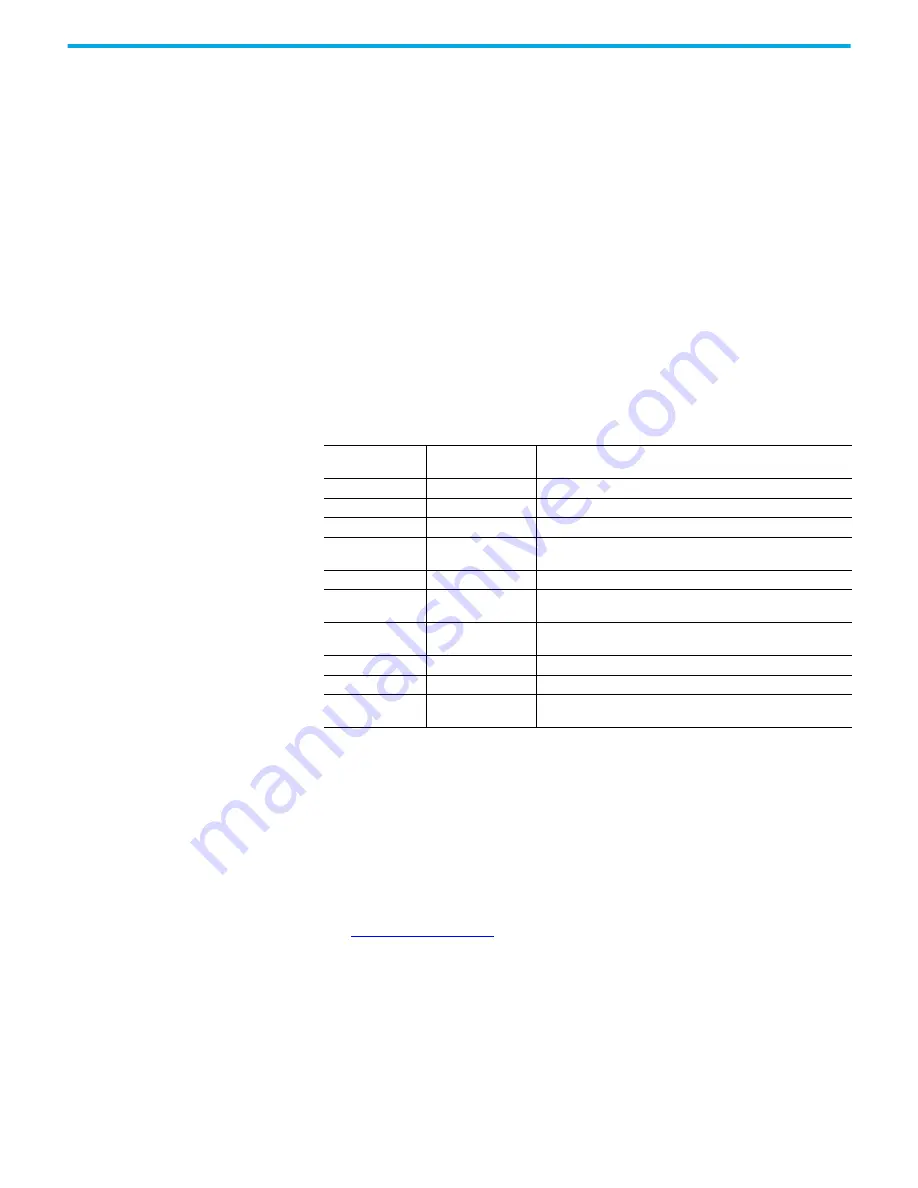
Rockwell Automation Publication 35-UM001A-EN-P - May 2022
119
Chapter 6 Safety Functions
SLS, SLP, and SDI Faults
The drive does not support drive-based SS2, SOS, SLS, SLP, and SDI safe stop/
safety limit functions. The safety controller supports the SLS, SLP, and SDI
safety function instructions. If the drive reports one of these faults, then the
safety controller detected the fault and reported to the drive over the safety
output connection, or the request tag was set through the safety output
assembly. Additional information for these faults must be obtained from the
safety controller that is associated with the drive. In addition, the safety
controller is responsible for issuing a torque disable request.
Safety Feedback Faults
When configured for safety feedback, the drive performs periodic diagnostics
to make sure that the feedback device is operating correctly. Use an explicit
message to read the fault type information from the drive. For example, if an
error is detected, the Safe Feedback object (class code 0x58) updates the
Feedback Fault Reason attribute (attribute ID 0x09) with the reason for the
fault.
Safety Fault Reset
If the drive detects a fault, the input assembly tag
device
:SI.SafetyFault is set
to one.
A Safety Fault can result from the SS1 stopping function, STO function, safety
feedback, SBC function, or other safety diagnostics.
To acknowledge or clear this fault, remove the source of the safety fault and
send a fault reset to the safety logic.
See
for more information about the Integrated Safety
Functions option module, state restart functionality.
Table 38 - Safety Feedback Faults
Safety Feedback
Fault Reason Value
Safety Feedback
Fault Reason Name
Description
1
No Fault
No Fault is present.
2
Invalid Configuration
The encoder's configuration is invalid.
3
Exceeded Max Speed
The encoder speed has exceeded the configured maximum speed.
4
Exceeded Max
Acceleration
The encoder acceleration has exceeded the configured maximum
acceleration.
5
Sin²+Cos² Error
The encoder has failed the vector length or aspect ratio checks.
6
Quadrature Error
The encoder has exceeded the maximum number of quadrature
signal errors.
9
Supply Voltage Error
The associated dual channel feedback instance has detected a fault
in the other encoder
11
Feedback Signal Loss
A feedback signal is missing, shorted, or open.
107
Max input frequency
Max Frequency of the configured encoder has been exceeded.
109
Position Rollover
Position has exceeded the maximum value supported by this
product. Please reset the device
Содержание Allen-Bradley 35E
Страница 10: ...10 Rockwell Automation Publication 35 UM001A EN P May 2022 Table of Contents Index 223 ...
Страница 222: ...222 Rockwell Automation Publication 35 UM001A EN P May 2022 Appendix B Configure a Message Instruction Notes ...
Страница 225: ...Rockwell Automation Publication 35 UM001A EN P May 2022 225 Armor PowerFlex AC Drives User Manual ...