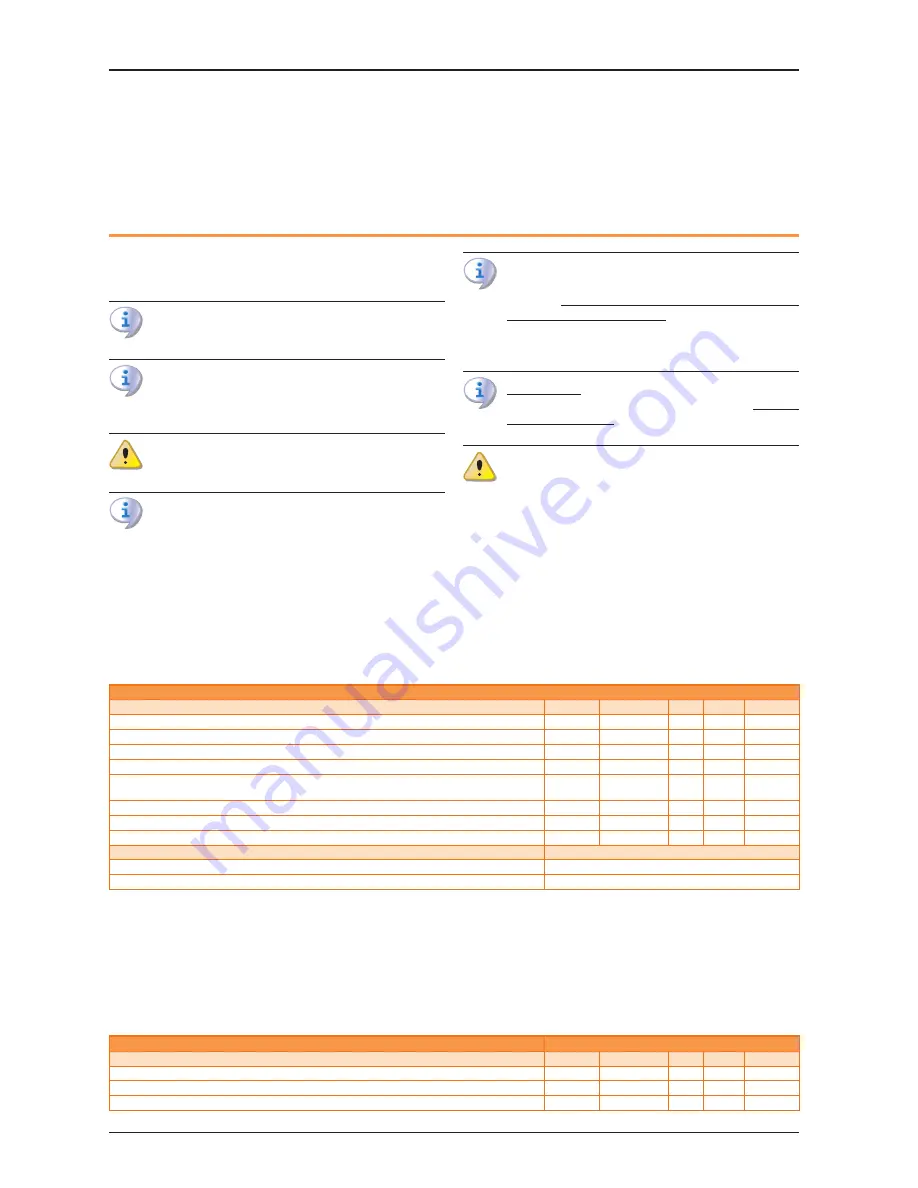
7 Maintenance
Installation, Use and Maintenance Manual – GAHP-A
35
6�7 EFFICIENCY
For increased appliance efficiency:
▶
Keep the finned coil clean;
▶
Adjust the maximum water temperature to the actual sys-
tem requirements;
▶
Reduce repeated switch-ons to the minimum (low loads);
▶
Program appliance activation for actual periods of use;
▶
Keep water and air filters on plumbing and ventilation sys-
tems clean.
7 MAINTENANCE
7�1 WARNINGS
Correct maintenance prevents problems, assures effi-
ciency and keeps running costs low.
Maintenance operations described herein may exclu-
sively be performed by the TAC or skilled maintenance
technician.
Any operation on internal components may exclusively
be performed by the TAC.
Before performing any operation, switch off the appli-
ance by means of the control device (DDC, CCP/CCI or
external request) and wait for the end of the switching
off cycle, then disconnect power and gas supply, by act-
ing on the electrical disconnecter and gas cock.
The efficiency checks and every other "check and
maintenance operation" (see Tables 7.1 p. 35 and
7.2 p. 35) must be performed with a frequency ac-
cording to current regulations or, if more restrictive, ac-
cording to the provisions set forth by the manufacturer,
installer or TAC.
Responsibility for efficiency checks, to be carried out for
the aims of restricting energy consumption, lies with
the system manager.
Heavy-duty use
If the unit is subject to heavy duty use (for example
in process plants or in other conditions of continuous
operation), maintenance operations must be more
frequent.
7�2 PRE-EMPTIVE MAINTENANCE
▶
For pre-emptive maintenance, comply with the recommen-
dations in Table 7.1 p. 35.
Table 7�1
GUIDELINES FOR THE PREVENTIVE MAINTENANCE OPERATIONS
Check of the unit
GAHP-A
GAHP-GS/WS
AY
ACF
GAHP-AR
Visually check of the general condition of the unit and of its air heat exchanger (1)
√
√
√
Check the correct operation of the device used for monitoring the water flow
√
√
√
√
√
Check the % value of CO2
√
√
√
check gas pressure to the burners
√
√
Check that the condensate discharge is clean
[If necessary, frequency of the maintenace operation must be increased]
√
√
√
Replace the belts after 6 years or 12,000 hours of operation
√
√
√
√
Check/restore the pressure of the primary hydronic circuit
√
Check/restore the air pressure inside of the expansion vessel of the primary hydronic circuit
√
Check for every DDC or CCI
DDC or CCI
Check that the plant is able to achive the setpoint temperature
√
Download the hystorical events
√
1 - It is suggested the cleaning of the air heat exchanger once every 4 years [the optimal frequency of this operation is in any case a consequence of
the installation site].
7�3 SCHEDULED ROUTINE MAINTENANCE
▶
For scheduled routine maintenance, perform the operations
in Table 7.2 p. 35, at least once every 2 years.
Table 7�2
SCHEDULED MAINTENANCE OPERATIONS
TO BE PERFORMED AT LEAST ONE EVERY TWO YEARS
Check of the unit
GAHP-A
GAHP-GS/WS
AY
ACF
GAHP-AR
Clean the combustion chamber
√*
√*
√
√
√*
Clean the burner
√*
√*
√
√
√*
Clean the electrodes of ignition and flame sensing
√
√
√
√
√